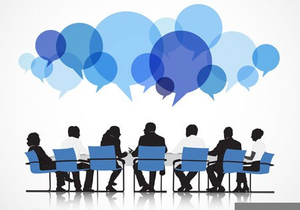
The history behind waste management is extensive. Open-backed carts with horses powered engines were the first vehicles for collection. Motorised versions were first introduced in the 20th Century. Later, closed-top trucks were developed which allowed for the reduction of odours and the easy disposal of refuse. The first truck with a hydraulic compactor was the Garwood Load Packer truck in the 1920s. This invention allowed the truck handle larger amounts of rubbish per collection route. Later, the invention of waste-to–energy led to the modern bin-lorries. In the twentieth century, recycling was also introduced.
Incinerators
Incineration is a waste management technique that uses waste to produce energy. The heat produced by incineration is used as heat to generate steam, which can power a turbine that makes electricity. Typically, an incineration plant produces two-thirds of a megawatt-hour of electricity per tonne of municipal waste. This process can also serve as district heating. A single plant can burn 600 metric tons of waste per day and produce about one ton of ash per day.
In Nottingham, England, was constructed the first British incinerator in 1874. Incinerators were also built in other parts of the country. Many large cities had their own destructors, and the electricity generated from burning rubbish powered sewer pumps and electric refuse collection vehicles.
Dust-yards
The first example of municipal solid-waste management was the 'dustyard' system. It was developed in London's early 19th century. This innovative system was based on household waste (coal ash from domestic fires) and its monetary value. This material was sought after by industries including the brick and agricultural industries. The high market value of this material encouraged dust-contractors and other businesses to collect 100% of their residual waste. This helped to ease the transition from municipal solid waste services to public ones in England.
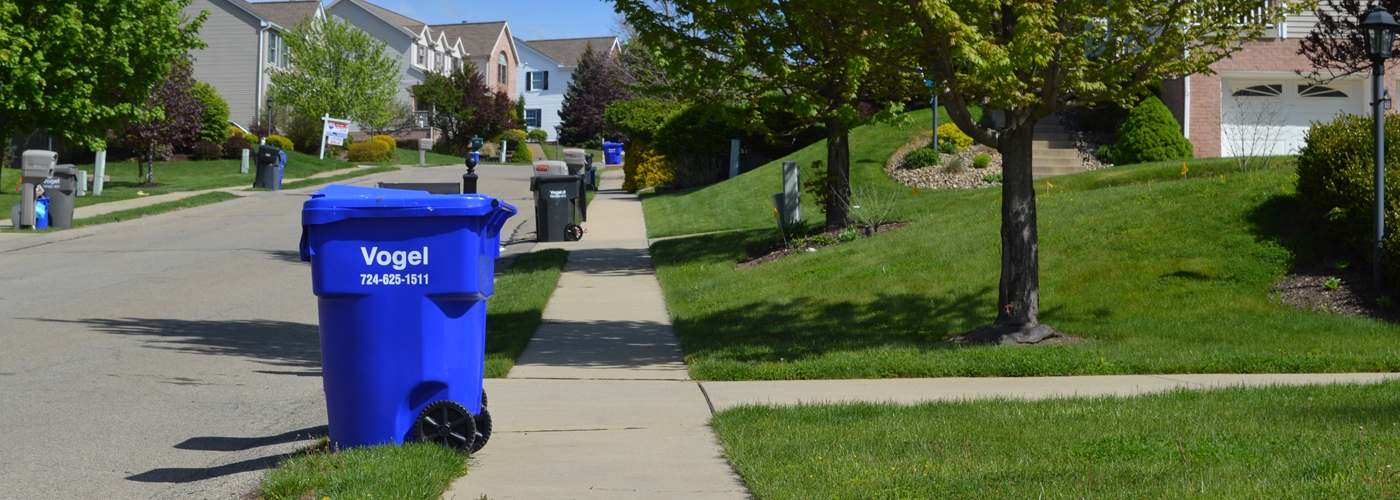
Around 1850, the first system for collecting waste was created. People used a dust-yard or ash-pit to dispose of their garbage. This waste was collected by a crew consisting of two men. The filler was the man who shoved the waste in a basket and the carrier carried it to the cart. The process was repeated until full. The cart was then returned to the dust-yard and passed through a chute. Its contents were then dropped onto the dust heap.
Inflated reserves
Inflation and labor costs are factors that can increase the cost of environmental services. To avoid such expenses, companies should report the depreciation values in their financial statements. This practice can result in overstated reserves on balance sheets, especially for waste management businesses. A company must also record the cost for abandoned or failed landfill development plans.
In 1997, Waste Management's new CEO discovered irregularities. He ordered a complete review of the company’s finances. It was discovered that the company had misrepresented its financial statements by $1.7 million. When the scandal was revealed, the stock price of the company fell by almost a quarter.
Accounting fraud
This past year, a massive accounting fraud at Waste Management was uncovered by the Securities and Exchange Commission. According to the SEC, former Waste Management executives lied about their company's financial performance and inflated profits by up to $1.7 billion. The company was eventually forced to settle a lawsuit in class and pay $7M in civil penalties.
Waste Management used accounting procedures that were inconsistent with generally accepted accounting standards to cover up its fraud. This included deferring expenditures, erasing present expenses, and using other techniques for burying expenses. Waste Management's principal fixed asset was garbage trucks and containers. Therefore, the depreciation expenses for these assets were substantial and easy to manipulate.
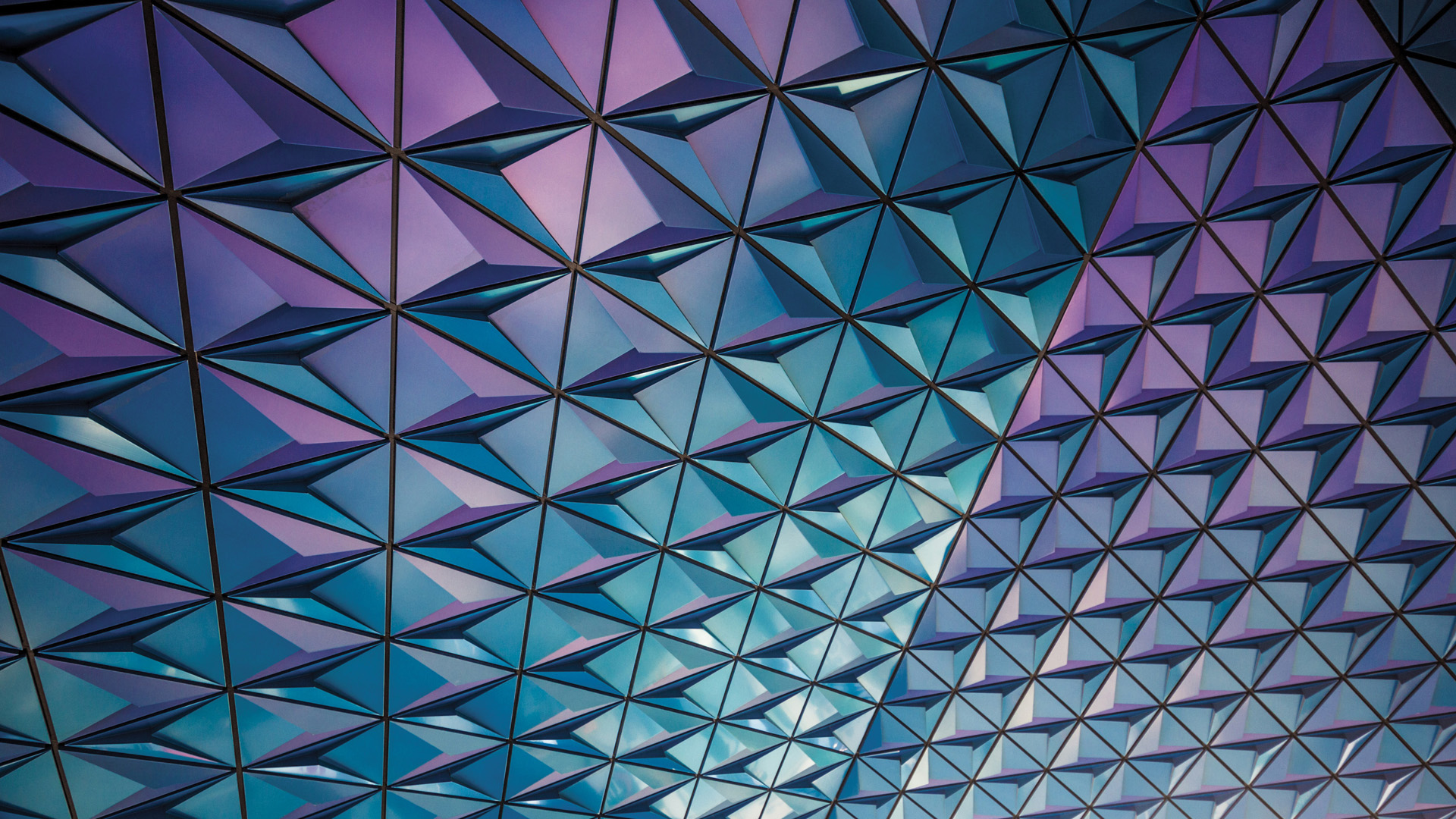
Harvest Power
With its innovative business model, Harvest Power is diverting organic waste from landfills and converting it into multiple value streams. This reduces net greenhouse emissions, lowers total disposal expenses, and slows the consumption of landfill space. It also turns unutilized agricultural inputs into renewable energy. Harvest Power also works with this system to reduce landfill space and promote renewable energie policies.
Harvest Power is already a great success in Spain. And its investors believe the model can easily be transferred to the United States. It raised $110M in funding in 2012 from Al Gore’s Generation Investment Management and Kleiner Perkins. Waste Management, the largest trash processing company in the country, has also invested. They have pledged to eliminate all landfills.
FAQ
How do you manage your employees effectively?
Achieving employee happiness and productivity is key to managing them effectively.
It means setting clear expectations for them and keeping an eye on their performance.
Managers must be clear about their goals and those of their teams in order to succeed.
They should communicate clearly to staff members. And they need to ensure that they reward good performance and discipline poor performers.
They will also need to keep records about their team's activities. These include:
-
What was accomplished?
-
How much work were you able to accomplish?
-
Who did it?
-
What was the moment it was completed?
-
Why it was done?
This information can be used to monitor performance and evaluate results.
What is Six Sigma and how can it help you?
It is a way to improve quality that places emphasis on customer service and continuous learning. This is an approach to quality improvement that uses statistical techniques to eliminate defects.
Motorola's 1986 efforts to improve manufacturing process efficiency led to the creation of Six Sigma.
This idea quickly spread throughout the industry. Today, many organizations use six sigma methods for product design, production and delivery.
How do we create a company culture that is productive?
A positive company culture creates a sense of belonging and respect in its people.
It is based on three principles:
-
Everyone has something valuable to contribute
-
Fair treatment of people is the goal
-
There is mutual respect between individuals and groups
These values reflect in how people behave. They will treat others with respect and kindness.
They will be respectful of the opinions of other people.
And they will encourage others to share ideas and feelings.
The company culture promotes collaboration and open communication.
People can freely express their opinions without fear or reprisal.
They know that they will not be judged if they make mistakes, as long as the matter is dealt with honestly.
Finally, the company culture promotes honesty and integrity.
Everyone knows that they must always tell the truth.
Everyone recognizes that rules and regulations are important to follow.
No one is entitled to any special treatment or favors.
What are the four major functions of Management?
Management is responsible of planning, organizing, leading, and controlling people as well as resources. It includes the development of policies and procedures as well as setting goals.
Management aids an organization in reaching its goals by providing direction and coordination, control, leadership motivation, supervision, training, evaluation, and leadership.
These are the four major functions of management:
Planning – Planning involves deciding what needs to happen.
Organizing - Organization involves deciding what should be done.
Directing - Directing means getting people to follow instructions.
Controlling – This refers to ensuring that tasks are carried out according to plan.
What are management concepts?
Management concepts are the principles and practices used by managers to manage people, resources. They cover topics such as job descriptions and performance evaluations, human resource policies, training programs, employee motivation, compens systems, organizational structure, among others.
Statistics
- The BLS says that financial services jobs like banking are expected to grow 4% by 2030, about as fast as the national average. (wgu.edu)
- As of 2020, personal bankers or tellers make an average of $32,620 per year, according to the BLS. (wgu.edu)
- Our program is 100% engineered for your success. (online.uc.edu)
- The average salary for financial advisors in 2021 is around $60,000 per year, with the top 10% of the profession making more than $111,000 per year. (wgu.edu)
- This field is expected to grow about 7% by 2028, a bit faster than the national average for job growth. (wgu.edu)
External Links
How To
How do you do the Kaizen method?
Kaizen means continuous improvement. Kaizen is a Japanese concept that encourages constant improvement by small incremental changes. It's a team effort to continuously improve processes.
Kaizen, a Lean Manufacturing method, is one of its most powerful. Employees responsible for the production line should identify potential problems in the manufacturing process and work together to resolve them. This increases the quality of products and reduces the cost.
The main idea behind kaizen is to make every worker aware of what happens around him/her. To prevent problems from happening, any problem should be addressed immediately. Report any problem you see at work to your manager.
There are some basic principles that we follow when doing kaizen. Always start with the end product in mind and work our way back to the beginning. If we want to improve our factory for example, we start by fixing the machines that make the final product. Then, we fix the machines that produce components and then the ones that produce raw materials. Then, we fix those who work directly with the machines.
This method is known as kaizen because it focuses upon improving every aspect of the process step by step. After we're done with the factory, it's time to go back and fix the problem.
It is important to understand how to measure the effectiveness and implementation of kaizen in your company. There are several ways to determine whether kaizen is working well. One method is to inspect the finished products for defects. Another way to find out how productive your company has been since you implemented kaizen is to measure the increase in productivity.
If you want to find out if your kaizen is actually working, ask yourself why. You were trying to save money or obey the law? Did you really believe that it would be a success factor?
Let's say you answered yes or all of these questions. Congratulations! You're now ready to get started with kaizen.