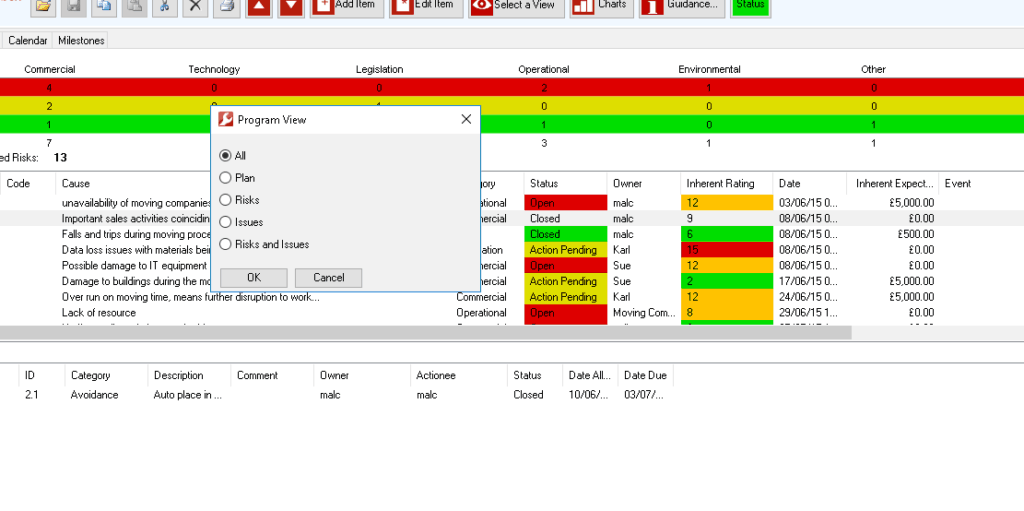
The success of a STEM-related project depends on the ability to create a framework for interprofessional collaboration. It allows members of the team to identify a problem together and to develop strategies to fix it. The team members present a brief report summarizing their findings to students. This helps them practice oral communication.
Framework for interprofessional teamwork
Framework for inter-professional teamwork (or framework for interprofessional teamwork) is a theoretical approach to improving inter-professional collaboration in primary healthcare. It takes into account a range of factors and draws on the findings of many research studies. The framework is comprised of six key themes. These relate to team structure, synergy among members, definition of roles and responsibility, competence of members to carry out designated tasks, and the organisational context that supports teamwork.
It is essential to define the roles and activities for each member of a PHC team in order to encourage teamwork. The CN and GP roles in team care are often ambiguous, leading to conflict and mutual dissatisfaction. CNs are frequently in a state that is unclear. Their involvement in patient-care is often limited, which can lead to conflict.
Templates
Creating a template for a project is a great way to make the process of project collaboration easier. A template can serve as a roadmap or repository for the team. It gives them a guideline for what to do, and who to contact. It keeps them on track. This is how you can create a template.
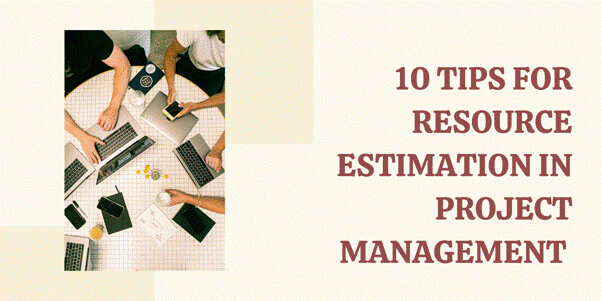
These templates can be customized to fit the needs of your business. These templates help your team streamline processes and save time. These templates can improve team communication, which is crucial for planning and execution. They can also help your team avoid human errors, since they clearly outline the details from the start.
Gantt charts
When working on a project, it can be difficult to track teamwork, especially when there is a high amount of dependencies between tasks. Gantt charts can be helpful in displaying the details of each task and their dependent tasks. The chart will also include the team's responsibilities along with their start and stop dates.
Gantt charts can be useful for project managers as they enable them to view all tasks associated with a project from one place. Gantt charts are great for encouraging team camaraderie and shared responsibility, as well as a desire to succeed. Gantt charts are a great way to visualize project goals and tasks and create an environment where team members can work together to achieve them.
Filtering Tool
The Filtering Tool for Project on Teamwork allows you to select key data from your team's tasks. This tool can be used to determine which tasks have been completed and started. This tool makes it easy to scan through all the data and find what you want.
You can access the filtering tool for project management on Teamwork from various sections of this site. This includes tasks, projects and time logs. Click the filters tab in the top right corner of any section to access this tool. You can also view filters on a user profile, and drag and drop the options to arrange them.
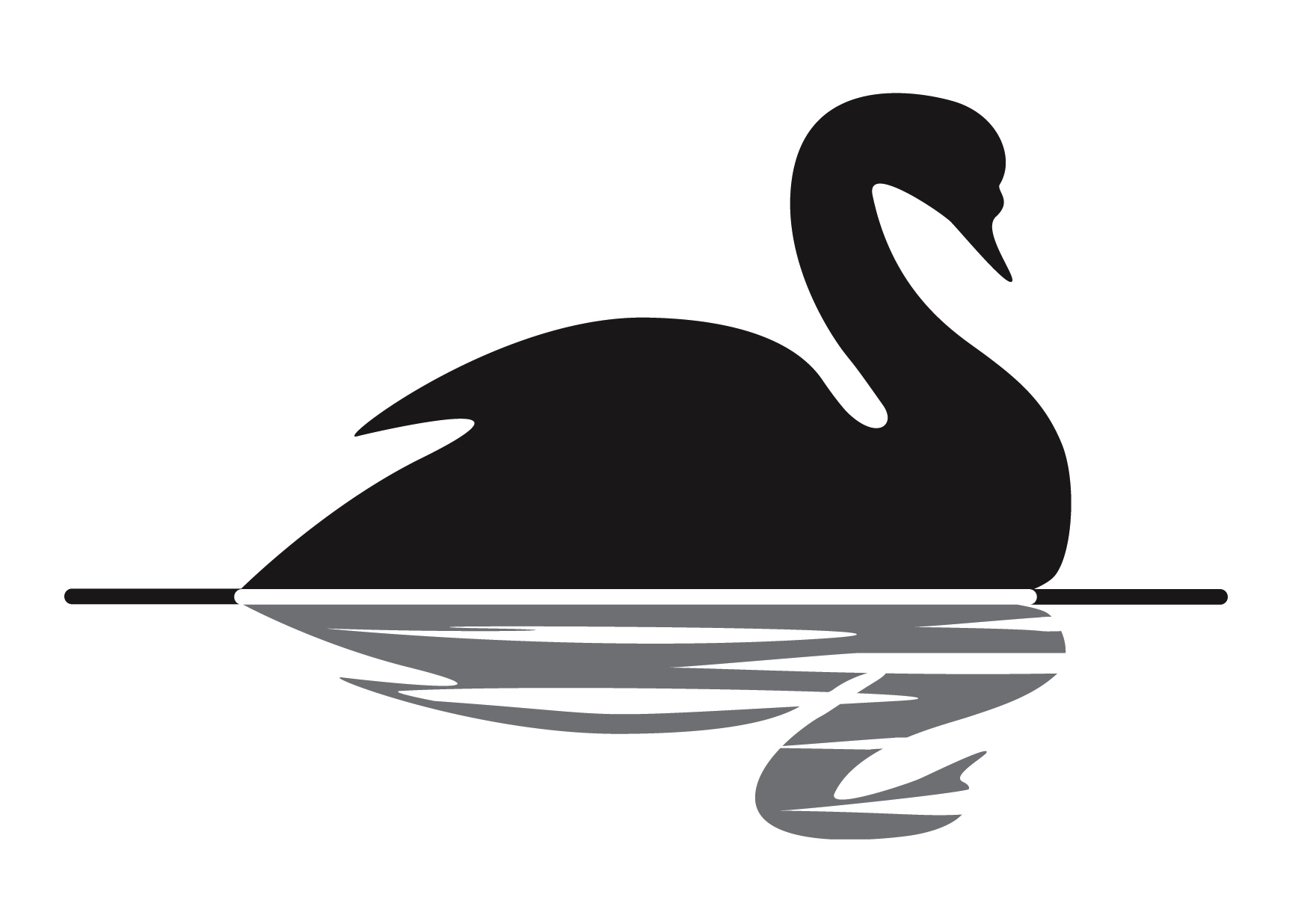
Task list
A task list is a way of grouping all the tasks in a project. Task lists can either be created by adding tasks or by assigning them as individuals, groups and companies to projects. You can either assign due dates to tasks, or you can leave them unassigned. By giving tasks a title and due date, you can add them to the project's tasklist.
To create a new task list in Teamwork, simply click the Add Task List button. Once you have created your task list, you can name it, add notes, set a start date, and even set a due date. You can choose to make your new list public or private.
FAQ
What are the five management process?
These five stages are: planning, execution monitoring, review and evaluation.
Planning involves setting goals for the future. This includes setting goals for the future and defining what you want.
Execution takes place when you actually implement the plans. They must be followed by all parties.
Monitoring is checking on progress towards achieving your objectives. Regular reviews should be done of your performance against targets or budgets.
Every year, there are reviews. They are a chance to see if everything went smoothly during the year. If not, changes may be made to improve the performance next time around.
Following the annual review, evaluation is done. It helps identify which aspects worked well and which didn't. It provides feedback about how people perform.
How do you manage employees effectively?
Managing employees effectively means ensuring that they are happy and productive.
This includes setting clear expectations for their behavior and tracking their performance.
Managers must be clear about their goals and those of their teams in order to succeed.
They need to communicate clearly and openly with staff members. They should also ensure that they both reward high performers and discipline those who are not performing to their standards.
They also need to keep records of their team's activities. These include:
-
What was achieved?
-
How much work was put in?
-
Who did it?
-
When it was done?
-
Why?
This information can be used for monitoring performance and evaluating results.
What role does a manager have in a company's success?
Different industries have different roles for managers.
The manager oversees the day-to-day activities of a company.
He/she ensures the company meets its financial commitments and produces goods/services that customers demand.
He/she ensures employees adhere to all regulations and quality standards.
He/she is responsible for the development of new products and services, as well as overseeing marketing campaigns.
How does a manager motivate their employees?
Motivation is the desire to do well.
Engaging in something fun can be a great way to get motivated.
Or you can get motivated by seeing yourself making a contribution to the success of the organization.
You might find it more rewarding to treat patients than to study medical books if you plan to become a doctor.
Another type of motivation comes from within.
Perhaps you have a strong sense to give back, for example.
You may even find it enjoyable to work hard.
Ask yourself why you aren't feeling motivated.
You can then think of ways to improve your motivation.
Statistics
- Hire the top business lawyers and save up to 60% on legal fees (upcounsel.com)
- Our program is 100% engineered for your success. (online.uc.edu)
- The profession is expected to grow 7% by 2028, a bit faster than the national average. (wgu.edu)
- The average salary for financial advisors in 2021 is around $60,000 per year, with the top 10% of the profession making more than $111,000 per year. (wgu.edu)
- Your choice in Step 5 may very likely be the same or similar to the alternative you placed at the top of your list at the end of Step 4. (umassd.edu)
External Links
How To
What is Lean Manufacturing?
Lean Manufacturing methods are used to reduce waste through structured processes. These processes were created by Toyota Motor Corporation, Japan in the 1980s. The aim was to produce better quality products at lower costs. Lean manufacturing emphasizes removing unnecessary steps from the production process. It includes five main elements: pull systems (continuous improvement), continuous improvement (just-in-time), kaizen (5S), and continuous change (continuous changes). Pull systems involve producing only what the customer wants without any extra work. Continuous improvement means continuously improving on existing processes. Just-in-time is when components and other materials are delivered at their destination in a timely manner. Kaizen stands for continuous improvement. Kaizen can be described as a process of making small improvements continuously. Finally, 5S stands for sort, set in order, shine, standardize, and sustain. These five elements are combined to give you the best possible results.
The Lean Production System
Six key concepts are the basis of lean production:
-
Flow - focuses on moving information and materials as close to customers as possible.
-
Value stream mapping - Break down each stage in a process into distinct tasks and create an overview of the whole process.
-
Five S's, Sort, Set in Order, Shine. Standardize. and Sustain.
-
Kanban – visual signals like colored tape, stickers or other visual cues are used to keep track inventory.
-
Theory of constraints: Identify bottlenecks and use lean tools such as kanban boards to eliminate them.
-
Just-in-time delivery - Deliver components and materials right to your point of use.
-
Continuous improvement: Make incremental improvements to the process instead of overhauling it completely.