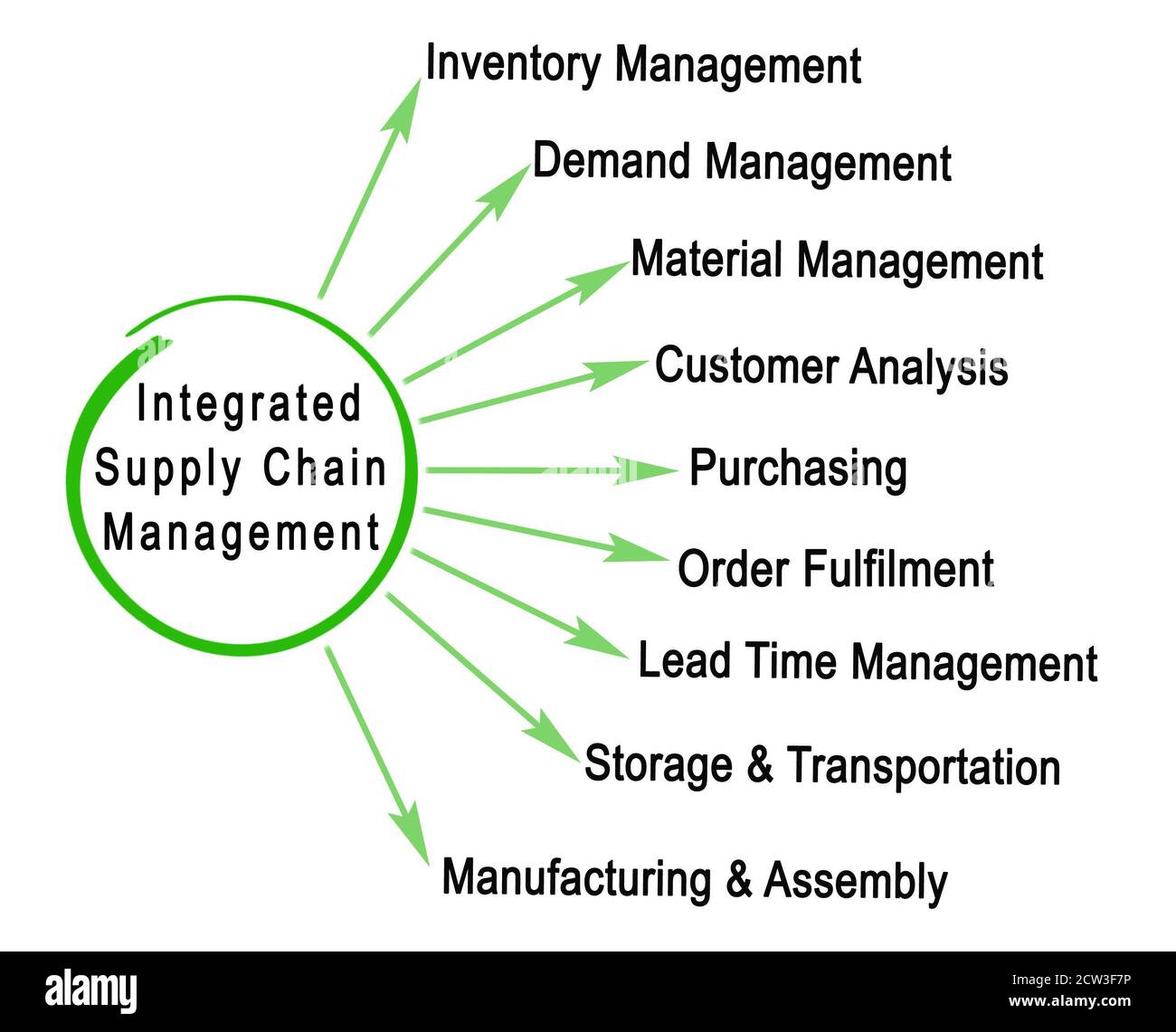
Integrated supply chain management is an integrated approach to managing a company. It involves the management of a business from its "cradle-to-grave" phase. This management approach is characterised in asymmetrical relations between buyers and vendors. Its goal is to improve quality and reduce costs. It involves visibility from all points of the supply chain. This is an important part of fully integrated supply chains. However, not all companies are interested in using such an approach.
Integrated supply chain management can be described as a "cradle–to-grave" approach.
Integrated supply chain management (ISCM) is a holistic concept that covers all aspects in the product life cycle. This includes raw materials and consumer products. It includes forward and reverse logistics, information flows and cash flows. This is typically between producers and distributors and retailers. The ultimate goal here is to minimize waste while maximising benefits for the consumer. Supply chain managers must learn how to make use of outside resources and reuse materials at the end.
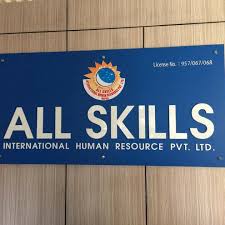
It is characterized by adversarial relationships between buyers and sellers
The integration of supply chain management requires reducing the number transactions and maximising the performance. This requires disciplined management skills and technologies as well as a strong focus on key capabilities. The ultimate goal of the project is to achieve higher profitability while reducing risk for everyone. This is often challenging in the current global economic climate. With some common practices, however, integration of supply chain management can be a cost-effective and efficient strategy.
It reduces costs
Integrated supply chain management can make your business more profitable in many ways. First, make sure that your suppliers fulfill your specifications. Second, ensure that they are able to deliver the goods at a fair price. A good reputation is essential, as well as the ability to deliver your goods on time. This is especially important for those who deal with perishable items. Implementing more efficient supply chain management practices can help increase your business' efficiency.
It improves quality
Integrated supply chain management allows for a single view of the entire supply chain. This centralized view is easy to update without needing hardware and software. It allows for agile and scalable supply chains. Organizations can better plan, collaborate with vendors and optimize their business performance by leveraging real-time information. It's a win/win situation for everyone involved. These are just a handful of the many benefits of integrating your supplier chain.
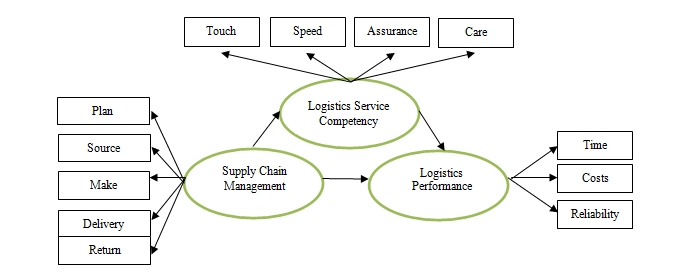
It allows for quick product design, manufacturing, and assembly
Manufacturers now have the ability to design and make complete products in half the time it used take with integrated supply chain administration. This trend can reduce material waste as well as warehouse costs. On-demand production also offers better customer service. Unfortunately, the learning curve is steep. However, you can create products in as little time as one day by using new materials or hardware. It can also improve product quality.
FAQ
What role can a manager fill in a company’s management?
The role of a manager varies from one industry to another.
The manager oversees the day-to-day activities of a company.
He/she ensures the company meets its financial commitments and produces goods/services that customers demand.
He/she is responsible for ensuring that employees comply with all regulations and follow quality standards.
He/she oversees marketing campaigns and plans new products.
Six Sigma is so well-known.
Six Sigma is easy to use and can lead to significant improvements. Six Sigma also gives companies a framework for measuring improvement and helps them focus on what is most important.
What is the difference between leadership and management?
Leadership is all about influencing others. Management is about controlling others.
A leader inspires others while a manager directs them.
Leaders motivate people to succeed; managers keep workers on track.
A leader develops people; a manager manages people.
How can we create a culture of success in our company?
A company culture that values and respects its employees is a successful one.
It is founded on three basic principles:
-
Everyone has something valuable to contribute
-
People are treated fairly
-
It is possible to have mutual respect between groups and individuals
These values reflect in how people behave. For example, they will treat others with courtesy and consideration.
They will listen to other people's opinions respectfully.
They can also be a source of inspiration for others.
In addition, the company culture encourages open communication and collaboration.
People are free to speak out without fear of reprisal.
They know mistakes will be accepted as long as they are dealt with honestly.
The company culture promotes honesty, integrity, and fairness.
Everyone knows that they must always tell truth.
Everyone recognizes that rules and regulations are important to follow.
No one is entitled to any special treatment or favors.
What is TQM?
When manufacturing companies realized that price was not enough to compete, the industrial revolution brought about the quality movement. They had to improve efficiency and quality if they were to remain competitive.
Management responded to the need to improve, and developed Total Quality Management (TQM). This focused on improving every aspect of an organization’s performance. It included continual improvement processes, employee involvement, customer satisfaction, and customer satisfaction.
What are some common management mistakes?
Managers can make their jobs more difficult than necessary.
They may not delegate enough responsibilities to staff and fail to give them adequate support.
Additionally, many managers lack communication skills that are necessary to motivate and direct their teams.
Some managers set unrealistic expectations for their staff.
Managers may prefer to solve every problem for themselves than to delegate responsibility.
What are the three basic management styles?
The three basic management styles are: authoritarian, laissez-faire, and participative. Each style has its own strengths and weaknesses. Which style do yo prefer? Why?
Autoritarian – The leader sets the direction for everyone and expects them to follow. This style works best in large organizations that are stable and well-organized.
Laissez-faire: The leader lets each person decide for themselves. This style is most effective when the organization's size and dynamics are small.
Participative: The leader listens to everyone's ideas and suggestions. This style is most effective in smaller organizations, where everyone feels valued.
Statistics
- Your choice in Step 5 may very likely be the same or similar to the alternative you placed at the top of your list at the end of Step 4. (umassd.edu)
- This field is expected to grow about 7% by 2028, a bit faster than the national average for job growth. (wgu.edu)
- The average salary for financial advisors in 2021 is around $60,000 per year, with the top 10% of the profession making more than $111,000 per year. (wgu.edu)
- The BLS says that financial services jobs like banking are expected to grow 4% by 2030, about as fast as the national average. (wgu.edu)
- 100% of the courses are offered online, and no campus visits are required — a big time-saver for you. (online.uc.edu)
External Links
How To
What is Lean Manufacturing?
Lean Manufacturing is a method to reduce waste and increase efficiency using structured methods. They were developed in Japan by Toyota Motor Corporation (in the 1980s). The main goal was to produce products at lower costs while maintaining quality. Lean manufacturing focuses on eliminating unnecessary steps and activities from the production process. It is composed of five fundamental elements: continuous improvement; pull systems, continuous improvements, just-in–time, kaizen, continuous change, and 5S. Pull systems allow customers to get exactly what they want without having to do extra work. Continuous improvement is the continuous improvement of existing processes. Just-in-time refers to when components and materials are delivered directly to the point where they are needed. Kaizen stands for continuous improvement. Kaizen can be described as a process of making small improvements continuously. Five-S stands for sort. It is also the acronym for shine, standardize (standardize), and sustain. These five elements are combined to give you the best possible results.
Lean Production System
The lean production system is based on six key concepts:
-
Flow: The goal is to move material and information as close as possible from customers.
-
Value stream mapping: This is a way to break down each stage into separate tasks and create a flowchart for the entire process.
-
Five S's: Sort, Shine Standardize, Sustain, Set In Order, Shine and Shine
-
Kanban is a visual system that uses visual cues like stickers, colored tape or stickers to keep track and monitor inventory.
-
Theory of Constraints - Identify bottlenecks in the process, and eliminate them using lean tools such kanban boards.
-
Just-intime - Order components and materials at your location right on the spot.
-
Continuous improvement - incremental improvements are made to the process, not a complete overhaul.