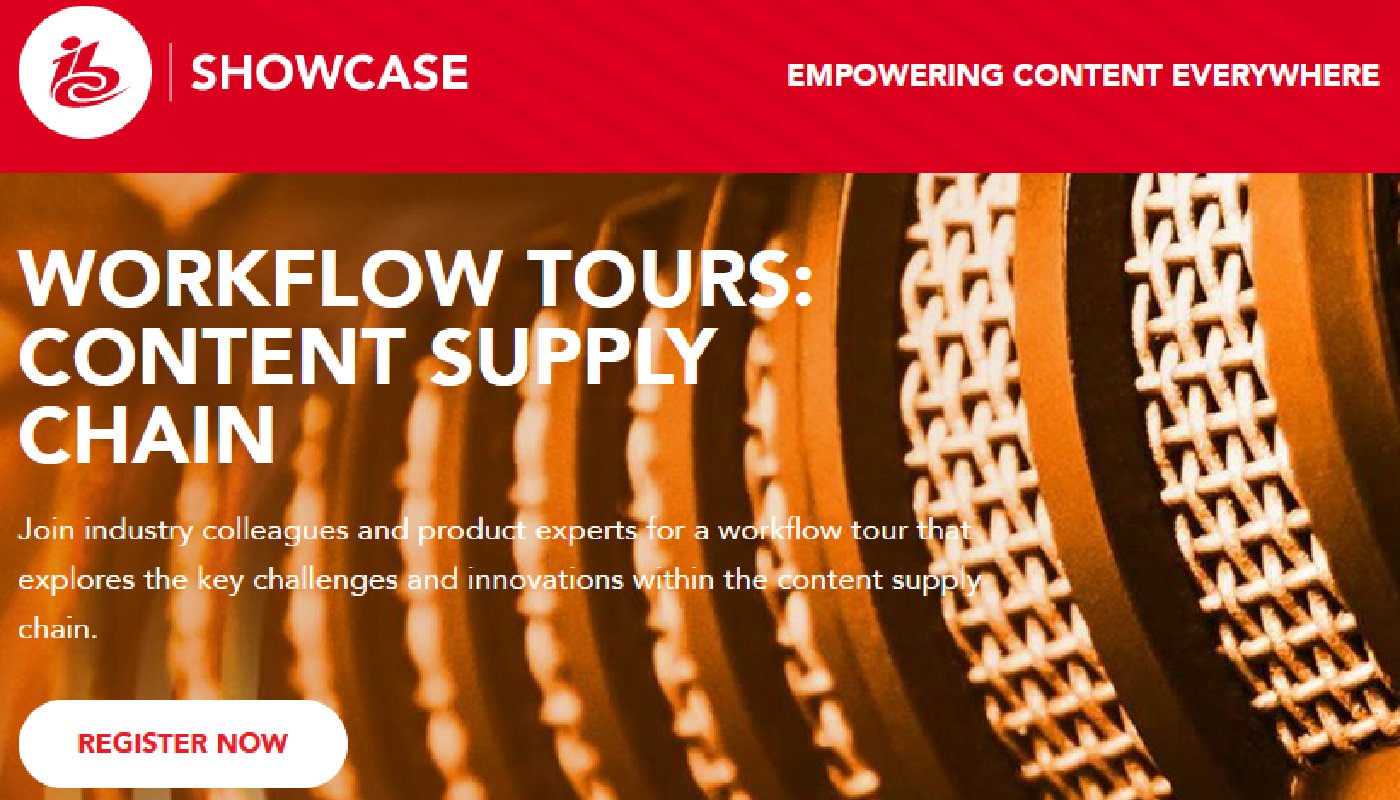
Clark Construction is a well-respected general contractor in the United States. Interns can expect to be taught by some of the most skilled construction professionals in this industry. Additionally, associate positions at Clark provide real-world hands-on construction experiences that prepare future construction professionals for careers in the field. You'll be able learn from some of the top construction professionals and take part in some of the most important construction projects in the nation.
Duties of the job
Clark Construction internships are a great way to learn from top-notch construction professionals. As an intern at Clark Construction, you will have the opportunity learn from the best construction professionals in the country. You will also be involved with some of the nation's most prestigious projects. These internships provide valuable hands-on experience and a realistic look at construction.
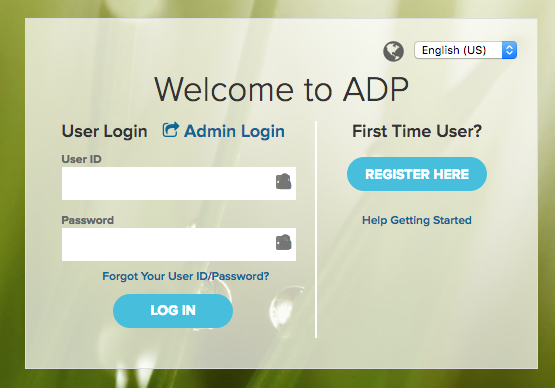
You will have the opportunity to do internships on the jobsite, as well as work in various corporate departments. Clark will teach you how to build buildings and make a positive impact on the world. There are numerous opportunities for Virtual Design & Construction, Research & Development, Design & Scheduling, Safety, sustainability, and Talent Management.
Salary
Clark Construction Group's salaries are competitive. They are ranked in the top 15 per cent of US companies based on their compensation and perks. Clark Construction Group has a very positive work environment, and most employees are happy with their jobs. The company is much more satisfied than its competitors and has a lower turnover rate. Clark Construction Group offers many additional benefits, including a paid internship.
Clark Construction Group offers an average salary of $106,341 a year, or $51 per hours. It varies depending on position, education, and department. For example, the highest paid position is Director of Operations, which pays $331,673 annually, while the lowest paying position is an Admin Assistant, which pays $50,345 per year. The department-specific salary ranges can be found below. For example, the salaries of the Director for HR and Marketing departments are on average $1128,811 and $88,113.
Location
Clark Construction could be the right place for you if you're searching for internships. Clark Construction is consistently ranked among the top general contractors in the country. Clark is a top-rated construction company that builds some of America's most notable projects. This internship will give you a true understanding of construction and valuable hands-on experience.
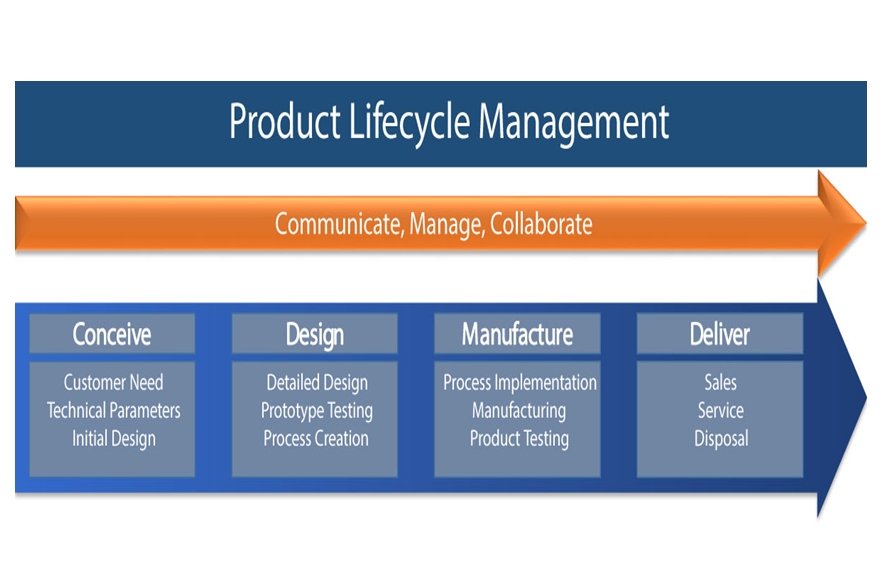
Clark Construction Group's employees are very happy at work. 86% report they love their jobs. In addition, only 20% of Clark Construction Group employees work less than eight hours a day. Clark Construction Group ranks third for overall company culture. Its employees generally enjoy their work and are satisfied with their benefits.
FAQ
What are management theories?
Management concepts are the practices and principles managers use to manage people or resources. They cover topics such as job descriptions and performance evaluations, human resource policies, training programs, employee motivation, compens systems, organizational structure, among others.
What is Six Sigma?
It's a strategy for quality improvement that emphasizes customer care and continuous learning. The goal is to eliminate defects by using statistical techniques.
Motorola's 1986 efforts to improve manufacturing process efficiency led to the creation of Six Sigma.
The idea spread quickly throughout the industry, and today, many organizations are using six sigma methods to improve product design, production, delivery, and customer service.
What is a simple management tool that aids in decision-making and decision making?
A decision matrix can be a simple, but effective tool to assist managers in making decisions. They can think about all options and make informed decisions.
A decision matrix can be used to show alternative options as rows or columns. It is easy to see how each option affects the other options.
In this example, there are four possible options represented by boxes on the left-hand side of the matrix. Each box represents an option. The top row represents the current state of affairs, and the bottom row is indicative of what would happen in the event that nothing were done.
The effect of Option 1 can be seen in the middle column. In this case, it would mean increasing sales from $2 million to $3 million.
The next two columns show the effects of choosing Options 2 and 3. These positive changes can increase sales by $1 million or $500,000. But, they also have some negative consequences. Option 2, for example, increases the cost by $100 000 while Option 3 decreases profits by $200 000.
Finally, the last column shows the results of choosing Option 4. This results in a decrease of sales by $1,000,000
A decision matrix has the advantage that you don’t have to remember where numbers belong. Simply look at the cells to instantly determine if one choice is better than the other.
The matrix has already done all of the work. It is as simple a matter of comparing all the numbers in each cell.
Here is an example how you might use the decision matrix in your company.
Advertising is a decision that you make. If you do, you'll be able to increase your revenue by $5 thousand per month. However, additional expenses of $10 000 per month will be incurred.
Look at the cell immediately below the one that states "Advertising" to calculate the net investment in advertising. It's $15,000. Advertising is worth much more than the investment cost.
What is the difference between project and program?
A program is permanent while a project can be temporary.
A project has usually a specified goal and a time limit.
It is usually done by a group that reports back to another person.
A program usually has a set of goals and objectives.
It is often implemented by one person.
What are the five management process?
The five stages of any business are planning, execution, monitoring, review, and evaluation.
Setting goals for the future is part of planning. Planning involves defining your goals and how to get there.
Execution happens when you actually do the plan. They must be followed by all parties.
Monitoring is the act of monitoring your progress towards achieving your targets. Regular reviews should be done of your performance against targets or budgets.
At the end of every year, reviews take place. These reviews allow you to evaluate whether the year was successful. If not, changes may be made to improve the performance next time around.
Following the annual review, evaluation is done. It helps to determine what worked and what didn’t. It also provides feedback regarding how people performed.
Statistics
- UpCounsel accepts only the top 5 percent of lawyers on its site. (upcounsel.com)
- The average salary for financial advisors in 2021 is around $60,000 per year, with the top 10% of the profession making more than $111,000 per year. (wgu.edu)
- This field is expected to grow about 7% by 2028, a bit faster than the national average for job growth. (wgu.edu)
- The profession is expected to grow 7% by 2028, a bit faster than the national average. (wgu.edu)
- Our program is 100% engineered for your success. (online.uc.edu)
External Links
How To
What is Lean Manufacturing?
Lean Manufacturing techniques are used to reduce waste while increasing efficiency by using structured methods. These processes were created by Toyota Motor Corporation, Japan in the 1980s. The main goal was to produce products at lower costs while maintaining quality. Lean manufacturing focuses on eliminating unnecessary steps and activities from the production process. It is made up of five elements: continuous improvement, continuous improvement, just in-time, continuous change, and 5S. Pull systems allow customers to get exactly what they want without having to do extra work. Continuous improvement is the continuous improvement of existing processes. Just-intime refers the time components and materials arrive at the exact place where they are needed. Kaizen means continuous improvement, which is achieved by implementing small changes continuously. Last but not least, 5S is for sort. These five elements can be combined to achieve the best possible results.
Lean Production System
Six key concepts are the basis of lean production:
-
Flow: The goal is to move material and information as close as possible from customers.
-
Value stream mapping is the ability to divide a process into smaller tasks, and then create a flowchart that shows the entire process.
-
Five S’s - Sorted, In Order. Shine. Standardize. And Sustain.
-
Kanban: Use visual signals such stickers, colored tape, or any other visual cues, to keep track your inventory.
-
Theory of constraints: Identify bottlenecks and use lean tools such as kanban boards to eliminate them.
-
Just-in-time delivery - Deliver components and materials right to your point of use.
-
Continuous improvement - make incremental improvements to the process rather than overhauling it all at once.