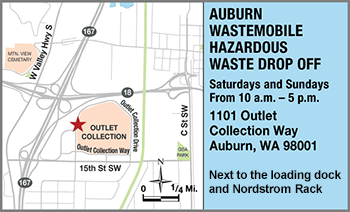
It risk or cyber risk is any type of risk that involves the use of information technology. Information technology risks include access risks and data breaches. These risks can affect both personal and business data and must be managed properly. This article will explain the various IT risks. This article will help you choose the right control measures for your company.
Information technology and risk
Information technology risk, also known as cyber risk, is any risk associated with information technology. This type risk is most prevalent in small businesses and startups. However, larger companies should consider information technology risks as well to ensure business continuity. However, there are ways to mitigate the risks of cyber attacks and protect businesses from the negative effects they can have on their bottom line.
Management of information technology risks requires a holistic, systematic approach. This includes systematic risk assessment and systemic risks management processes. It also requires decision-makers who are willing to reverse previous decisions, a well-defined communication structure, and a strong risk-taking ethic.
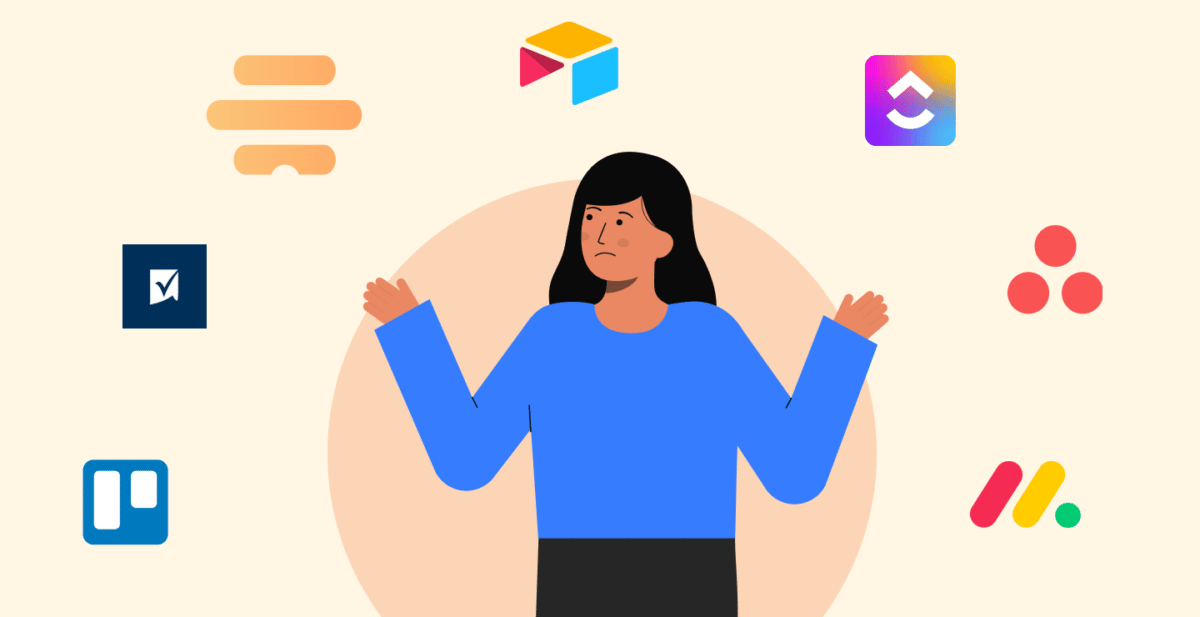
Data breach risk
A data breach is when unauthorized individuals steal, access, or modify data on a computer system. This can lead to financial loss and reputational damage as well as lawsuits. It can also cause security problems for government agencies. Breach can lead to the disclosure of highly sensitive information. An attacker could also gain access to trade secrets if they are able to hack into the IT infrastructure of the government. A third party can use the data to create fraudulent accounts or sell it on darknet.
IT risks like data breaches are something that companies need to notify customers and employees. The company must also create a response plan in order to minimize any negative consequences. The plan should be an ongoing document that is updated as necessary.
Risk assessment
IT security is concerned about access risk. This refers to unauthorised access to vital information. Access can occur from both logical or physical access. Physical access involves accessing sensitive information such as databases and processing environments. The network is used to connect users to these systems. The network may allow an employee to gain unauthorised access confidential or proprietary information.
Managing access permissions can be a complex process. Many systems and applications have different permission models, making it difficult to assign the proper permissions to each user. Organizations should have policies that restrict access to certain users in order to reduce this risk.
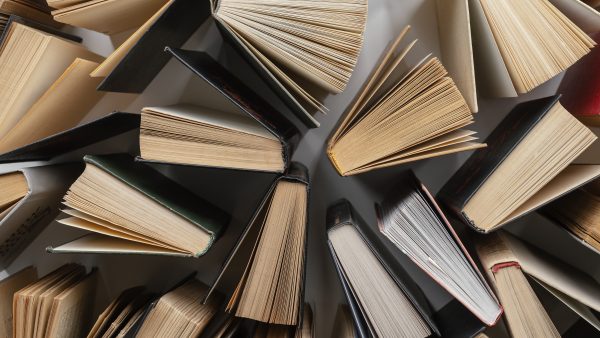
Control measures
You have a range of options to control IT risk. IT hazards can easily be controlled by providing equipment, training staff, and implementing physical security. To reduce risk, control measures must be integrated and comprehensive. You should implement administrative controls to reduce exposure. You should also use respirators and goggles as PPE. These should all work in concert and should be communicated regularly to employees.
A risk assessment is the foundation of any risk control plan. Also, it is important to determine which controls are best for your business. These measures must be cost-effective, efficient, and effective.
Preparation for reaction
Workers must be aware and prepared for any reaction. Workers in the C and D categories should not be exposed to undue risk. Workers in category C and D should be wary of risks from carcinogens. Furthermore, workers should be aware of explosion risks.
FAQ
What kind of people use Six Sigma
Six Sigma is well-known to those who have worked in operations research and statistics. However, anyone involved in any aspect of business can benefit from using it.
It is a commitment-intensive task that requires strong leadership skills.
How to manage employees effectively?
Effectively managing employees requires that you ensure their happiness and productivity.
It is important to set clear expectations about their behavior and keep track of their performance.
Managers must be clear about their goals and those of their teams in order to succeed.
They must communicate clearly with their staff. And they need to ensure that they reward good performance and discipline poor performers.
They also need to keep records of their team's activities. These include:
-
What was the result?
-
How much work did you put in?
-
Who did it?
-
What was the moment it was completed?
-
Why did it happen?
This information is useful for monitoring performance and evaluating the results.
What is the difference in leadership and management?
Leadership is about influencing others. Management is all about controlling others.
A leader inspires his followers while a manager directs the workers.
Leaders inspire people to achieve success. Managers keep their workers focused.
A leader develops people; a manager manages people.
Statistics
- The BLS says that financial services jobs like banking are expected to grow 4% by 2030, about as fast as the national average. (wgu.edu)
- Hire the top business lawyers and save up to 60% on legal fees (upcounsel.com)
- As of 2020, personal bankers or tellers make an average of $32,620 per year, according to the BLS. (wgu.edu)
- The average salary for financial advisors in 2021 is around $60,000 per year, with the top 10% of the profession making more than $111,000 per year. (wgu.edu)
- This field is expected to grow about 7% by 2028, a bit faster than the national average for job growth. (wgu.edu)
External Links
How To
How does Lean Manufacturing work?
Lean Manufacturing methods are used to reduce waste through structured processes. They were created by Toyota Motor Corporation in Japan in the 1980s. The main goal was to produce products at lower costs while maintaining quality. Lean manufacturing focuses on eliminating unnecessary steps and activities from the production process. It is composed of five fundamental elements: continuous improvement; pull systems, continuous improvements, just-in–time, kaizen, continuous change, and 5S. Pull systems allow customers to get exactly what they want without having to do extra work. Continuous improvement is the continuous improvement of existing processes. Just-in time refers to components and materials being delivered right at the place they are needed. Kaizen stands for continuous improvement. Kaizen can be described as a process of making small improvements continuously. Finally, 5S stands for sort, set in order, shine, standardize, and sustain. These five elements are used together to ensure the best possible results.
The Lean Production System
Six key concepts make up the lean manufacturing system.
-
Flow - focus on moving material and information as close to customers as possible;
-
Value stream mapping is the ability to divide a process into smaller tasks, and then create a flowchart that shows the entire process.
-
Five S's, Sort, Set in Order, Shine. Standardize. and Sustain.
-
Kanban - visual cues such as stickers or colored tape can be used to track inventory.
-
Theory of Constraints - Identify bottlenecks in the process, and eliminate them using lean tools such kanban boards.
-
Just-in time - Get components and materials delivered right at the point of usage;
-
Continuous improvement - make incremental improvements to the process rather than overhauling it all at once.