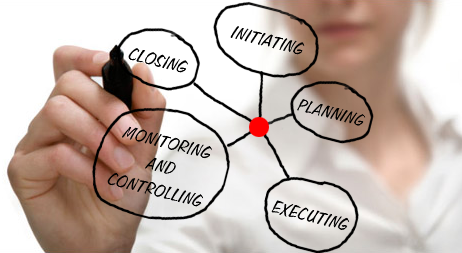
It is important for any organization to establish a management goal. The purpose of the goal is to help achieve the company's goals. A well-written objective clearly explains the company's objectives and why they should be achieved. The objective gives employees a sense of direction and purpose. When the objective of an organization is clearly understood, it can be expressed in a measurable format.
Goals
A goal is a plan for the future or a desired outcome. People strive to achieve their goals within a certain period of time, and they often set deadlines for their achievements. When they set goals, they make sure to measure their progress against those deadlines. But, there are some goals that can prove difficult.
Identifying and setting objectives is essential for the success of a company. These goals serve many different purposes, and all levels need to participate. There are two types: process-oriented and outcome-oriented goals. Outcome-oriented objectives communicate the new vision of the company and make it possible for employees to take action. Although they look similar to the outcome-oriented goals, process-oriented objectives are more focused on creating new processes or workflows. The primary difference in process-oriented goals and outcomes-oriented ones is that they don't necessarily have a specific time frame.
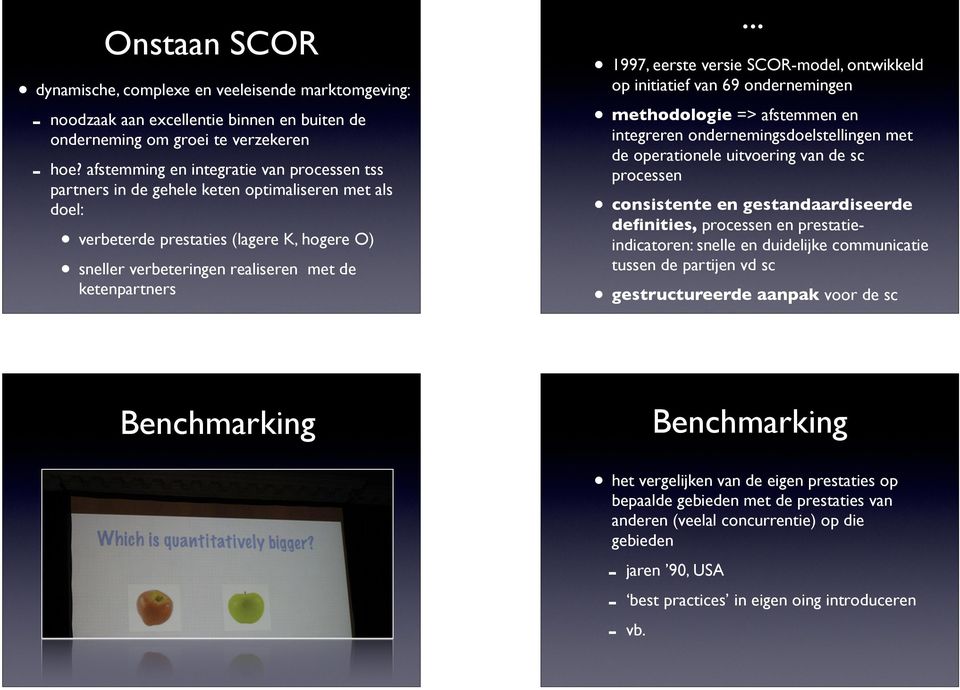
Scope
Management's purpose is to help a company grow and succeed. This can be achieved by proper planning and execution. Sound management strives to provide the best quality products and services for the lowest price. It is also important to reduce waste within a company. Proper management also ensures that the supply of goods and services to people remains regular. This helps improve a company’s financial strength.
A solid management team is focused on optimizing the use of resources. This can happen by implementing logistic strategies, reducing waste, and other such measures. This will help a company increase its profit margin. A management team will also be attentive to the needs of employees, and will develop procedures that will improve the working environment. A strong management team will put employee's personal development first and will provide opportunities for training, mentoring and internal promotions.
Measurable Form
An objective that is quantifiable can be described as a management goal. For example, a goal to improve financial performance may be measured by total sales and profitability as well as stock price. These measurements are important for strategic planning because they allow managers and analysts to evaluate whether the company is moving in the right direction.
The management objective must be specific, time-bound and specific. It must be pertinent to the organization's purpose and work towards that end. It should also be a worthwhile goal that can be measured.
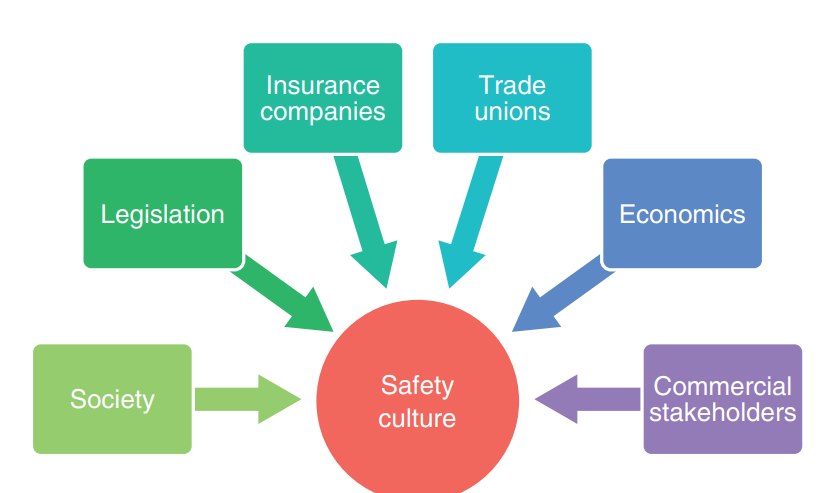
Setting objectives is a process
The process of setting management objectives is about defining the goals for an organization. These goals must be defined at the top level of management. They must also be achievable and adaptable to the changing business environment. Once the objectives are set, top management works with the people responsible for their execution. The top management then creates departmental targets, strategies and action plans.
MBOs should be based on the company's mission and vision. These should be communicated clearly from the top down and include all opinions. Employees should be encouraged to create their own objectives. This will give employees a greater sense empowerment. Additionally, it is important that objectives are measurable in order to demonstrate progress.
FAQ
What can a manager do to improve his/her management skillset?
Through demonstrating good management skills at every opportunity
Managers must monitor the performance of subordinates constantly.
You must quickly take action if your subordinate fails to perform.
It is essential to know what areas need to be improved and how to do it.
Why is it important that companies use project management methods?
Project management techniques are used to ensure that projects run smoothly and meet deadlines.
This is because many businesses depend heavily upon project work to produce products and services.
These projects must be managed efficiently and effectively by companies.
Companies could lose their time, reputation, and money without effective project management.
Which kind of people use Six Sigma
Six Sigma will most likely be familiar to people who have worked in statistics and operations research. But anyone can benefit from it.
Because it requires a high level of commitment, only those with strong leadership skills will make an effort necessary to implement it successfully.
What is Six Sigma and how can it help you?
It's an approach to quality improvement that emphasizes customer service and continuous learning. The goal is to eliminate defects by using statistical techniques.
Motorola's 1986 efforts to improve manufacturing process efficiency led to the creation of Six Sigma.
The idea spread quickly throughout the industry, and today, many organizations are using six sigma methods to improve product design, production, delivery, and customer service.
What are the steps involved in making a decision in management?
Managers are faced with complex and multifaceted decisions. It involves many factors, such as analysis and strategy, planning, execution, measurement, evaluation, feedback etc.
Management of people requires that you remember that they are just as human as you are, and can make mistakes. As such, there is always room for improvement, especially if you're willing to put forth the effort to improve yourself first.
We explain in this video how the Management decision-making process works. We discuss different types of decisions as well as why they are important and how managers can navigate them. These topics are covered in this course:
What is TQM?
The industrial revolution was when companies realized that they couldn't compete on price alone. This is what sparked the quality movement. They needed to improve quality and efficiency if they were going to remain competitive.
Management developed Total Quality Management to address the need for improvement. It focused on all aspects of an organisation's performance. It included continuous improvement and employee involvement as well as customer satisfaction.
Statistics
- Our program is 100% engineered for your success. (online.uc.edu)
- The BLS says that financial services jobs like banking are expected to grow 4% by 2030, about as fast as the national average. (wgu.edu)
- Hire the top business lawyers and save up to 60% on legal fees (upcounsel.com)
- The average salary for financial advisors in 2021 is around $60,000 per year, with the top 10% of the profession making more than $111,000 per year. (wgu.edu)
- As of 2020, personal bankers or tellers make an average of $32,620 per year, according to the BLS. (wgu.edu)
External Links
How To
What is Lean Manufacturing?
Lean Manufacturing methods are used to reduce waste through structured processes. They were developed by Toyota Motor Corporation in Japan during the 1980s. The aim was to produce better quality products at lower costs. Lean manufacturing emphasizes removing unnecessary steps from the production process. It includes five main elements: pull systems (continuous improvement), continuous improvement (just-in-time), kaizen (5S), and continuous change (continuous changes). Pull systems allow customers to get exactly what they want without having to do extra work. Continuous improvement means continuously improving on existing processes. Just-in-time is when components and other materials are delivered at their destination in a timely manner. Kaizen stands for continuous improvement. Kaizen can be described as a process of making small improvements continuously. The 5S acronym stands for sort in order, shine standardize and maintain. These five elements are combined to give you the best possible results.
Lean Production System
Six key concepts underlie the lean production system.
-
Flow - The focus is on moving information and material as close as possible to customers.
-
Value stream mapping is the ability to divide a process into smaller tasks, and then create a flowchart that shows the entire process.
-
Five S's – Sort, Put In Order Shine, Standardize and Sustain
-
Kanban – visual signals like colored tape, stickers or other visual cues are used to keep track inventory.
-
Theory of Constraints - Identify bottlenecks in the process, and eliminate them using lean tools such kanban boards.
-
Just-in Time - Send components and material directly to the point-of-use;
-
Continuous improvement: Make incremental improvements to the process instead of overhauling it completely.