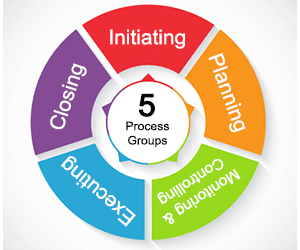
In order to survive the inevitable changes in our world, it is important to be able identify and implement ways of managing risk. Organizations will be more resilient if they adopt a systems-based approach for managing risk. But how do you decide which methods are the best?
With the proper resources, risk management methods should be implemented. You can use either internal or external resources. The resources must be accessible at all times, and the funds must be appropriately allocated. Risk is minimized when resources are readily available. Risiko increases if resources don't exist.
Sharing resources, avoiding or transferring risks are some of the options for managing risk. These methods can be either structural or non-structural. The right strategy can help you spread risk and minimize losses. The right approach may not always be possible. However, in modern times, everyone is at risk.
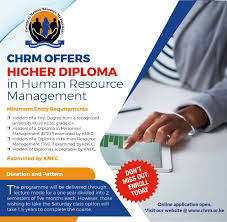
A risk chart helps you visualize potential risks and their consequences. It shows the risks to resources and their consequences, along with the options to mitigate or eliminate them.
Another way to visualize danger is by using a bow tie diagram. It is used frequently in financial and banking industries. It helps you to determine the risk level and its potential impact on your business. It can also help identify the differences in risk between two different risks. It's particularly useful when estimating the likelihood of an unexpected equipment breakdown.
The law of large quantities can be used to determine the likelyhood of an event. But fat-tailed distributions may render it useless. Some risks may not be suitable for the law of large quantities. For instance, fires in one place could result in the destruction of all department records. The risk of a flame in a single place may be lower than the risk of fire in multiple buildings.
Another way to gauge the severity of loss is to calculate the magnitude of the risk. This involves first calculating a loss's probability and then assessing the risk left after mitigation measures are taken. If a loss is likely to occur regularly, you should avoid performing activities that have a high severity of loss. This is also called risk reduction.
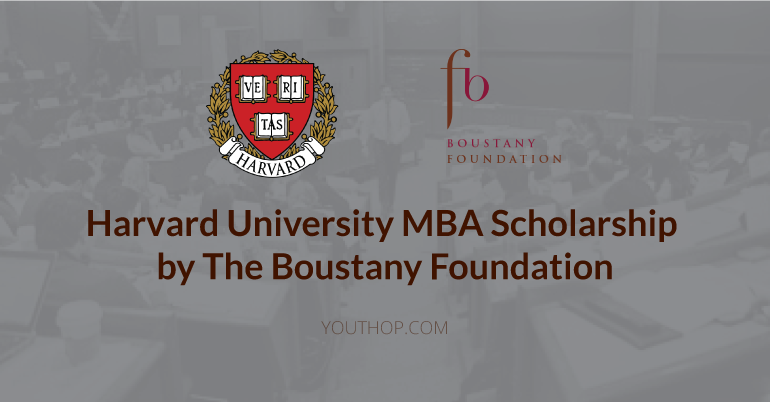
Your company will make the best decision possible by choosing the right risk management methods. The best strategy for managing risk should be specific to your company and be implemented within the context in which it is being used. It is important to determine the most appropriate methods for managing risk in your organization. This will help you reduce risk and keep your business growing.
Management of risk is more complex than it seems. Implementing systems, aligning them, and adapting your organization's ability to respond to changes are the best ways to manage risk. Your organization should also empower your people to identify threats and opportunities. Your organization should enable these people to communicate with you the threats and opportunities in a timely manner.
FAQ
What is TQM, exactly?
The industrial revolution led to the birth and growth of the quality movement. Manufacturing companies realized they couldn't compete solely on price. They had to improve efficiency and quality if they were to remain competitive.
To address this need for improvement management created Total Quality Management (TQM) which aimed to improve all aspects of an organization's performance. It included continual improvement processes, employee involvement, customer satisfaction, and customer satisfaction.
What are management concepts?
Management concepts are the fundamental principles and practices that managers use when managing people and their resources. They cover topics like job descriptions (job descriptions), performance evaluations, training programmes, employee motivation and compensation systems.
What is a basic management tool used in decision-making?
A decision matrix is a simple but powerful tool for helping managers make decisions. It allows them to consider all possible solutions.
A decision matrix represents alternatives in rows and columns. This makes it easy for you to see how each option affects other options.
In this example, there are four possible options represented by boxes on the left-hand side of the matrix. Each box represents one option. The top row represents the current state of affairs, and the bottom row is indicative of what would happen in the event that nothing were done.
The effect of selecting Option 1 is shown in the middle column. It would increase sales by $2 million to 3 million in this instance.
The effects of options 2 and 3 are shown in the next columns. These are good changes, they increase sales by $1million or $500,000. These positive changes have their downsides. Option 2 can increase costs by $100 million, while Option 3 can reduce profits by $200,000.
The last column shows you the results of Option 4. This means that sales will decrease by $1 million.
The best part of using a decision-matrix is that it doesn't require you to know which numbers belong where. The best thing about a decision matrix is that you can simply look at the cells, and immediately know whether one option is better or not.
The matrix already does all the work. It is as simple as comparing the numbers within the relevant cells.
Here's an example of how you might use a decision matrix in your business.
You need to decide whether to invest in advertising. By doing so, you can increase your revenue by $5 000 per month. However, this will mean that you'll have additional expenses of $10,000.
You can calculate the net result of investing in advertising by looking at the cell directly below the one that says "Advertising." That number is $15 thousand. Advertising is more valuable than its costs.
What is Six Sigma, exactly?
It's an approach to quality improvement that emphasizes customer service and continuous learning. The objective is to eliminate all defects through statistical methods.
Motorola created Six Sigma as part of their efforts to improve manufacturing processes in 1986.
The idea quickly spread in the industry. Many organizations today use six-sigma methods to improve product design and production, delivery and customer service.
What is the meaning of "project management?"
It refers to the management of activities related to a project.
This includes defining the scope, identifying the requirements and preparing the budget. We also organize the project team, schedule the work, monitor progress, evaluate results, and close the project.
How do you effectively manage employees?
Managing employees effectively means ensuring that they are happy and productive.
It also means having clear expectations of their behavior and keeping track of their performance.
Managers must set clear goals for their employees and themselves to achieve this goal.
They must communicate clearly with their staff. They should also ensure that they both reward high performers and discipline those who are not performing to their standards.
They must also keep records of team activities. These include:
-
What did you accomplish?
-
How much work was put in?
-
Who did it?
-
What was the moment it was completed?
-
Why?
This data can be used to evaluate and monitor performance.
Statistics
- 100% of the courses are offered online, and no campus visits are required — a big time-saver for you. (online.uc.edu)
- Hire the top business lawyers and save up to 60% on legal fees (upcounsel.com)
- UpCounsel accepts only the top 5 percent of lawyers on its site. (upcounsel.com)
- As of 2020, personal bankers or tellers make an average of $32,620 per year, according to the BLS. (wgu.edu)
- The profession is expected to grow 7% by 2028, a bit faster than the national average. (wgu.edu)
External Links
How To
How do you apply the Kaizen method to your life?
Kaizen means continuous improvement. The term was coined in the 1950s at Toyota Motor Corporation and refers to the Japanese philosophy emphasizing constant improvement through small incremental changes. It is a process where people come together to improve their processes.
Kaizen is one of the most effective methods used in Lean Manufacturing. In this concept, employees who are responsible for the production line must identify problems that exist during the manufacturing process and try to solve them before they become big issues. This is how you can improve the quality and lower the cost.
Kaizen is the idea that every worker should be aware of what is going on around them. So that there is no problem, you should immediately correct it if something goes wrong. So, if someone notices a problem while working, he/she should report it to his/her manager.
Kaizen has a set of basic principles that we all follow. When working with kaizen, we always start with the end result and move towards the beginning. For example, if we want to improve our factory, we first fix the machines that produce the final product. Then, we fix the machines that produce components and then the ones that produce raw materials. Then, we fix those who work directly with the machines.
This method, called 'kaizen', focuses on improving each and every step of the process. We finish fixing the factory and then go back to the beginning. This continues until we achieve perfection.
You need to know how to measure the effectiveness of kaizen within your business. There are many methods to assess if kaizen works well. Another way to determine if kaizen is working well is to look at the quality of the products. Another way is to check how much productivity has grown since kaizen was implemented.
To determine if kaizen is effective, you should ask yourself why you chose to implement kaizen. Is it because the law required it or because you want to save money. Did you really believe it would lead to success?
Suppose you answered yes to any of these questions, congratulations! Now you're ready for kaizen.