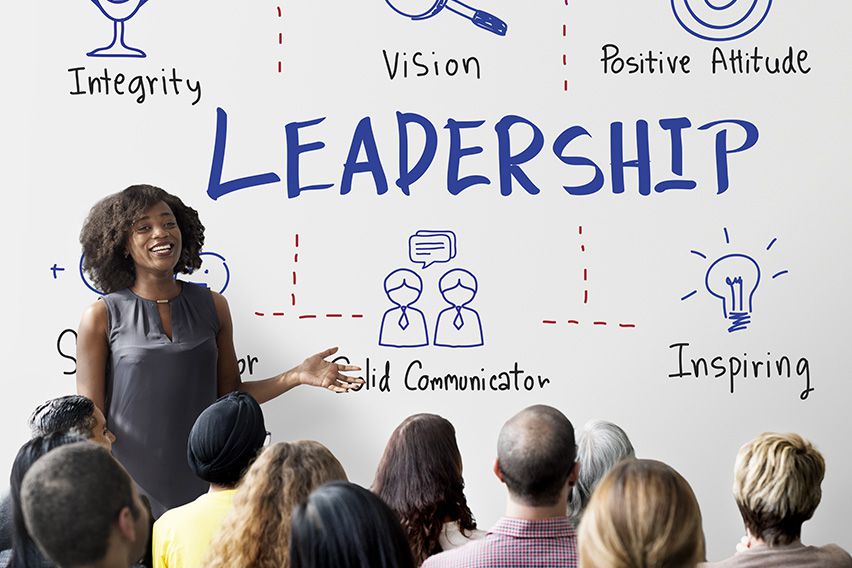
A company must follow 14 elements in order be considered as a PSM program. These elements include Process Hazard analyses, Permissible Exposure Limits, Physical Data, and Corrosivity Data. These elements are crucial to the success of a PSM Program. Compliant PSM programs will be judged compliant if they adhere to these elements. These elements should be followed by your company.
Analyses of Process Hazards
An essential element of any safety management program is the process hazard analysis. It helps to identify possible hazards and determine the consequences of failure. This analysis must be done by a team of employees who are knowledgeable about the process. It will include human factors and previous incidents and reviews the siting of the facility. Once completed, the analysis must be updated every five years. As part of a safety management program, the process of hazard analysis must also be implemented.
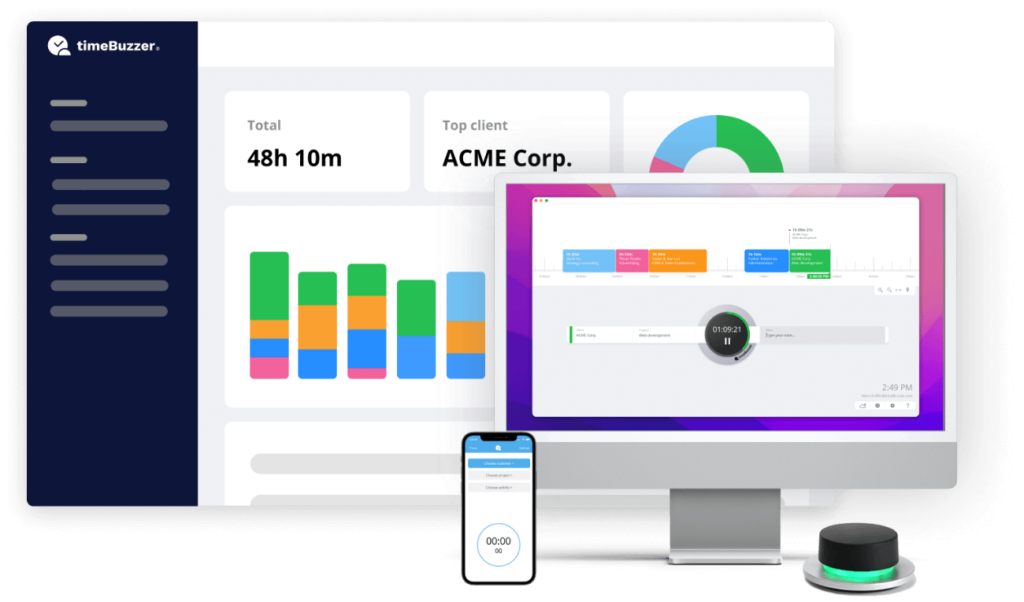
Permissible exposure limits
OSHA Process Safety Management is a set standard for hazardous chemical, gas, or liquid processes. The standard is applicable to businesses who produce or process dangerous chemicals. It does not cover hydrocarbon fuels used exclusively for workplace use, retail or well drilling. It does not apply to facilities that are normally vacant or remote.
Physical data
PSM is the process that analyzes and controls the risk associated with hazardous materials and products. This involves knowing how to safely transport, store, and handle hazardous substances. This will result in less product waste and fewer workplace injuries. It makes it easier to make decisions and allows organizations to prioritize safety and health. PSM is essential for a safe workplace. It can help companies prevent costly medical emergencies and save money.
Data on corrosivity
The PSM standard defines requirements for handling and storing chemicals and other substances that may cause damage to buildings and equipment. The PSM includes requirements for emergency actions plans and permit systems. It also requires periodic compliance audits. PSM-compliant workplaces will provide safety and protection for employees, no matter how hazardous your organization's production processes are.
Thermal stability data
OSHA established a standard to collect and report PSM thermal stability data. The program will ensure that researchers are aware of possible hazards and minimize the effects of accidental release. It will be regularly reviewed and updated to meet the needs of new research projects. It will become accessible to all employees. The PSM program includes information on toxicity, reactivity, corrosivity, and physical properties.
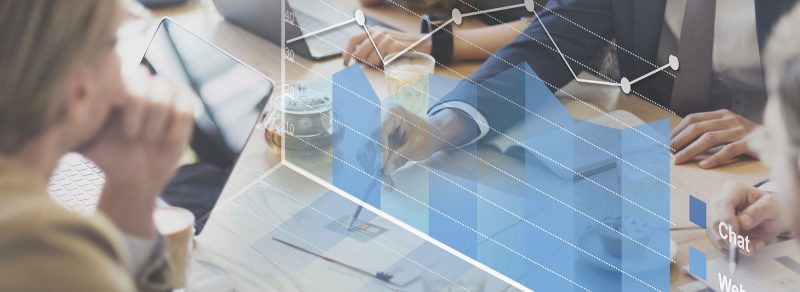
Participation clause for employees
Process Safety Management (PSM), a systematic approach to the prevention and control of hazardous chemicals (HHC)-related process accidents, is an analytical approach. It is a crucial step in improving safety at work and must be applied at all levels of the plant. It contains 14 elements and employee participation clauses that must all be implemented. Listed below are a few examples of these elements and their requirements.
FAQ
What are the steps of the management decision-making process?
Managers are faced with complex and multifaceted decisions. This involves many factors including analysis, strategy and planning, implementation, measurement and evaluation, feedback, feedback, and others.
Management of people requires that you remember that they are just as human as you are, and can make mistakes. As such, there are always opportunities for improvement, especially when you put in the effort to improve yourself.
We explain in this video how the Management decision-making process works. We discuss different types of decisions as well as why they are important and how managers can navigate them. The following topics will be covered.
What is the difference of leadership and management?
Leadership is about being a leader. Management is about controlling others.
A leader inspires others while a manager directs them.
A leader motivates people to achieve success; a manager keeps workers on task.
A leader develops people; a manager manages people.
What are some of the common mistakes made by managers?
Managers can make their jobs more difficult than necessary.
They may not be able to delegate enough responsibility to staff or provide adequate support.
Additionally, many managers lack communication skills that are necessary to motivate and direct their teams.
Managers can set unrealistic expectations for their employees.
Managers may attempt to solve all problems themselves, rather than delegating it to others.
What does it mean to say "project management"
Management is the act of managing activities in order to complete a project.
We help you define the scope of your project, identify the requirements, prepare the budget, organize the team, plan the work, monitor progress and evaluate the results before closing down the project.
What kind of people use Six Sigma?
Six sigma is a common concept for people who have worked in statistics or operations research. Anyone involved in business can benefit.
Because it requires a high level of commitment, only those with strong leadership skills will make an effort necessary to implement it successfully.
What is Six Sigma?
It is a way to improve quality that places emphasis on customer service and continuous learning. It is a method that eliminates defects using statistical techniques.
Six Sigma was developed at Motorola in 1986 as part of its efforts to improve manufacturing processes.
It was quickly adopted by the industry and many companies are now using six-sigma to improve product design, production, delivery, customer service, and product design.
What is a basic management tool used in decision-making?
A decision matrix is a simple but powerful tool for helping managers make decisions. It helps them think systematically about all the options available to them.
A decision matrix allows you to represent alternatives as columns and rows. This makes it easy for you to see how each option affects other options.
In this example, we have four possible alternatives represented by the boxes on the left side of the matrix. Each box represents an option. The top row displays the current situation, and the bottom row shows what might happen if nothing is done.
The effect of selecting Option 1 is shown in the middle column. It would increase sales by $2 million to 3 million in this instance.
The results of choosing Option 2 and 3 can be seen in the columns below. These are both positive changes that increase sales by $1million and $500,000. However, these also involve negative consequences. Option 2 can increase costs by $100 million, while Option 3 can reduce profits by $200,000.
The final column shows the results for Option 4. This results in a decrease of sales by $1,000,000
The best part about using a decision matrix to guide you is that you don’t need to keep track of which numbers go where. You can just glance at the cells and see immediately if one given choice is better.
This is because your matrix has already done the hard work. It is as simple as comparing the numbers within the relevant cells.
Here's an example showing how you might use a Decision Matrix in your business.
You need to decide whether to invest in advertising. You'll be able increase your monthly revenue by $5000 if you do. You will still have to pay $10000 per month in additional expenses.
If you look at the cell that says "Advertising", you can see the number $15,000. Therefore, you should choose to invest in advertising since it is worth more than the cost involved.
Statistics
- Hire the top business lawyers and save up to 60% on legal fees (upcounsel.com)
- UpCounsel accepts only the top 5 percent of lawyers on its site. (upcounsel.com)
- The average salary for financial advisors in 2021 is around $60,000 per year, with the top 10% of the profession making more than $111,000 per year. (wgu.edu)
- 100% of the courses are offered online, and no campus visits are required — a big time-saver for you. (online.uc.edu)
- The profession is expected to grow 7% by 2028, a bit faster than the national average. (wgu.edu)
External Links
How To
How do I get my Six Sigma license?
Six Sigma can be used to improve quality and efficiency. It's a system that allows companies to get consistent results from operations. The name derives its meaning from the "sigmas" Greek word, which is composed of two letters that mean six. This process was developed at Motorola in 1986. Motorola recognized the need to standardize manufacturing processes in order to produce better products at a lower cost. There were many people doing the work and they had difficulty achieving consistency. They used statistical tools such as Pareto analysis, control charts, and Pareto analysis to resolve the problem. After this, they would apply these techniques to every part of the operation. So, after applying this technique, they would be able to make changes where there was room for improvement. Three main steps are involved when you're trying to go through the whole process of getting your Six Sigma certification. First, you need to determine if your qualifications are valid. You will need classes to pass before you can begin taking tests. You can then start taking the tests once you have completed those classes. The class material will be reviewed. After that, you can take the test. If you pass, then you will become certified. Finally, you can add your certifications on to your resume.