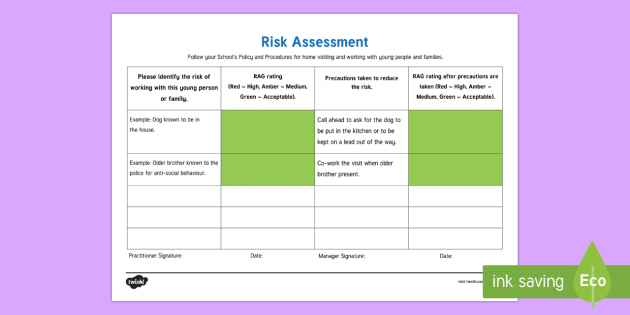
Process knowledge management is an essential tool in quality and risk management. It provides a framework for linking past knowledge to current knowledge, including prior product data from similar products. It provides the foundation for continuous improvement. Let's examine some of the advantages of process knowledge management. Here are some examples. It may surprise you at the value it can bring to your company. It's also easy to put into practice.
Lessons learned
Ideally, your organisation will have a template for lessons learned and make this readily available to all employees. If not, it is better to use a document management system to share the lessons with your team. The template should be simple and easily understandable by your team, but you should also consider testing different formats. The more complex your document is, the less likely it will be shared by your employees. This is why it is so important to choose the right format and make sure your staff is involved.
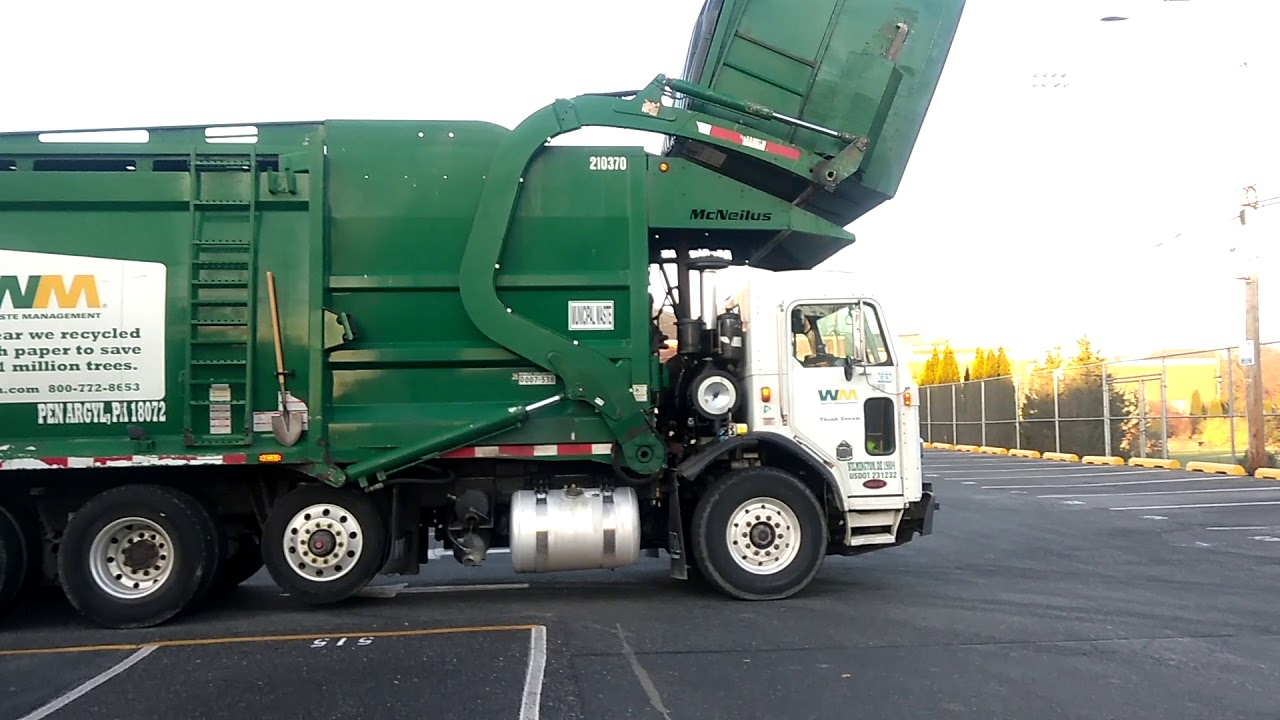
Expertise location
Expert location is much more than just biographical details. It includes tools for sharing expertise and identifying key employees who could be the best candidates to answer questions. For example, most people have a profile on LinkedIn, Facebook, or Google+ that includes their areas of expertise. These tools make it easy to organize information, giving people places to talk about their publications, projects and knowledge. This can help to improve their image and reputation.
Communities & networks
The creation of virtual communities can facilitate cross-industry collaborations as well as strategic knowledge management. These communities are a way to foster communication and disseminate new processes, approaches, and tools that improve the performance and innovation of organisations. They can be used to improve the effectiveness of meetings and share case histories. Industry leaders are looking into the potential benefits of communities in industrial production. See Communities & Networks for Process Knowledge Management: These are a framework to help you manage your knowledge. Communities and networks can be used to connect people from many different locations or disciplines.
Content management
Although a content management system can store 200 pages worth of training documents, it cannot replace a knowledge-management system that can capture institutional as well as user-generated information about a particular topic. A content-management system should allow for information to be captured from many perspectives. This will help in making better decisions and serving customers. A content-management system could store all the sales training materials for a dealership, for example, if they are selling cars.
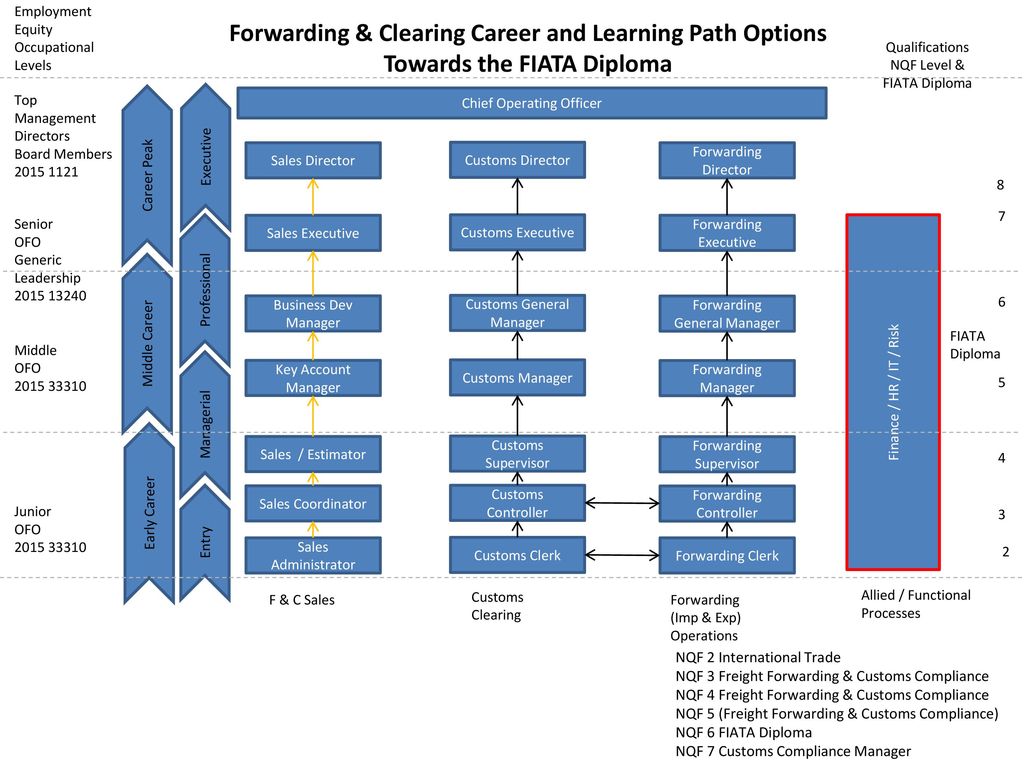
Knowledge mapping
Knowledge mapping is a great way to leverage your knowledge assets and improve your processes. Knowledge mapping is a powerful way to identify knowledge gaps and find solutions for improving your process. It is also a useful tool to increase collaboration among departments. Once you have mapped your knowledge, it is possible to start standardizing processes. Knowledge maps are a great way to capture and disseminate best practices and improve your organization's processes and operations.
FAQ
What are some common management mistakes?
Sometimes, managers make their job more difficult than it is.
They might not give enough support and delegate the right responsibilities to their staff.
A majority of managers lack the communication skills needed to motivate their team and lead them.
Some managers create unrealistic expectations for their teams.
Managers may attempt to solve all problems themselves, rather than delegating it to others.
What are the 4 main functions of management?
Management is responsible in planning, organizing and directing people and resources. Management also involves setting goals and developing policies.
Management is the ability to direct, coordinate, control, motivate, supervise, train, and evaluate an organization's efforts towards achieving its goals.
Management has four primary functions:
Planning - Planning is about determining what must be done.
Organizing - Organization involves deciding what should be done.
Direction - This is the art of getting people to follow your instructions.
Controlling - Controlling means ensuring that people carry out tasks according to plan.
Why is it important for companies to use project management techniques?
Project management techniques are used to ensure that projects run smoothly and meet deadlines.
This is due to the fact that most businesses rely heavily upon project work in order to produce goods, and services.
These projects are essential for companies.
Companies may lose their reputation, time and money if they do not have effective project management.
What are the top management skills?
Management skills are essential for any business owner, whether they're running a small local store or an international corporation. These include the ability and willingness to manage people, finances as well resources, time and space.
Management Skills are also needed when you're setting goals and objectives, planning strategies, leading teams, motivating employees, resolving problems, creating policies and procedures, and managing change.
There are so many managerial tasks!
How do you define Six Sigma?
People who have worked with statistics and operations research will usually be familiar with the concepts behind six sigma. It can be used by anyone in any business aspect.
It is a commitment-intensive task that requires strong leadership skills.
What are the 5 management processes?
The five stages of a business include planning, execution (monitoring), review, evaluation, and review.
Setting goals for the future is part of planning. This includes setting goals for the future and defining what you want.
Execution takes place when you actually implement the plans. It is important to ensure that everyone follows the plans.
Monitoring allows you to monitor your progress towards achieving your goals. This should involve regular reviews of performance against targets and budgets.
Reviews take place at the end of each year. These reviews allow you to evaluate whether the year was successful. If not, changes may be made to improve the performance next time around.
After the annual review is complete, evaluations are conducted. It helps identify which aspects worked well and which didn't. It also gives feedback on how well people did.
What are the steps that management takes to reach a decision?
The decision-making process for managers is complex and multifaceted. It involves many elements, including analysis, strategy. planning. implementation. measurement. evaluation. feedback.
When managing people, the most important thing to remember is that they are just human beings like you and make mistakes. There is always room to improve, especially if your first priority is to yourself.
In this video, we explain what the decision-making process looks like in Management. We discuss the different types of decisions and why they are important, every manager should know how to navigate them. The following topics will be covered:
Statistics
- Our program is 100% engineered for your success. (online.uc.edu)
- This field is expected to grow about 7% by 2028, a bit faster than the national average for job growth. (wgu.edu)
- 100% of the courses are offered online, and no campus visits are required — a big time-saver for you. (online.uc.edu)
- Your choice in Step 5 may very likely be the same or similar to the alternative you placed at the top of your list at the end of Step 4. (umassd.edu)
- UpCounsel accepts only the top 5 percent of lawyers on its site. (upcounsel.com)
External Links
How To
How is Lean Manufacturing done?
Lean Manufacturing processes are used to reduce waste and improve efficiency through structured methods. They were created by Toyota Motor Corporation in Japan in the 1980s. The aim was to produce better quality products at lower costs. Lean manufacturing is about eliminating redundant steps and activities from the manufacturing process. It has five components: continuous improvement and pull systems; just-in time; continuous change; and kaizen (continuous innovation). The production of only what the customer needs without extra work is called pull systems. Continuous improvement is constantly improving upon existing processes. Just-intime refers the time components and materials arrive at the exact place where they are needed. Kaizen means continuous improvement. Kaizen involves making small changes and improving continuously. Last but not least, 5S is for sort. These five elements are used together to ensure the best possible results.
Lean Production System
Six key concepts underlie the lean production system.
-
Flow: The goal is to move material and information as close as possible from customers.
-
Value stream mapping is the ability to divide a process into smaller tasks, and then create a flowchart that shows the entire process.
-
Five S’s - Sorted, In Order. Shine. Standardize. And Sustain.
-
Kanban – visual signals like colored tape, stickers or other visual cues are used to keep track inventory.
-
Theory of Constraints - Identify bottlenecks in the process, and eliminate them using lean tools such kanban boards.
-
Just-intime - Order components and materials at your location right on the spot.
-
Continuous improvement: Make incremental improvements to the process instead of overhauling it completely.