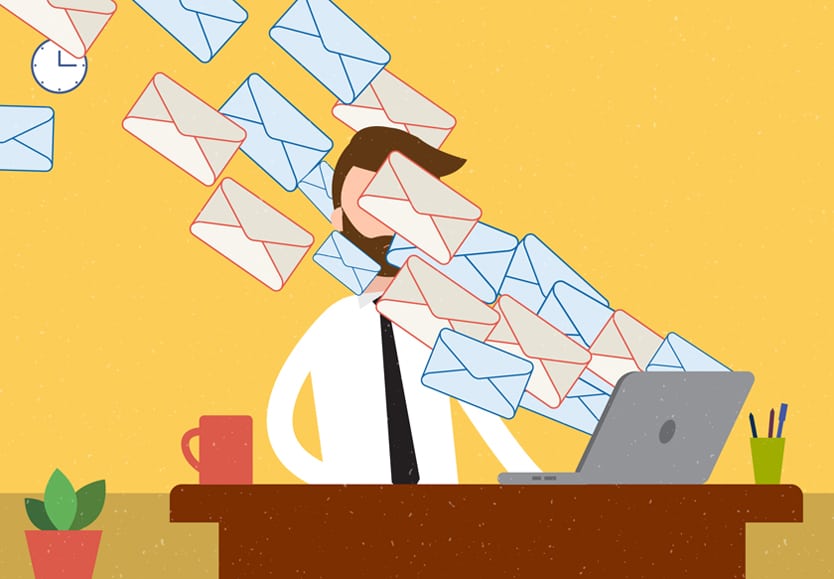
These are some common ways you can reduce your carbon footprint or lower the emissions of your supply chains. These include: Engaging stakeholders. Managing sustainable procuration. And addressing social responsibility. If you follow these tips, your supply chain will be more reliable and durable.
Stakeholder Engagement
Successful engagement with stakeholders is vital to the success of any company's sustainability efforts. In fact, engaging stakeholders can speed up the sustainability journey. Companies can build a collaborative culture with multiple stakeholders and create strong engagement strategies. In addition to improving the supply chain, engaging stakeholders helps a company gain valuable insights on risks and opportunities.
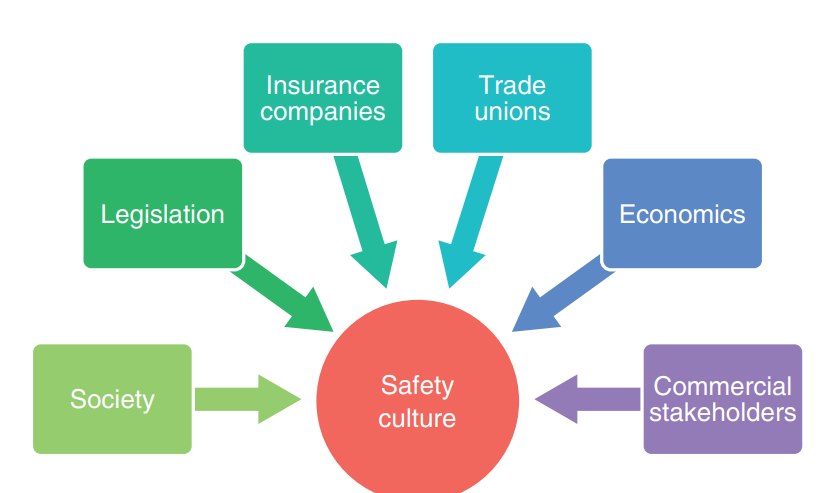
In order to engage stakeholders in a sustainable supply chain, companies should carefully select the metrics they are interested in tracking. A business' social and environmental dimensions must be considered when selecting metrics. Companies can have a difficult time measuring environmental and social metrics. Engagement can be difficult because many stakeholders might not know about the company's sustainability efforts.
Managing sustainable procurement
Managing sustainable procurement is an important process for any company. It is important to ensure that all supply chains are transparent and that suppliers at tier 1 are held responsible for sustainable practices. Some organizations struggle to implement sustainable practices due to a lack of visibility into their supply chain. EcoVadis recently found that only half of organizations had full visibility into their supply chain, while 28% didn't have any visibility at all. Implementing sustainability measures can take many years. However, organizations can start with small wins like auditing suppliers.
Making sustainable procurement a standard part the procurement process can help procurement teams minimize risks, identify incremental improvement opportunities, and ensure internal customers are informed about the impact of their purchases. To achieve sustainability, organizations need to go beyond the existing options and develop and implement new ways of sustainable procurement. They must also work in new ways with suppliers, learn new skills, and ensure that they have the right data and information to achieve their goals.
Social Responsibility Management
A sustainable supply chain must include social responsibility management (CSR). CSR principles must be followed at every step of the supply chain. The environment must not be harmed by products and services provided by companies. This includes assessing product lifespan phases, developing reuse strategies, and developing transportation abilities. Companies should also be mindful of customers' needs and comply with government regulations.
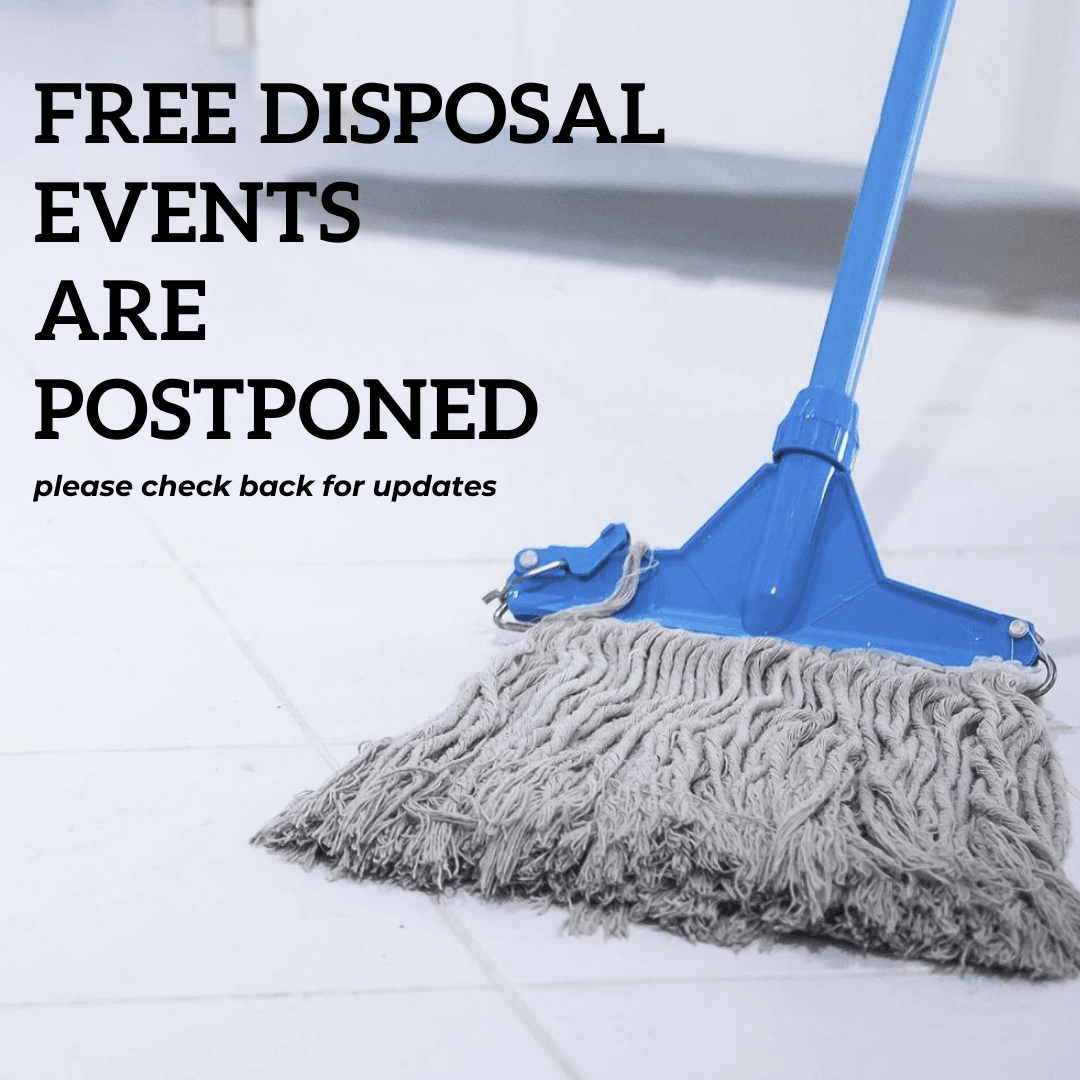
While sustainability is about meeting current needs without compromising future ones, it also involves social, economic, and environmental issues. Social responsibility is a commitment of a business to conduct business ethically, to benefit its workforce, local community, society, and the wider world.
FAQ
What is a basic management tool that can be used for decision-making?
A decision matrix can be a simple, but effective tool to assist managers in making decisions. It helps them to think strategically about all options.
A decision matrix allows you to represent alternatives as columns and rows. This allows you to easily see how each choice affects others.
In this example, we have four possible alternatives represented by the boxes on the left side of the matrix. Each box represents an option. The status quo (the current condition) is shown in the top row, and what would happen if there was no change?
The effect of Option 1 can be seen in the middle column. In this example, it would lead to an increase in sales of between $2 million and $3 million.
The effects of options 2 and 3 are shown in the next columns. These positive changes result in increased sales of $1 million and $500,000. But, they also have some negative consequences. Option 2 increases costs by $100 thousand, while Option 3 decreases profits to $200 thousand.
The last column displays the results of selecting Option 4. This involves decreasing sales by $1 million.
A decision matrix has the advantage that you don’t have to remember where numbers belong. You can just glance at the cells and see immediately if one given choice is better.
This is because your matrix has already done the hard work. It is as simple a matter of comparing all the numbers in each cell.
Here is an example how you might use the decision matrix in your company.
You need to decide whether to invest in advertising. If you do this, you will be able to increase revenue by $5000 per month. However, additional expenses of $10 000 per month will be incurred.
If you look at the cell that says "Advertising", you can see the number $15,000. Advertising is more valuable than its costs.
What is Six Sigma?
It's a strategy for quality improvement that emphasizes customer care and continuous learning. The goal is to eliminate defects by using statistical techniques.
Motorola created Six Sigma as part of their efforts to improve manufacturing processes in 1986.
It was quickly adopted by the industry and many companies are now using six-sigma to improve product design, production, delivery, customer service, and product design.
How can we create a culture of success in our company?
A company culture that values and respects its employees is a successful one.
It's founded on three principal principles:
-
Everybody has something of value to share
-
People are treated fairly
-
Respect is shared between individuals and groups
These values can be seen in the behavior of people. They will treat others with kindness and consideration.
They will respect the opinions of others.
They can also be a source of inspiration for others.
A company culture encourages collaboration and communication.
People feel comfortable expressing their opinions freely without fear of reprisal.
They know that they will not be judged if they make mistakes, as long as the matter is dealt with honestly.
Finally, the company culture encourages honesty as well as integrity.
Everyone knows that they must always tell the truth.
Everyone knows that there are rules and regulations that apply to them.
No one is entitled to any special treatment or favors.
What is the difference between Six Sigma Six Sigma and TQM?
The major difference between the two tools for quality management is that six Sigma focuses on eliminating defect while total quality control (TQM), on improving processes and decreasing costs.
Six Sigma is a methodology for continuous improvement. This method emphasizes eliminating defects using statistical methods such p-charts, control charts, and Pareto analysis.
The goal of this method is to reduce variation in product output. This is done by identifying root causes and rectifying them.
Total Quality Management involves monitoring and measuring every aspect of the organization. Training employees is also part of total quality management.
It is frequently used as an approach to increasing productivity.
Why is it so hard to make smart business decisions?
Complex systems with many moving parts are the hallmark of businesses. It is difficult for people in charge of businesses to manage multiple priorities simultaneously and also deal with uncertainty.
Understanding the impact of these factors on the system is crucial to making sound decisions.
This requires you to think about the purpose and function of each component. It's important to also consider how they interact with each other.
You need to ask yourself if your previous actions have led you to make unfounded assumptions. You might consider revisiting them if they are not.
For help, ask someone else if you're still stumped after all the above. They might see things differently than you and may have some insights that could help find a solution.
What is Kaizen?
Kaizen is a Japanese term meaning "continuous improvement." It is a philosophy that encourages employees to constantly look for ways to improve their work environment.
Kaizen is built on the belief that everyone should be able do their jobs well.
Statistics
- Hire the top business lawyers and save up to 60% on legal fees (upcounsel.com)
- The average salary for financial advisors in 2021 is around $60,000 per year, with the top 10% of the profession making more than $111,000 per year. (wgu.edu)
- Your choice in Step 5 may very likely be the same or similar to the alternative you placed at the top of your list at the end of Step 4. (umassd.edu)
- Our program is 100% engineered for your success. (online.uc.edu)
- The profession is expected to grow 7% by 2028, a bit faster than the national average. (wgu.edu)
External Links
How To
How do you implement a Quality Management Plan (QMP)?
Quality Management Plan (QMP), which was introduced in ISO 9001:2008, provides a systematic approach to improving processes, products, and services through continual improvement. It helps to improve customer satisfaction and product/service quality by continuously measuring, analyzing, controlling and improving.
QMP is a method that ensures good business performance. The QMP aims to improve the process of production, service delivery, and customer relationship. A QMP should include all three aspects - Processes, Products, and Services. When the QMP includes only one aspect, it is called a "Process" QMP. If the QMP is focused on a product/service, it's called a QMP. And when the QMP concentrates on Customer Relationships, it is called "Customer" QMP.
Scope is the most important element in implementing a QMP. Strategy is the second. They can be described as follows:
Scope: This describes the scope and duration for the QMP. For example, if you want to implement a QMP that lasts six months, then this scope will outline the activities done during the first six.
Strategy: This describes the steps taken to achieve the goals set out in the scope.
A typical QMP consists of 5 phases: Planning, Design, Development, Implementation, and Maintenance. Here are the details for each phase.
Planning: This stage is where the QMP objectives are identified and prioritized. To get to know the expectations and requirements, all stakeholders are consulted. Next, you will need to identify the objectives and priorities. The strategy for achieving them is developed.
Design: The design stage involves the development of vision, mission strategies, tactics, and strategies that will allow for successful implementation. These strategies are then put into practice by creating detailed plans.
Development: Here the development team works toward building the necessary resources and capabilities to support the successful implementation.
Implementation: This refers to the actual implementation or the use of the strategies planned.
Maintenance: Maintaining the QMP over time is an ongoing effort.
In addition, several additional items must be included in the QMP:
Participation by Stakeholders is essential for the QMP's continued success. They need to be actively involved in the planning, design, development, implementation, and maintenance stages of the QMP.
Project Initiation: It is essential to have a clear understanding about the problem and the solution before you can initiate a project. Also, the initiator should understand why they are doing it and what they expect.
Time Frame: It is important to consider the QMP's time frame. You can use a simplified version if you are only going to be using the QMP for short periods. For a long-term commitment you may need more complicated versions.
Cost Estimation. Cost estimation is another crucial component of QMP. Planning is not possible without knowing the amount of money you will spend. Cost estimation is crucial before you begin the QMP.
QMPs are more than just documents. They can also be updated as needed. It is constantly changing as the company changes. It is important to review it periodically to ensure it meets all current requirements.