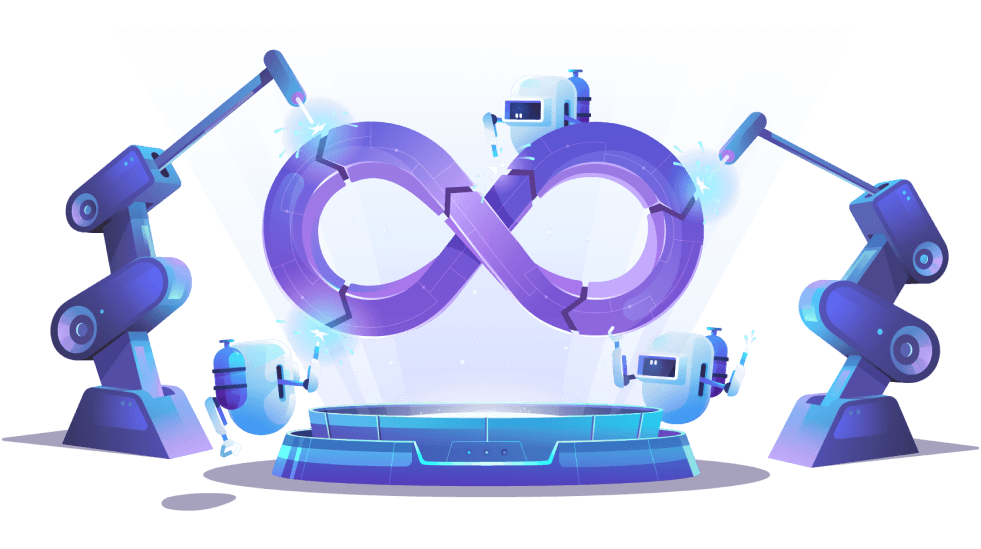
A Master of Public Administration (MPA) is a program that offers a graduate degree in nonprofit and public management. This course is designed to teach you the leadership skills necessary for leading a non-profit organization. It teaches students how to inspire volunteers and employees, as well as the surrounding community. The Network of Schools of Public Policy, Affairs, and Administration accredited the program. Oklahoma currently has two MPA programs, with more than 208 worldwide.
Schools that offer programs in nonprofit and public management
A Master's in Public and Nonprofit Management will prepare you for a wide range of roles in nonprofit organizations. This program has many benefits. It prepares students to lead mission driven organizations and manage their fundraising efforts. The program's unique focus on innovation and new technologies as well as public-private partnerships helps prepare students for a wide range of jobs in nonprofit organizations.
The MPA Concentration allows students to focus their studies on a variety nonprofit and public organizations. Additionally, it addresses some of most pressing issues that nonprofit and public professionals face. It also allows students the most flexibility in designing their studies, with the ability to concentrate in nonprofit management or public administration.
Master's degrees in nonprofit and public management often combine hands on experience with classroom learning. Internships and capstone projects give students real-world experience. The program gives students the opportunity to expand their professional network and meet people from non-profit and community-based organizations.
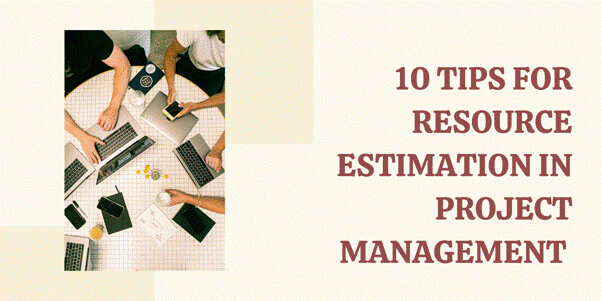
FAQ
What are some of the common mistakes made by managers?
Sometimes managers make their job harder than they need to.
They may not delegate enough responsibilities and not provide sufficient support.
Managers often lack the communication skills necessary to motivate and guide their teams.
Managers set unrealistic expectations and make it difficult for their team.
Managers may choose to solve every problem all by themselves, instead of delegating to others.
What is a fundamental management tool for decision-making?
The decision matrix is a powerful tool that managers can use to help them make decisions. It helps them to think strategically about all options.
A decision matrix can be used to show alternative options as rows or columns. This allows one to see how each alternative impacts other options.
In this example, we have four possible alternatives represented by the boxes on the left side of the matrix. Each box represents an option. The top row represents the current state of affairs, and the bottom row is indicative of what would happen in the event that nothing were done.
The middle column shows the effect of choosing Option 1. In this case, it would mean increasing sales from $2 million to $3 million.
The next two columns show the effects of choosing Options 2 and 3. These positive changes result in increased sales of $1 million and $500,000. But, they also have some negative consequences. Option 2 increases costs by $100 thousand, while Option 3 decreases profits to $200 thousand.
Finally, the last column shows the results of choosing Option 4. This means that sales will decrease by $1 million.
The best thing about a decision matrix is the fact that you don't have to remember which numbers go with what. The best thing about a decision matrix is that you can simply look at the cells, and immediately know whether one option is better or not.
This is because your matrix has already done the hard work. It's simply a matter of comparing the numbers in the relevant cells.
Here's an example of how you might use a decision matrix in your business.
It is up to you to decide whether to spend more money on advertising. If you do, you'll be able to increase your revenue by $5 thousand per month. You'll also have additional expenses up to $10,000.
Look at the cell immediately below the one that states "Advertising" to calculate the net investment in advertising. It's $15,000. Advertising is worth much more than the investment cost.
What are the three basic management styles?
The three basic management styles are: authoritarian, laissez-faire, and participative. Each style has strengths and flaws. What style do you prefer? Why?
Authoritarian – The leader sets a direction and expects everyone follows it. This style is best when the organization has a large and stable workforce.
Laissez-faire – The leader gives each individual the freedom to make decisions for themselves. This style is best when the organization has a small but dynamic group.
Participative - Leaders listen to all ideas and suggestions. This style is most effective in smaller organizations, where everyone feels valued.
How can a manager improve his/her managerial skills?
It is important to have good management skills.
Managers need to monitor their subordinates' performance.
It is important to take immediate action if your subordinate doesn't perform as expected.
You should be able pinpoint what needs to improve and how to fix it.
What are management concepts, you ask?
Management concepts are the practices and principles managers use to manage people or resources. They cover topics such as job descriptions and performance evaluations, human resource policies, training programs, employee motivation, compens systems, organizational structure, among others.
How can we create a culture of success in our company?
A culture of respect and value within a company is key to a productive culture.
It is based on three principles:
-
Everybody can contribute something valuable
-
Fair treatment of people is the goal
-
People and groups should respect each other.
These values are reflected in the way people behave. They will show consideration and courtesy to others.
They will listen respectfully to the opinions of others.
They encourage others to express their feelings and ideas.
Additionally, the company culture encourages open communication as well as collaboration.
People can freely express their opinions without fear or reprisal.
They know mistakes will be accepted as long as they are dealt with honestly.
Finally, the company culture promotes honesty and integrity.
Everyone knows that they must always tell truth.
Everyone understands that there are rules and regulations which apply to them.
People don't expect special treatment or favors.
Statistics
- 100% of the courses are offered online, and no campus visits are required — a big time-saver for you. (online.uc.edu)
- The average salary for financial advisors in 2021 is around $60,000 per year, with the top 10% of the profession making more than $111,000 per year. (wgu.edu)
- Our program is 100% engineered for your success. (online.uc.edu)
- Your choice in Step 5 may very likely be the same or similar to the alternative you placed at the top of your list at the end of Step 4. (umassd.edu)
- Hire the top business lawyers and save up to 60% on legal fees (upcounsel.com)
External Links
How To
What is Lean Manufacturing?
Lean Manufacturing uses structured methods to reduce waste, increase efficiency and reduce waste. These processes were created by Toyota Motor Corporation, Japan in the 1980s. The primary goal was to make products with lower costs and maintain high quality. Lean manufacturing is about eliminating redundant steps and activities from the manufacturing process. It consists of five basic elements: pull systems, continuous improvement, just-in-time, kaizen (continuous change), and 5S. The production of only what the customer needs without extra work is called pull systems. Continuous improvement means continuously improving on existing processes. Just-in-time refers to when components and materials are delivered directly to the point where they are needed. Kaizen refers to continuous improvement. It is achieved through small changes that are made continuously. Last but not least, 5S is for sort. These five elements are used together to ensure the best possible results.
Lean Production System
Six key concepts form the foundation of the lean production system:
-
Flow is about moving material and information as near as customers can.
-
Value stream mapping is the ability to divide a process into smaller tasks, and then create a flowchart that shows the entire process.
-
Five S's – Sort, Put In Order Shine, Standardize and Sustain
-
Kanban – visual signals like colored tape, stickers or other visual cues are used to keep track inventory.
-
Theory of constraints: Identify bottlenecks and use lean tools such as kanban boards to eliminate them.
-
Just-in-time - deliver components and materials directly to the point of use;
-
Continuous improvement - incremental improvements are made to the process, not a complete overhaul.