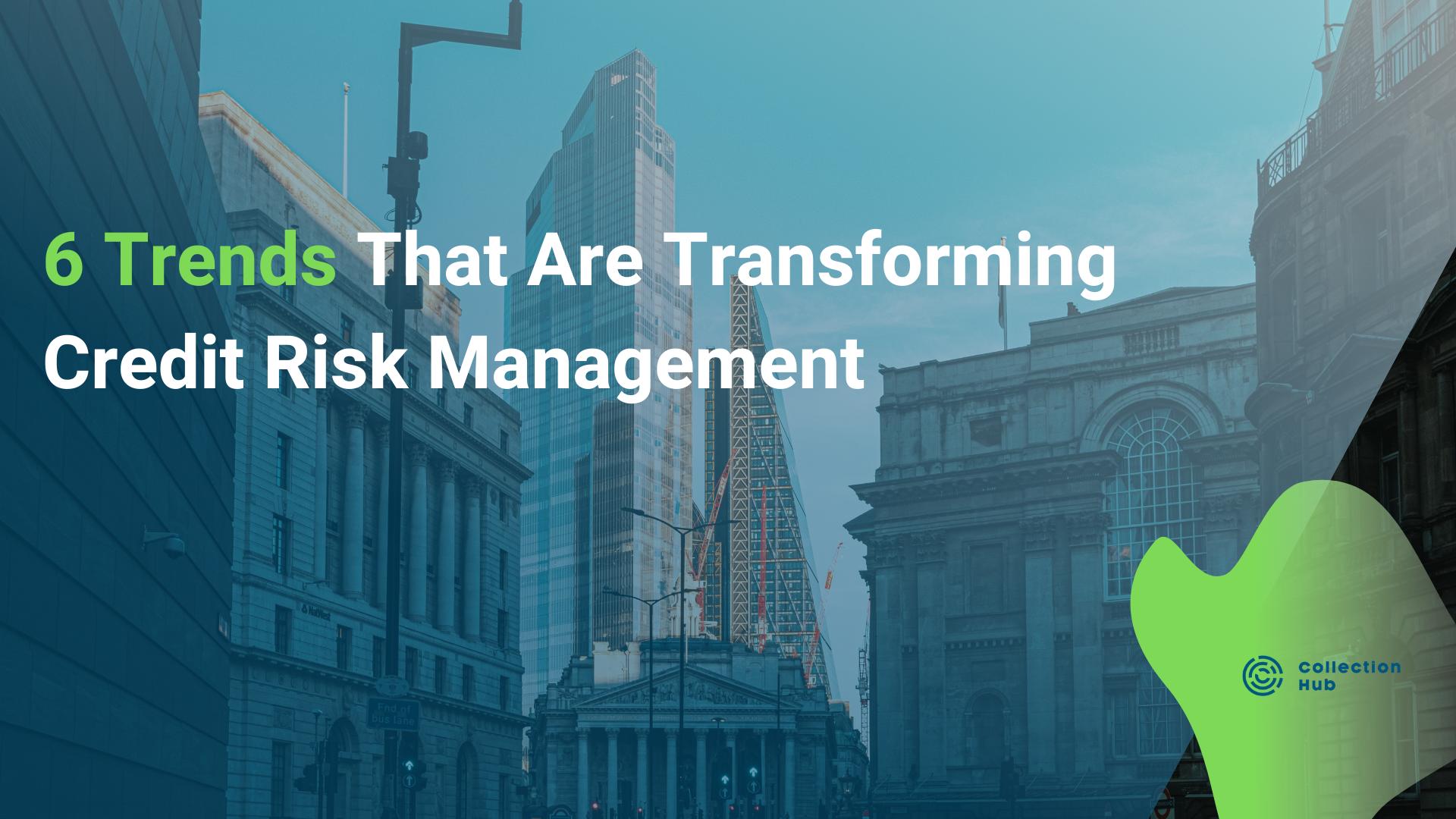
The hierarchy is a way to protect workers from dangers. It is widely accepted by many safety agencies and is commonly used in practice. It is taught to industry managers, who then implement it as a standard procedure. However, this system can be modified in certain ways. To learn more, please check out our guide to the NFPA 70E hazard classification system and the ARECC variation. Once you have this information, you can better apply the hierarchy to your workplace.
NFPA 70E
NFPA 70E is a set of standards for electrical safety in the workplace. New 2018 edition contains Annex Q, which describes human performance as well human error and potential consequences. This section provides a hierarchy for controlling hazards, and prioritizes their elimination. The first step in removing electrical hazards is to remove the source or hazard. Personal protective equipment should be used only as a last resort.
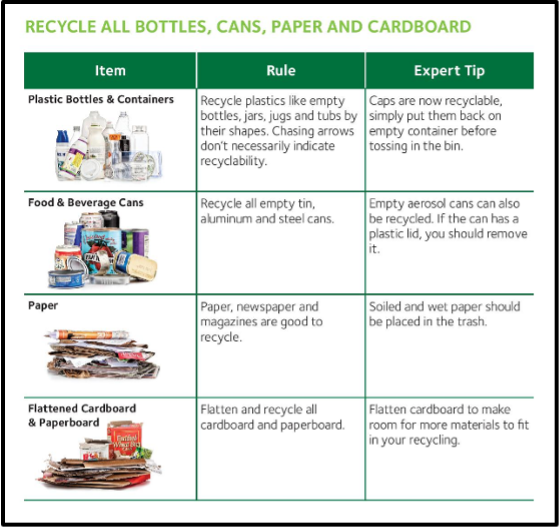
The next step in reducing the severity of risks is to assess the extent of your exposure. Engineering controls can reduce hazardous substance exposure, but they are not able to eliminate the hazards completely. The hierarchy of control's goal is to reduce the severity of hazards and prevent them from happening. An engineering control could be a vaporizer, fog machine, ventilation system, or fire alarm.
Appendices to the NFPA70E standard are also available. These documents provide information about specific procedures and practices and guidance on how to follow them. Appendices contain sample forms, PPE guidance and design requirements as well as risk assessment guidelines. Annexes provide information on how to implement the standard. In some cases, they may provide specific information that can be helpful in ensuring the safety of a building or workplace.
ARECC variation
The ARECC variation in the hierarchy of control is a method used to reduce the risk of exposure to a given hazard. This system is traditionally used in the United States and Canada, but it has been adapted in other countries. Some countries put isolation before engineering controls while others combine both. The ARECC variety includes warnings and employee education. Important to understand that warnings can't eliminate all hazards from a workplace.
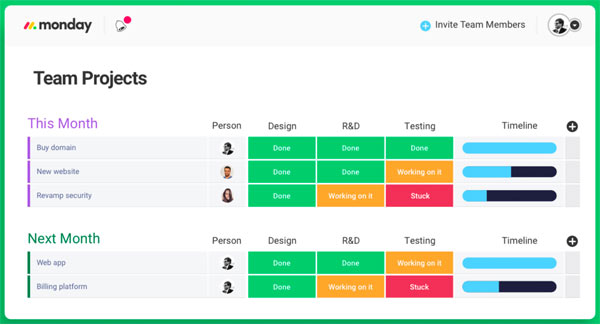
The ARECC hierarchy, or set of controls, is a framework that promotes occupational safety and health. It prioritizes the most effective solutions by identifying feasible options. The hierarchy contains five categories of controls: engineering controls and administrative controls. Each category has unique strengths and weaknesses. They are all important for specific situations. Some of the controls that are included in the ARECC hierarchy are more effective than others.
FAQ
How does a manager learn to manage?
Through demonstrating good management skills at every opportunity
Managers must continuously monitor the performance levels of their subordinates.
You must act quickly if you notice that your subordinate isn’t performing to their standards.
You should be able pinpoint what needs to improve and how to fix it.
What are the main management skills?
Managerial skills are crucial for every business owner, regardless of whether they run a small store in their locality or a large corporation. These skills include the ability of managing people, finances, time, space, and other factors.
Management Skills are also needed when you're setting goals and objectives, planning strategies, leading teams, motivating employees, resolving problems, creating policies and procedures, and managing change.
As you can see, there are many managerial responsibilities!
What is Six Sigma?
Six Sigma uses statistical analyses to locate problems, measure them, analyze root cause, fix problems and learn from the experience.
The first step to solving the problem is to identify it.
Next, data are collected and analyzed in order to identify patterns and trends.
Next, corrective steps are taken to fix the problem.
Finally, data is reanalyzed to determine whether the problem has been eliminated.
This cycle continues until the problem is solved.
What are the main four functions of management
Management is responsible of planning, organizing, leading, and controlling people as well as resources. It includes creating policies and procedures, as well setting goals.
Management is the ability to direct, coordinate, control, motivate, supervise, train, and evaluate an organization's efforts towards achieving its goals.
The four main functions of management are:
Planning – Planning involves deciding what needs to happen.
Organizing: Organizing refers to deciding how things should work.
Directing - This refers to getting people follow instructions.
Controlling: Controlling refers to making sure that people do what they are supposed to.
Statistics
- Your choice in Step 5 may very likely be the same or similar to the alternative you placed at the top of your list at the end of Step 4. (umassd.edu)
- The profession is expected to grow 7% by 2028, a bit faster than the national average. (wgu.edu)
- The BLS says that financial services jobs like banking are expected to grow 4% by 2030, about as fast as the national average. (wgu.edu)
- 100% of the courses are offered online, and no campus visits are required — a big time-saver for you. (online.uc.edu)
- The average salary for financial advisors in 2021 is around $60,000 per year, with the top 10% of the profession making more than $111,000 per year. (wgu.edu)
External Links
How To
How does Lean Manufacturing work?
Lean Manufacturing is a method to reduce waste and increase efficiency using structured methods. These processes were created by Toyota Motor Corporation, Japan in the 1980s. It was designed to produce high-quality products at lower prices while maintaining their quality. Lean manufacturing seeks to eliminate unnecessary steps and activities in the production process. It is made up of five elements: continuous improvement, continuous improvement, just in-time, continuous change, and 5S. It is a system that produces only the product the customer requests without additional work. Continuous improvement is the continuous improvement of existing processes. Just-in time refers to components and materials being delivered right at the place they are needed. Kaizen means continuous improvement. Kaizen involves making small changes and improving continuously. The 5S acronym stands for sort in order, shine standardize and maintain. These five elements are combined to give you the best possible results.
The Lean Production System
The lean production system is based on six key concepts:
-
Flow - focuses on moving information and materials as close to customers as possible.
-
Value stream mapping - Break down each stage in a process into distinct tasks and create an overview of the whole process.
-
Five S's – Sort, Put In Order Shine, Standardize and Sustain
-
Kanban – visual signals like colored tape, stickers or other visual cues are used to keep track inventory.
-
Theory of constraints - identify bottlenecks in the process and eliminate them using lean tools like kanban boards;
-
Just-in-time delivery - Deliver components and materials right to your point of use.
-
Continuous improvement: Make incremental improvements to the process instead of overhauling it completely.