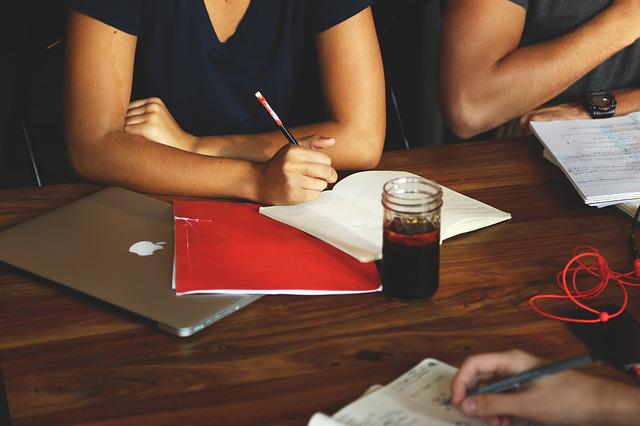
A safe management solution is a combination of safes placed in retail locations. Each safe is equipped with a small amount control software. It is only possible to have well-defined functions in the terminal units' resident memory or processing capacity. Key control parameters are achieved through a central server, which can be a network of servers or a cloud server. The safes themselves are typically not connected to an internet connection. External hardware is not required.
Safe management system collects data
A safety management program is a combination of processes and procedures designed to reduce the likelihood of safety incidents. These systems can be highly effective but cannot eliminate all possible errors because they would not be practical, feasible, workable, or cost-effective. A safety management system cannot measure the behavior of every worker, so the information collected by it is not completely reliable. However, these information are still vital in order to ensure safety at work.
Managers should have access to the system's data and be able analyze it to improve safety performance. This data can be used in statistical techniques as well as other sources. Information should be clearly presented. Moreover, the reports should be able to identify trends that can help managers allocate resources more effectively. Safety management systems need to be flexible enough for these trends. Additionally, the information collected must be easy to interpret so that it can be acted on.
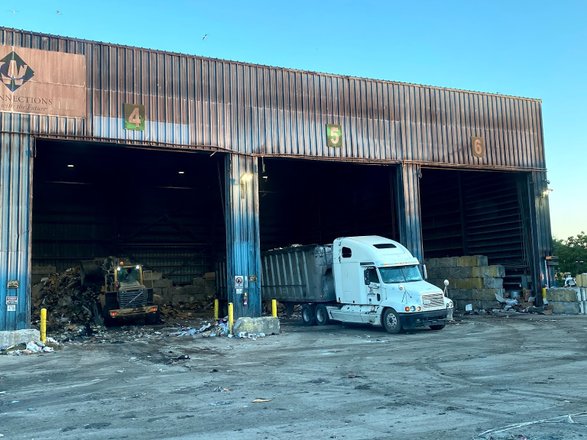
Documentation
A key component of developing a safe management program is good documentation. This helps to avoid making mistakes and prevents you from having to re-learn old lessons. A typical management system will include processes to handle miscellaneous statements and process safety management. It also should contain labeling and record preservation. Documentation is essential for preventing injuries, accidents, or illnesses. Stakeholders are able to easily access the document, which contains best practices.
A solid SMS documentation system should include all the applicable national and international regulations, processes and procedures, as well as specific templates for each process and lines of accountability. It should outline the structure and organization of the safety system as well as the outputs of SMS. The documentation should also include explicit guidelines for the maintenance of records. To be effective safety documentation must be approved in writing by authorities. You must also make sure that it reflects the latest changes made.
Risk matrix
A risk matrix can be a valuable tool for managing risks within an organization. A risk matrix allows you to prioritize risks according to their impact. The risk matrix utilizes categories such as Impact, Probability, and Impact to determine the risk level. Once you have determined the risks for your business, you can use the risk matrix to improve your existing risk control measures and reinforce your proactive safety culture. Here are some suggestions to help you make a risk matrix.
First, create and maintain a risk matrix. This document shows three types. Each level represents a different risk. In Figure A1, the ground level represents the quantitative relationship between severity and probability. The middle floor represents linear scaling, while the top floor is carpeted. Each column represents a different risk, which is represented by its corresponding numerical value. The risk indicator in each cell is determined by the formula: Ri x Cj.
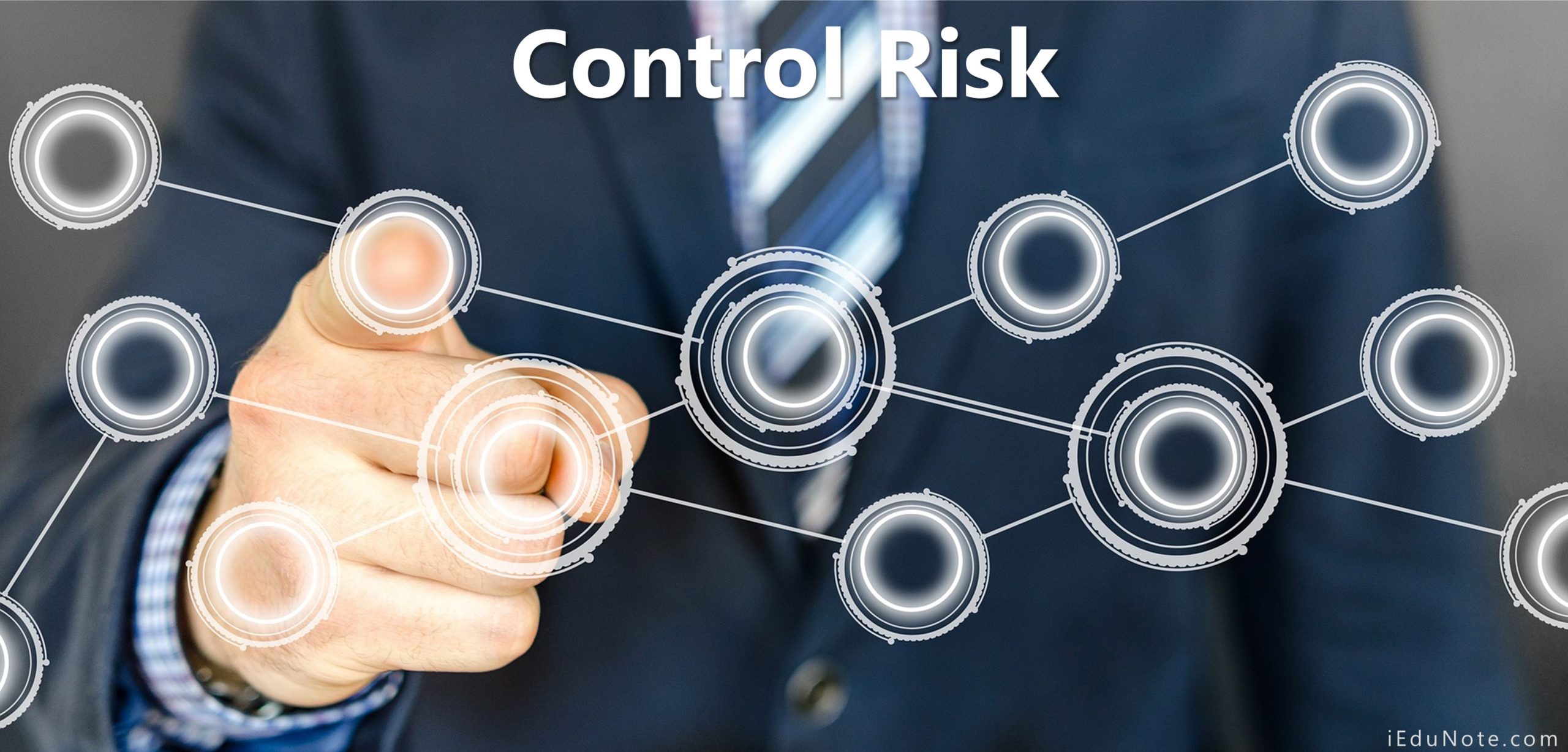
Safety assurance
It is crucial to establish the safety assurance procedures in a safety management program. Safety assurance procedures should contain all resources, reporting requirements and disciplinary actions. It should also contain a safety policy, which must be communicated to all levels of the organization and is reviewed frequently. The safety policy should identify the different levels of management who have authority to make decisions about safety. The certificate holder should also indicate the types and levels of personnel and resources responsible for maintaining safety management.
Safety assurance was developed as a response to increasing industrial exploitation. The industrial revolution created significant commercial opportunities for Western societies. Business owners were driven to use a low-skilled workforce including child labour and rural migrants to meet their financial obligations. In such circumstances, it was not uncommon for people to be injured, killed, or have accidents. Safety management emerged to be a counterweight for the exploitation of labour.
FAQ
What is the best way to motivate your employees as a manager?
Motivation can be defined as the desire to achieve success.
Enjoyable activities can motivate you.
You can also get motivated by seeing your contribution to the success or the improvement of the organization.
If you are a doctor and want to be one, it will likely be more rewarding to see patients than to read medical books every day.
Another type of motivation comes from within.
For example, you might have a strong sense of responsibility to help others.
Or you might enjoy working hard.
If you don't feel motivated, ask yourself why.
Then think about how you can make your life more motivating.
Why does it sometimes seem so difficult to make good business decisions?
Businesses are complex systems, and they have many moving parts. The people who run them must juggle multiple priorities at once while also dealing with uncertainty and complexity.
It is important to understand the effects of these factors on the system in order to make informed decisions.
You must first consider what each piece of the system does and why. It is important to then consider how the individual pieces relate to each other.
You should also ask yourself if there are any hidden assumptions behind how you've been doing things. If they don't, you may want to reconsider them.
Try asking for help from another person if you're still stuck. They may see things differently from you and have insights that could help you find a solution.
What are management concepts?
Management Concepts are the principles and practices managers use to manage people and resources. They include such topics as human resource policies, job descriptions, performance evaluations, training programs, employee motivation, compensation systems, organizational structure, and many others.
What is Six Sigma?
It's a method for quality improvement that focuses on customer service as well as continuous learning. The goal is to eradicate defects through statistical techniques.
Six Sigma was developed at Motorola in 1986 as part of its efforts to improve manufacturing processes.
The idea spread quickly throughout the industry, and today, many organizations are using six sigma methods to improve product design, production, delivery, and customer service.
What kind people use Six Sigma?
Six-sigma will be well-known to anyone who has worked in operations research or statistics. Anybody involved in any aspect or business can benefit.
Because it requires a high degree of commitment, only leaders with strong leadership skills can implement it successfully.
Statistics
- Our program is 100% engineered for your success. (online.uc.edu)
- The BLS says that financial services jobs like banking are expected to grow 4% by 2030, about as fast as the national average. (wgu.edu)
- Hire the top business lawyers and save up to 60% on legal fees (upcounsel.com)
- This field is expected to grow about 7% by 2028, a bit faster than the national average for job growth. (wgu.edu)
- The average salary for financial advisors in 2021 is around $60,000 per year, with the top 10% of the profession making more than $111,000 per year. (wgu.edu)
External Links
How To
How do you do the Kaizen method?
Kaizen means continuous improvement. Kaizen is a Japanese concept that encourages constant improvement by small incremental changes. It is a process where people come together to improve their processes.
Kaizen is one the most important methods of Lean Manufacturing. Employees responsible for the production line should identify potential problems in the manufacturing process and work together to resolve them. This will increase the quality and decrease the cost of the products.
Kaizen is a way to raise awareness about what's happening around you. It is important to correct any problems immediately if they are discovered. So, if someone notices a problem while working, he/she should report it to his/her manager.
Kaizen has a set of basic principles that we all follow. Always start with the end product in mind and work our way back to the beginning. In order to improve our factory's production, we must first fix the machines producing the final product. First, we fix machines that produce components. Next, we fix machines that produce raw material. Then, we fix those who work directly with the machines.
This approach is called 'kaizen' because it focuses on improving everything steps by step. When we are done fixing the whole factory, we go back to the beginning and continue until we reach perfection.
How to measure kaizen's effectiveness in your business is essential to implement it. There are many methods to assess if kaizen works well. Another way to determine if kaizen is working well is to look at the quality of the products. Another method is to determine how much productivity has improved since the implementation of kaizen.
If you want to find out if your kaizen is actually working, ask yourself why. Is it because the law required it or because you want to save money. Did you really think that it would help you achieve success?
Congratulations if you answered "yes" to any of the questions. You are now ready to begin kaizen.