
An ISO document contains a number of rules that are crucial for readers to understand. For example, abbreviations must be precise and unambiguous. Certain forms of punctuation should be avoided. These include symbols to indicate quantities and language. These guidelines make it easier for readers to understand the ISO document and its contents.
Formulas
The implementation of electronic ISO documents forms can help improve customer satisfaction, regulatory compliance, quality, and company processes. Keep these forms simple and break them into data types. Make sure they are part a process. Agile development is essential. Users' requirements should be gathered early. User testing is also a good idea. This can help you discover issues that you didn't anticipate. Software-specific training should be provided to all users.
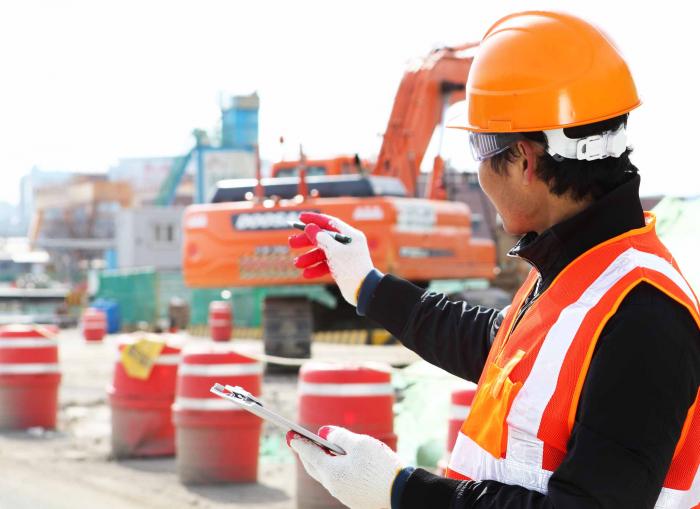
Symbols for quantities
In ISO documents, quantities are represented with symbols. These symbols, which are often abbreviated terms and written in italics instead of numbers or words written in lowercase, are used to represent quantities in ISO documents. Some abbreviations can also have special meanings. For example, 'net current value' or the 'internal rates of return'. The standard also specifies what symbols should be used when referring to quantities.
Acronyms
Some common acronyms will be familiar to you if you are a regular reader of ISO documents. The first is CAR, or Corrective Action Request. This acronym refers to an activity that originates a Corrective Action (CA). This typically involves investigating the root cause of a problem and then preventing it from happening again. It can also refer to the whole Corrective Action Lifecycle.
Language
Language of ISO document plays a crucial role in ensuring that the document can be understood by its intended audience. There are certain conventions that characterize this language. Although abbreviations may be used in common usage, it is important that the first word of each term be capitalized. For example, the abbreviation "ac" for alternating current is acceptable, but "d.c." is not acceptable for radio frequency.
Formatting
Documentation is an important aspect of ISO standards. Some organizations overdocument and create an inflexible system. You can avoid this problem by making sure that your documentation follows the correct format and style.
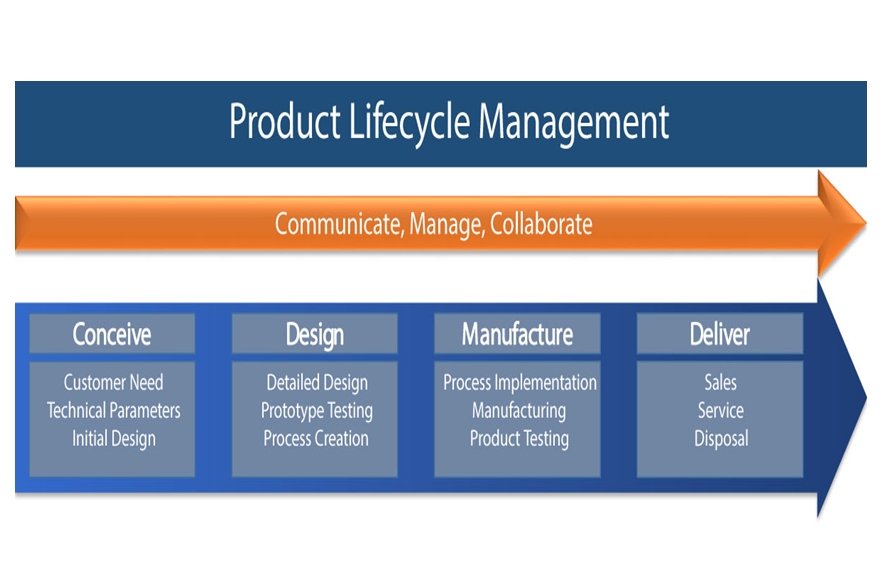
Publishing
ISO publishes documents in different formats. ISO documents are known as IEC standards and ISO standards. They are the results of a committee called ISO/IEC JTC 1 and the American Society for Testing and Materials. ISO standards can differ from ASTM standards. Some standards are not complete and are not published. Their designations are often not included in the titles of published works.
FAQ
What are the four main functions of management?
Management is responsible to plan, organize, direct, and control people and resources. It includes the development of policies and procedures as well as setting goals.
Management is the ability to direct, coordinate, control, motivate, supervise, train, and evaluate an organization's efforts towards achieving its goals.
Management has four primary functions:
Planning - Planning refers to deciding what is needed.
Organizing: Organizing refers to deciding how things should work.
Direction - This is the art of getting people to follow your instructions.
Controlling – This refers to ensuring that tasks are carried out according to plan.
What's the difference between Six Sigma and TQM?
The main difference between these two quality management tools is that six sigma focuses on eliminating defects while total quality management (TQM) focuses on improving processes and reducing costs.
Six Sigma is a methodology for continuous improvement. It emphasizes the elimination and improvement of defects using statistical methods, such as control charts, P-charts and Pareto analysis.
This method aims to reduce variation in product production. This is accomplished by identifying the root cause of problems and fixing them.
Total quality management involves measuring and monitoring all aspects of the organization. It also involves training employees to improve performance.
It is often used to increase productivity.
What are the three main management styles you can use?
The three major management styles are authoritarian (left-faire), participative and laissez -faire. Each style is unique and has its strengths as well as weaknesses. Which style do YOU prefer? Why?
Authoritarian – The leader sets a direction and expects everyone follows it. This style works best if the organization is large and stable.
Laissez-faire – The leader gives each individual the freedom to make decisions for themselves. This style works best when the organization is small and dynamic.
Participative: The leader listens to everyone's ideas and suggestions. This style works best in smaller organizations where everyone feels valued.
Statistics
- UpCounsel accepts only the top 5 percent of lawyers on its site. (upcounsel.com)
- Our program is 100% engineered for your success. (online.uc.edu)
- The BLS says that financial services jobs like banking are expected to grow 4% by 2030, about as fast as the national average. (wgu.edu)
- The average salary for financial advisors in 2021 is around $60,000 per year, with the top 10% of the profession making more than $111,000 per year. (wgu.edu)
- This field is expected to grow about 7% by 2028, a bit faster than the national average for job growth. (wgu.edu)
External Links
How To
How do I get my Six Sigma License?
Six Sigma is a tool for quality management to improve processes and increase efficiency. It's a methodology that helps companies achieve consistent results from their operations. The name is derived from the Greek word "sigmas", which means "six". Motorola invented this process in 1986. Motorola realized that it was important to standardize manufacturing processes so they could produce products quicker and cheaper. Because of the number of people involved in the work, they had problems maintaining consistency. To resolve this issue, they used statistical tools like Pareto analysis and control charts. They would then apply these techniques to all aspects of their operation. This technique would enable them to make improvements in areas that needed it. Three main steps are involved when you're trying to go through the whole process of getting your Six Sigma certification. Find out if you are qualified. You will need classes to pass before you can begin taking tests. After you have passed the classes, you can start taking the exams. It is important to review everything that you have learned in class. Once you have completed the class, you will be ready for the test. If you pass, you'll get certified. Finally, you will be able add your certifications onto your resume.