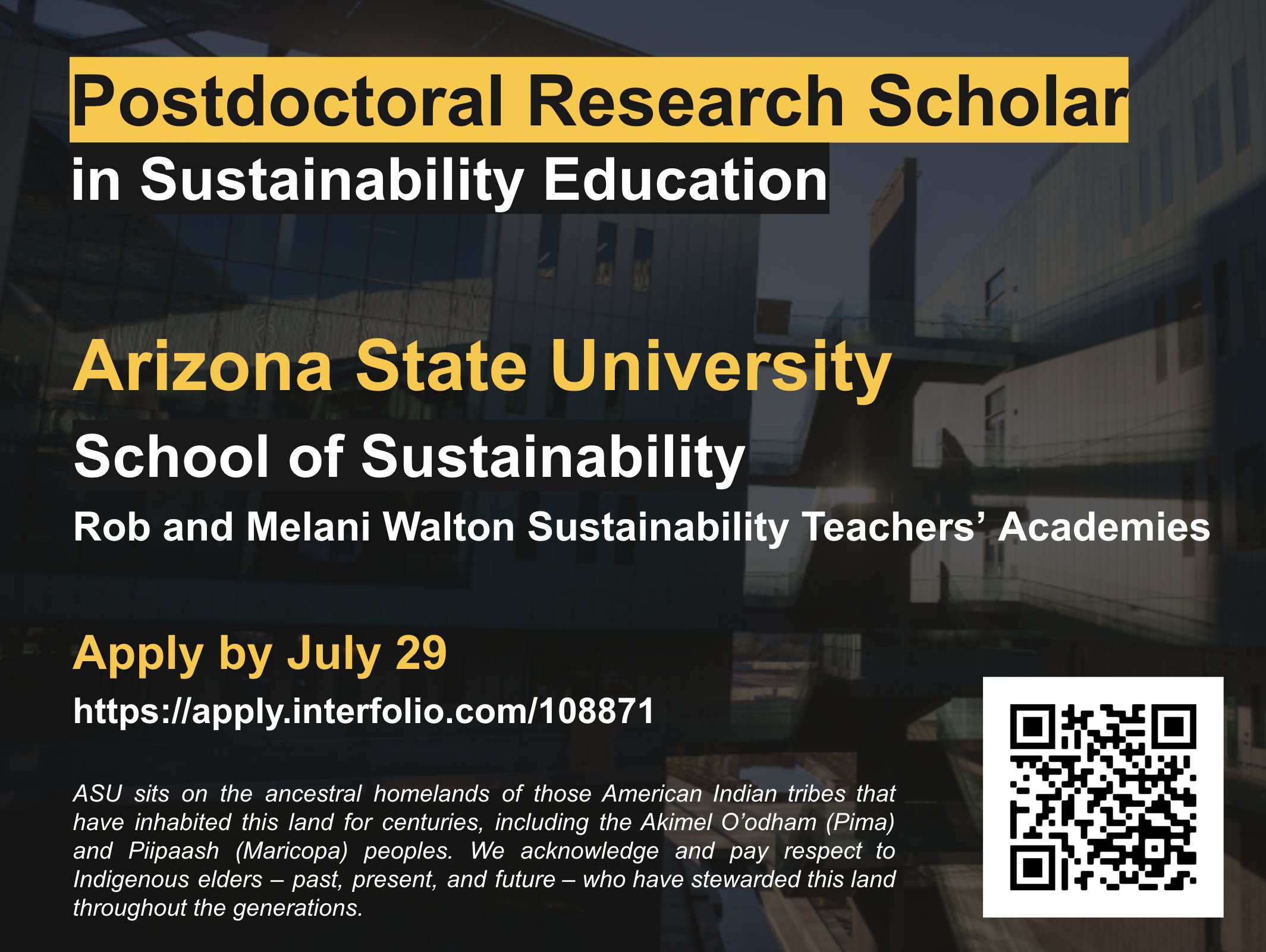
Logistics refers to the movement, storage and distribution of goods, from their initial production through final delivery. Logistics industry includes many companies, people, activities, data, and information that makes goods available for purchase. A logistics supply chain is a collaborative effort between multiple stakeholders. Although many companies are focused on logistics, there is a lot more to the process than just logistics. These are some of the various types of logistical systems. You can read on to learn about these systems and how you can improve your company’s supply chain operations.
Logistics is the movement, storage, and distribution of goods from initial production to final delivery
Logistics involves the efficient movement and storage of products from initial production to final delivery. If flows are optimized, products reach the customers at just the right time, at exactly the right location, and at the perfect cost. Here are seven rights to logistics. The first is to arrive at the right time. Products should be delivered to customers on time, without delay, in the right condition.
Inbound logistics focuses on the inbound movement of materials and products to manufacturers, whereas outbound logistics focuses on the outbound flow of goods and information from sources outside of the business. Inbound logistics focuses on acquiring materials and arranging inbound transportation, storage, and distribution to customers. Reverse logistic deals with return shipment of finished goods and their packaging. Some cases may include reusable packaging and disposal.
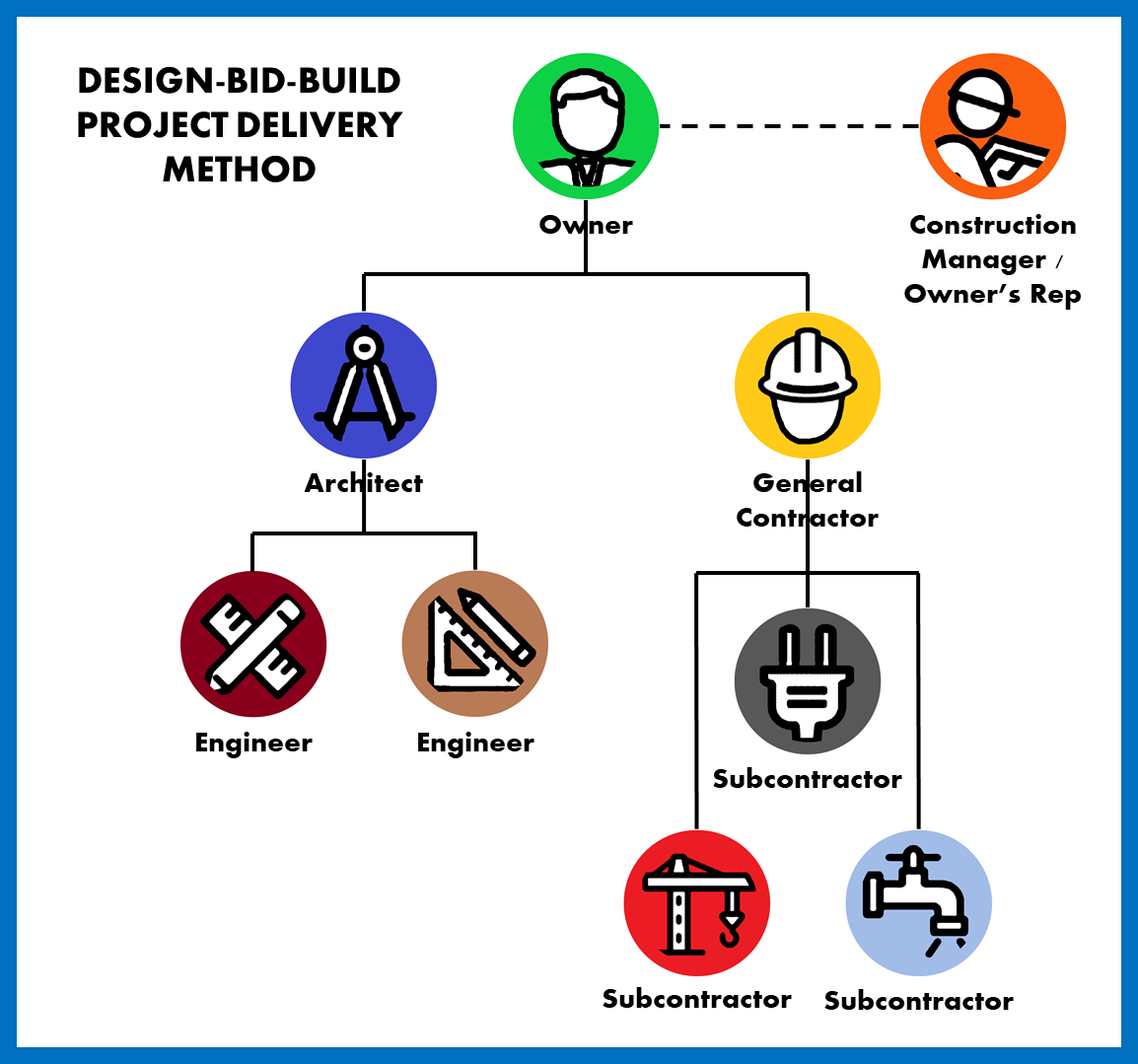
It is a risk-adjusted enterprise
A risk-adjusted or RAR investment is an investment that has more risk than a normal business investment. The opportunity cost of risk is the difference between risk-adjusted and normal business investment yields. RAR helps business owners to manage cash flows in different areas of their business, and reduces the risk of investment.
It's a small piece of a larger, collaborative supply network
A highly integrated supply chain is an interdependent network that relies on timely deliveries. In such a chain, failure to deliver could bring the whole chain to a halt. Even the best logistics providers and suppliers cannot avoid every disruption. To ensure smooth and efficient operation of the chain, it is vital that everyone evaluates the potential risks involved in any given system.
The positive effects of collaborations between retailers and manufacturers can be beneficial for both. A recent collaboration between a retailer in the United States and a major U.S. retail chain led to a lower logistics cost between the factory, the store and the factory. Collaborations in this area can also help retailers increase their sales. Manufacturers can also collaborate with retailers to lower transportation and labor costs.
It involves software
Supply management software can help companies manage their entire supply network. The software can manage all aspects, from vendor relationships through to transactions. Supply chain management software should be used regardless of whether you run a small business or large corporation. These software can help you manage inventory and supplier relationships as well as flow of data within your company. These programs may include all stages of product development, including warehousing and shipping. They might also manage inventory and offer insight into trends or demand.
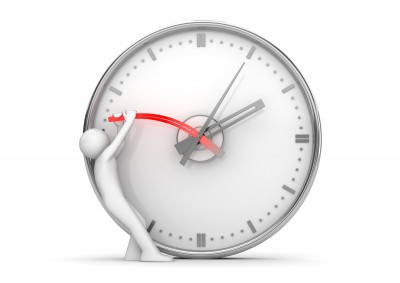
Software for logistics management can improve inventory management, real time fleet management, and streamline communication. It can also increase customer service. It automates day-to-day tasks and gives business owners actionable insights. It also improves communication and inventory processes, which is essential for the successful management of supply chains. These applications can help you improve customer service and increase profitability. If you're considering buying software for your enterprise you might be curious what the benefits are.
FAQ
What does it mean to say "project management"
We mean managing the activities involved in carrying out a project.
We help you define the scope of your project, identify the requirements, prepare the budget, organize the team, plan the work, monitor progress and evaluate the results before closing down the project.
Why does it sometimes seem so difficult to make good business decisions?
Complex systems with many moving parts are the hallmark of businesses. Their leaders must manage multiple priorities, as well as dealing with uncertainty.
The key to making good decisions is to understand how these factors affect the system as a whole.
You must first consider what each piece of the system does and why. Next, consider how each piece interacts with the others.
You should also ask yourself if there are any hidden assumptions behind how you've been doing things. If so, it might be worth reexamining them.
Asking for assistance from someone else is a good idea if you are still having trouble. They may see things differently from you and have insights that could help you find a solution.
How can we make our company culture successful?
A company culture that values and respects its employees is a successful one.
It's based on three main principles:
-
Everyone has something to contribute
-
People are treated with respect
-
Respect is shared between individuals and groups
These values can be seen in the behavior of people. They will show consideration and courtesy to others.
They will be respectful of the opinions of other people.
These people will inspire others to share thoughts and feelings.
In addition, the company culture encourages open communication and collaboration.
People feel free to express their views openly without fear of reprisal.
They know mistakes will be accepted as long as they are dealt with honestly.
Finally, the company culture encourages honesty as well as integrity.
Everybody knows they have to tell the truth.
Everyone is aware that rules and regulations apply to them.
Nobody expects to be treated differently or given favors.
What are some common mistakes managers make?
Sometimes managers make it harder for their employees than is necessary.
They might not give enough support and delegate the right responsibilities to their staff.
A majority of managers lack the communication skills needed to motivate their team and lead them.
Some managers create unrealistic expectations for their teams.
Managers may prefer to solve every problem for themselves than to delegate responsibility.
What are management theories?
Management Concepts are the management principles and practices that managers use in managing people and resources. They cover topics like job descriptions (job descriptions), performance evaluations, training programmes, employee motivation and compensation systems.
What are the most important management skills?
Any business owner needs to be able to manage people, finances, resources and time. They include the ability to manage people, finances, resources, time, and space, as well as other factors.
When you need to manage people, set goals, lead teams, motivate them, solve problems, develop policies and procedures and manage change, management skills are essential.
As you can see there is no end to the number of managerial tasks.
Why is it important for companies to use project management techniques?
Project management techniques are used to ensure that projects run smoothly and meet deadlines.
Because most businesses depend heavily on project work to produce goods or services,
These projects must be managed efficiently and effectively by companies.
Companies could lose their time, reputation, and money without effective project management.
Statistics
- Our program is 100% engineered for your success. (online.uc.edu)
- Your choice in Step 5 may very likely be the same or similar to the alternative you placed at the top of your list at the end of Step 4. (umassd.edu)
- As of 2020, personal bankers or tellers make an average of $32,620 per year, according to the BLS. (wgu.edu)
- This field is expected to grow about 7% by 2028, a bit faster than the national average for job growth. (wgu.edu)
- The BLS says that financial services jobs like banking are expected to grow 4% by 2030, about as fast as the national average. (wgu.edu)
External Links
How To
How can you implement the Kaizen technique?
Kaizen means continuous improvement. The Japanese philosophy emphasizes small, incremental improvements to achieve continuous improvement. This term was created by Toyota Motor Corporation in 1950. It's a process where people work together to improve their processes continuously.
Kaizen is one the most important methods of Lean Manufacturing. The concept involves employees responsible for manufacturing identifying problems and trying to fix them before they become serious issues. This improves the quality of products, while reducing the cost.
The main idea behind kaizen is to make every worker aware of what happens around him/her. Correct any errors immediately to avoid future problems. So, if someone notices a problem while working, he/she should report it to his/her manager.
There are some basic principles that we follow when doing kaizen. Start with the end product, and then move to the beginning. To improve our factory, for example, we need to fix the machines that produce the final product. We then fix the machines producing components, and the machines producing raw materials. Then, we fix those who work directly with the machines.
This method is known as kaizen because it focuses upon improving every aspect of the process step by step. Once we have finished fixing the factory, we return to the beginning and work until perfection.
You need to know how to measure the effectiveness of kaizen within your business. There are several ways to determine whether kaizen is working well. One method is to inspect the finished products for defects. Another way is to see how much productivity has increased since implementing kaizen.
You can also find out if kaizen works by asking yourself why you decided to implement it. It was because of the law, or simply because you wanted to save some money. Did you really believe that it would be a success factor?
Congratulations if you answered "yes" to any of the questions. You are ready to start kaizen.