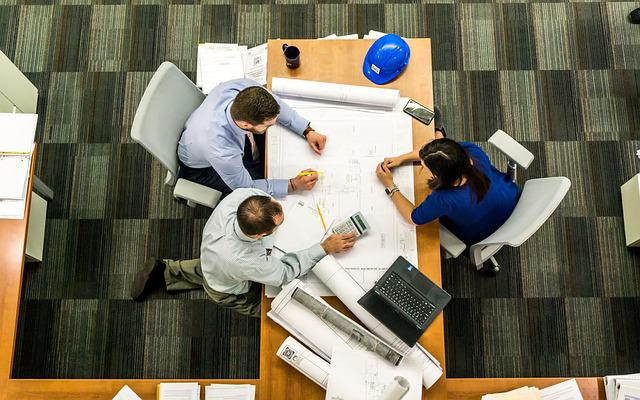
Risk assessments are a valuable tool that can help you determine whether your business may be at risk. An assessment should be performed on a regular basis. This will give a snapshot about the current risks and threats that are posed to your system. This will give you a snapshot of the risks and threats posed by your system.
Hazard identification
Risk assessment begins with hazard identification. Many people don't have the skills required to identify hazards correctly, so some legitimate risks may be overlooked. An anchor for the hazard identification process can encourage more people to identify hazards, and help reduce the likelihood of an overlooked risk. The study included 72 participants randomly assigned to high-anchor and low-anchor conditions. They also completed a five-factor personality test.
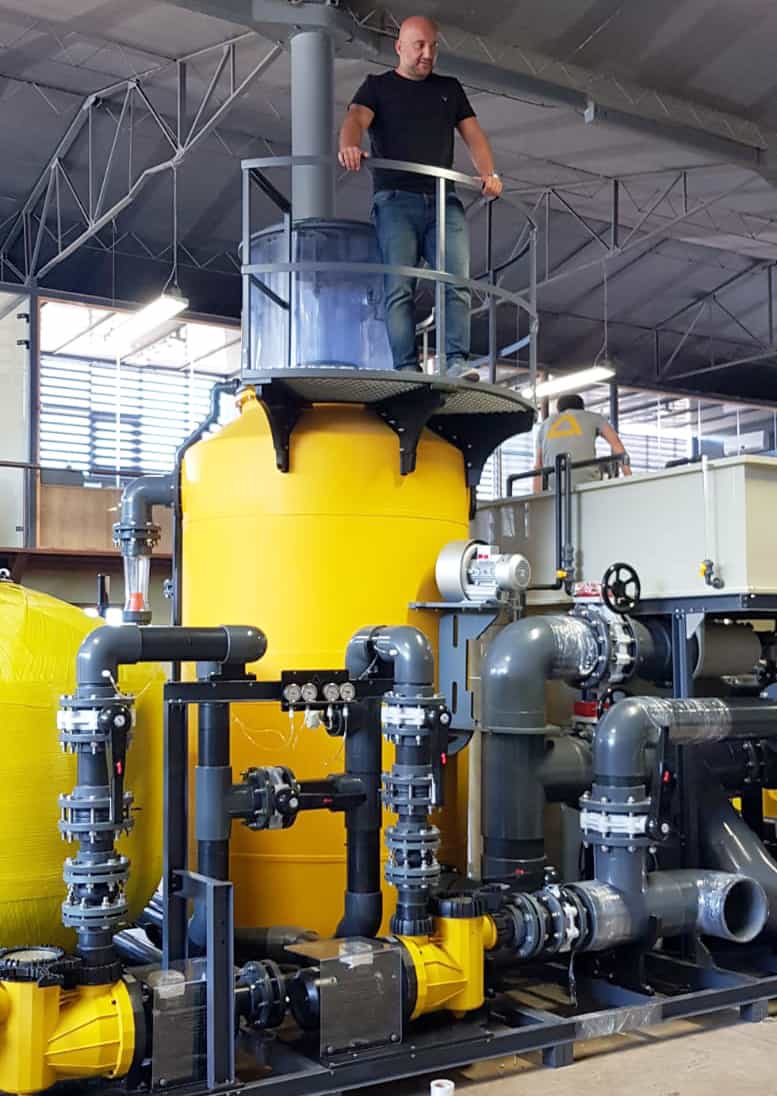
Document review
Ling is an aspiring project manager for a large internet business. Her first project involves the creation of privacy software solutions to a client. In order to identify project risks, she will use documentation review. Document review is a systematic review of project plans, assumptions, information, and other relevant data. These findings will be used to inform the risk assessment process. Not only can this review identify risks but it also helps to minimize risk exposure.
Influence diagrams
For capturing a sequence or decisions, influence diagrams can be a powerful tool. These diagrams are frequently used in risk management, project and other organizational disciplines. Influence diagrams allow participants to view the connections between different factors and actions, including the potential for harm or loss. They can be used to evaluate the risks associated in particular projects. These diagrams can be used to illustrate and group work.
Impact diagrams
An impact diagram is an effective tool to evaluate the relative risks involved in a project's risk assessment. They are a representation of the impact of each potential risk on the project. This analysis is usually done by the risk manager, or other people with knowledge about the risks. The results of the analysis can be ranked according to impact, duration uncertainty and probability of occurrence. These diagrams can help you determine which risks should be addressed first, and which ones need to be revised.
iAuditor
iAuditor for Risk Assessment is a digital tool that replaces pen & paper checklists with electronic reporting. This software will simplify your risk assessment process and make it more efficient. Start the process by downloading free templates. You can modify the checklists according to your requirements. Next, you can assign corrective action to your workers. After the assessment is completed, you will receive comprehensive reports that can be saved to your user account. These reports are available for sharing with others or can be updated as needed.
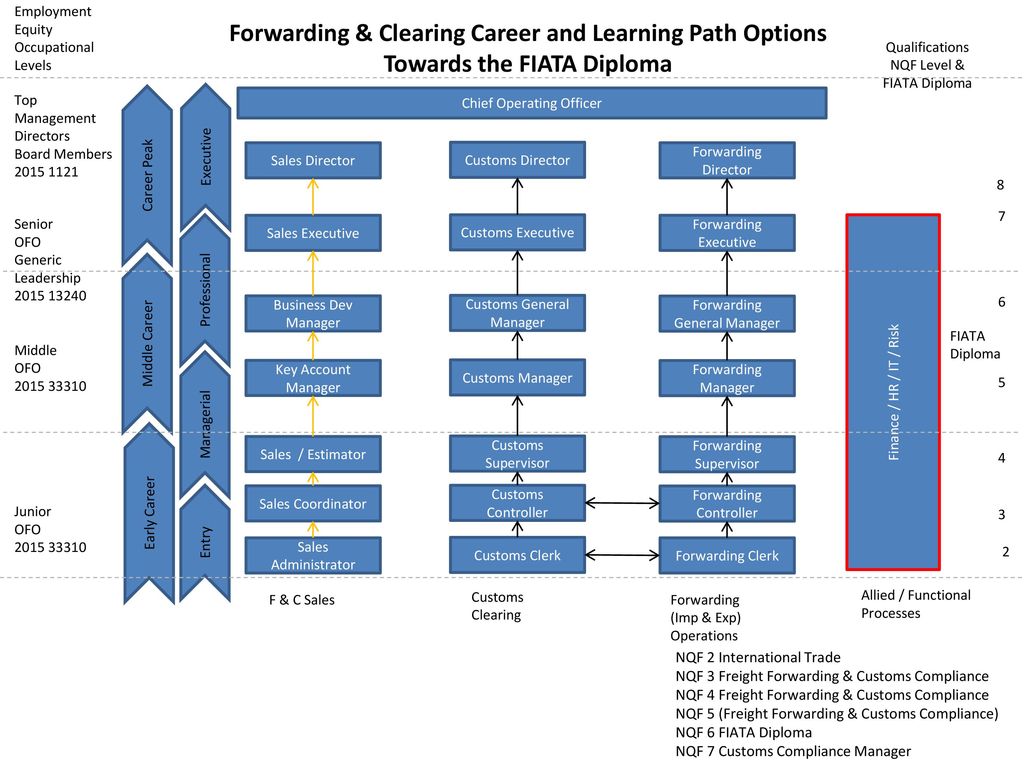
Corrective action
A corrective action refers to an appropriate response to a threat or possibility. The process can be very lengthy and time-consuming, and it's important to track the results to ensure that the action is successful. Corrective measures are not isolated events. They are part and parcel of the overall process. Monitoring the progress of corrective measures helps you to identify and resolve issues. This will enable you to improve overall performance.
FAQ
How do you effectively manage employees?
Managing employees effectively means ensuring that they are happy and productive.
This includes setting clear expectations for their behavior and tracking their performance.
Managers need to establish clear goals for their team and for themselves.
They need to communicate clearly with staff members. They must communicate clearly with staff members.
They must also keep records of team activities. These include:
-
What was the result?
-
How much work was done?
-
Who did it and why?
-
What was the moment it was completed?
-
Why did it happen?
This information can be used for monitoring performance and evaluating results.
Six Sigma is so popular.
Six Sigma can be implemented quickly and produce impressive results. Six Sigma provides a framework to measure improvements and allows companies to focus on the most important things.
What are the 3 main management styles?
There are three main management styles: participative, laissez-faire and authoritarian. Each style has its own strengths and weaknesses. What style do you prefer? Why?
Authoritarian - The leader sets the direction and expects everyone to comply with it. This style is best when the organization has a large and stable workforce.
Laissez-faire – The leader gives each individual the freedom to make decisions for themselves. This style works best when an organization is small and dynamic.
Participative - Leaders listen to all ideas and suggestions. This style works best in smaller organizations where everyone feels valued.
It seems so difficult sometimes to make sound business decisions.
Businesses are complex systems, and they have many moving parts. It is difficult for people in charge of businesses to manage multiple priorities simultaneously and also deal with uncertainty.
Understanding how these factors impact the whole system is key to making informed decisions.
You need to be clear about the roles and responsibilities of each system. It is important to then consider how the individual pieces relate to each other.
You need to ask yourself if your previous actions have led you to make unfounded assumptions. You might consider revisiting them if they are not.
You can always ask someone for help if you still have questions after all of this. They might have different perspectives than you, and could offer insight that could help you solve your problem.
What is the role of a manager in a company?
Managers' roles vary from industry to industry.
In general, a manager controls the day-to-day operations of a company.
He/she will ensure that the company fulfills its financial obligations.
He/she is responsible for ensuring that employees comply with all regulations and follow quality standards.
He/she plans new products and services and oversees marketing campaigns.
Why is project management so important?
To ensure projects run smoothly and meet deadlines, project management techniques are employed.
Because most businesses depend heavily on project work to produce goods or services,
These projects require companies to be efficient and effective managers.
Companies could lose their time, reputation, and money without effective project management.
What's the difference between leadership & management?
Leadership is all about influencing others. Management is about controlling others.
Leaders inspire followers, while managers direct workers.
Leaders inspire people to achieve success. Managers keep their workers focused.
A leader develops people; a manager manages people.
Statistics
- Hire the top business lawyers and save up to 60% on legal fees (upcounsel.com)
- The BLS says that financial services jobs like banking are expected to grow 4% by 2030, about as fast as the national average. (wgu.edu)
- This field is expected to grow about 7% by 2028, a bit faster than the national average for job growth. (wgu.edu)
- The average salary for financial advisors in 2021 is around $60,000 per year, with the top 10% of the profession making more than $111,000 per year. (wgu.edu)
- UpCounsel accepts only the top 5 percent of lawyers on its site. (upcounsel.com)
External Links
How To
What is Lean Manufacturing?
Lean Manufacturing is a method to reduce waste and increase efficiency using structured methods. They were developed by Toyota Motor Corporation in Japan during the 1980s. It was designed to produce high-quality products at lower prices while maintaining their quality. Lean manufacturing eliminates unnecessary steps and activities from a production process. It has five components: continuous improvement and pull systems; just-in time; continuous change; and kaizen (continuous innovation). Pull systems involve producing only what the customer wants without any extra work. Continuous improvement means continuously improving on existing processes. Just-in-time is when components and other materials are delivered at their destination in a timely manner. Kaizen means continuous improvement. Kaizen involves making small changes and improving continuously. Five-S stands for sort. It is also the acronym for shine, standardize (standardize), and sustain. These five elements are used together to ensure the best possible results.
The Lean Production System
The lean production system is based on six key concepts:
-
Flow - focus on moving material and information as close to customers as possible;
-
Value stream mapping: This is a way to break down each stage into separate tasks and create a flowchart for the entire process.
-
Five S's - Sort, Set In Order, Shine, Standardize, and Sustain;
-
Kanban - use visual signals such as colored tape, stickers, or other visual cues to keep track of inventory;
-
Theory of constraints: Identify bottlenecks and use lean tools such as kanban boards to eliminate them.
-
Just-in Time - Send components and material directly to the point-of-use;
-
Continuous improvement: Make incremental improvements to the process instead of overhauling it completely.