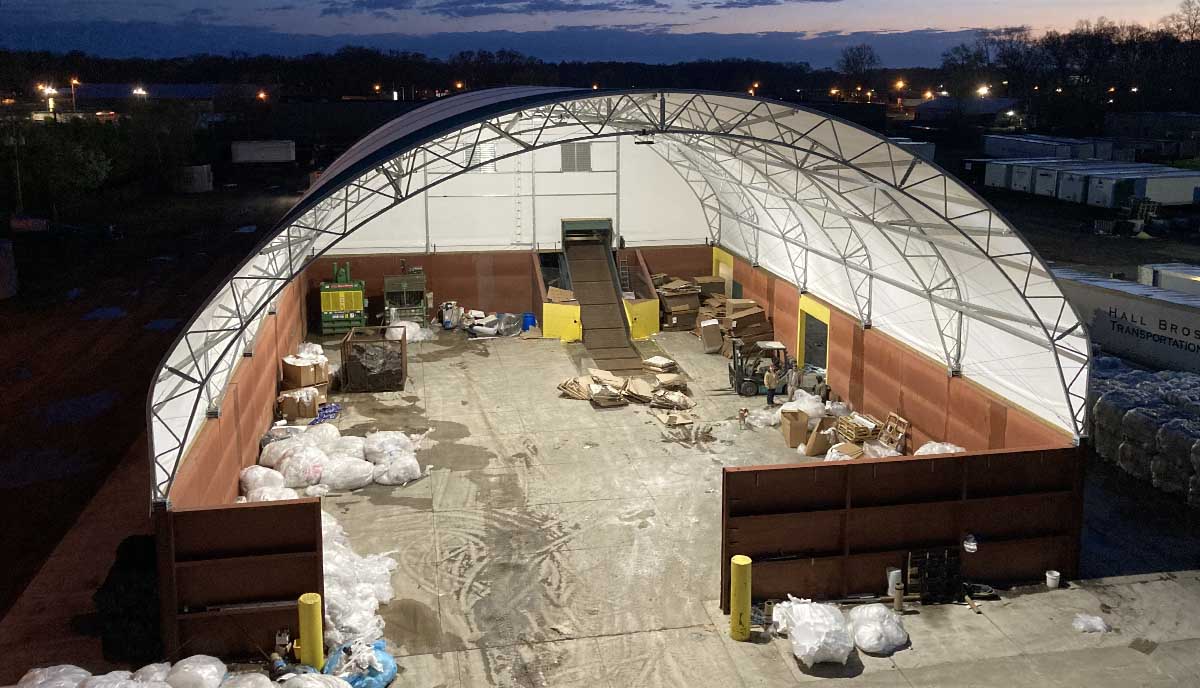
Effective change management training is strategic in nature. It helps leaders guide their teams through transitions, educates employees, and increases the organization's success rates. Efficient change management training will also increase employee engagement, satisfaction, as well as productivity. Learn more by downloading our eBook: Change management training - 5 strategies to increase employee engagement and productivity
It is important to have a strategy for change management.
Designing and delivering effective training sessions is a key strategic skill in change management. Although one-day, massive trainings may not be effective, smaller sessions that are asynchronous and combine live training with job tools and reference materials might prove more efficient. This flexibility allows organizations to respond quickly to changes. This article will give you some tips for creating training sessions that meet your employees' needs.
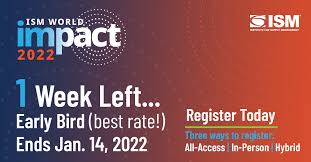
It assists leaders in guiding their teams through the process of change
It takes a combination between people and technical skills to manage change effectively. To be a good leader, you must have the ability to listen to and respect the feelings of your team members. Communication must be strategic, yet heartfelt. Leaders need to show comfort and assurance when employees are feeling anxious or distrustful. Distrustability is more likely when leaders speak but do not act. If a leader is to be a rolemodel, they must also act as one. Employees must feel they are part of the change.
It helps employees understand the change
It is crucial to ensure that employees understand the changes they will face during a change management course. Employees need to be able understand the changes in a meaningful and practical way. To ensure that employees understand the changes occurring, it is important to repeat this training throughout the training. Employees will be better acquainted with the changes if there is a formal statement.
It can help increase the success rate of an organisation
The ability to manage change is essential for employees in order to be able to do their job and to be able to accept new changes. Often, this training focuses on a specific technology, organizational structure, or overall business strategy. The training program will vary depending on what organization it is. It is important to give employees a solid foundation for changing. Below are some essential steps to ensure your employees have the ability to manage change.
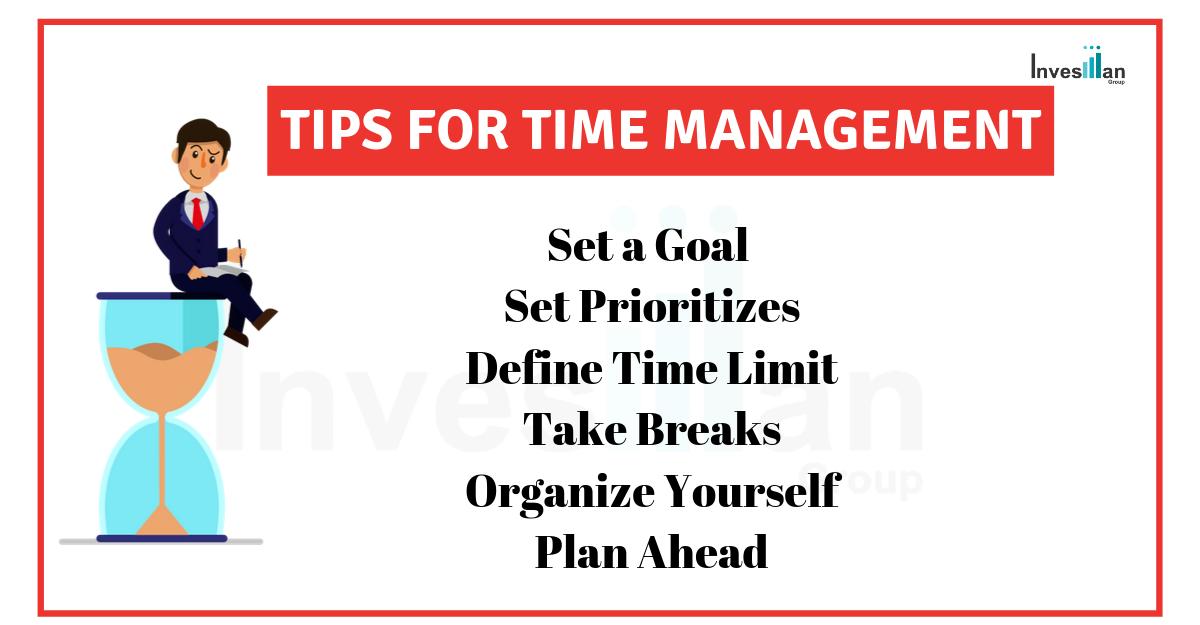
It helps prepare individuals to manage change
Training in change management is designed to help employees accept, implement and manage change. It helps employees understand the whys and hows of change and create better strategies for implementing them. The introduction of change management training will make individuals more passionate about new products or services. This will increase their commitment, and allow them to adapt to new changes. It helps them remain engaged. They will be better equipped to manage change.
FAQ
What are the main styles of management?
There are three types of management: participative, laissez faire, and authoritarian. Each style has its own strengths and weaknesses. Which style do your prefer? Why?
Authority - The leader is the one who sets the direction and expects everyone in the organization to follow it. This style is best when the organization has a large and stable workforce.
Laissez-faire – The leader gives each individual the freedom to make decisions for themselves. This style is best when the organization has a small but dynamic group.
Participative – The leader listens and takes in ideas from all. This style is most effective in smaller organizations, where everyone feels valued.
What are the 5 management processes?
The five stages of a business include planning, execution (monitoring), review, evaluation, and review.
Planning means setting goals for the long-term. It involves setting goals and making plans.
Execution happens when you actually do the plan. These plans must be adhered to by everyone.
Monitoring is checking on progress towards achieving your objectives. Regular reviews should be done of your performance against targets or budgets.
Reviews take place at the end of each year. They provide an opportunity to assess whether everything went well during the year. If not, then it may be possible to make adjustments in order to improve performance next time.
After the annual review, evaluation takes place. It helps to identify what went well and what didn’t. It also gives feedback on how well people did.
What does "project management" mean?
We mean managing the activities involved in carrying out a project.
We help you define the scope of your project, identify the requirements, prepare the budget, organize the team, plan the work, monitor progress and evaluate the results before closing down the project.
What is the difference between TQM and Six Sigma?
The key difference between the two quality management tools is that while six-sigma focuses its efforts on eliminating defects, total quality management (TQM), focuses more on improving processes and reducing cost.
Six Sigma stands for continuous improvement. It emphasizes the elimination of defects by using statistical methods such as control charts, p-charts, and Pareto analysis.
This method aims to reduce variation in product production. This is achieved by identifying and addressing the root causes of problems.
Total quality management is the measurement and monitoring of all aspects within an organization. This includes training employees to improve their performance.
It is commonly used as a strategy for increasing productivity.
What are management concepts?
Management concepts are the principles and practices used by managers to manage people, resources. They include such topics as human resource policies, job descriptions, performance evaluations, training programs, employee motivation, compensation systems, organizational structure, and many others.
Statistics
- 100% of the courses are offered online, and no campus visits are required — a big time-saver for you. (online.uc.edu)
- Our program is 100% engineered for your success. (online.uc.edu)
- The average salary for financial advisors in 2021 is around $60,000 per year, with the top 10% of the profession making more than $111,000 per year. (wgu.edu)
- This field is expected to grow about 7% by 2028, a bit faster than the national average for job growth. (wgu.edu)
- UpCounsel accepts only the top 5 percent of lawyers on its site. (upcounsel.com)
External Links
How To
How do I do the Kaizen Method?
Kaizen means continuous improvement. This Japanese term refers to the Japanese philosophy of continuous improvement that emphasizes incremental improvements and constant improvement. It's a team effort to continuously improve processes.
Kaizen, a Lean Manufacturing method, is one of its most powerful. In this concept, employees who are responsible for the production line must identify problems that exist during the manufacturing process and try to solve them before they become big issues. This is how you can improve the quality and lower the cost.
The main idea behind kaizen is to make every worker aware of what happens around him/her. So that there is no problem, you should immediately correct it if something goes wrong. If someone spots a problem while at work, they should immediately report it to their manager.
Kaizen is based on a few principles. The end product is always our starting point and we work toward the beginning. In order to improve our factory's production, we must first fix the machines producing the final product. We then fix the machines producing components, and the machines producing raw materials. Finally, we repair the workers who are directly involved with these machines.
This method, called 'kaizen', focuses on improving each and every step of the process. When we are done fixing the whole factory, we go back to the beginning and continue until we reach perfection.
It is important to understand how to measure the effectiveness and implementation of kaizen in your company. There are many ways you can determine if kaizen has been implemented well. One way is to examine the amount of defects on the final products. Another method is to determine how much productivity has improved since the implementation of kaizen.
To determine if kaizen is effective, you should ask yourself why you chose to implement kaizen. Is it because the law required it or because you want to save money. Did you really think that it would help you achieve success?
Congratulations! Now you're ready for kaizen.