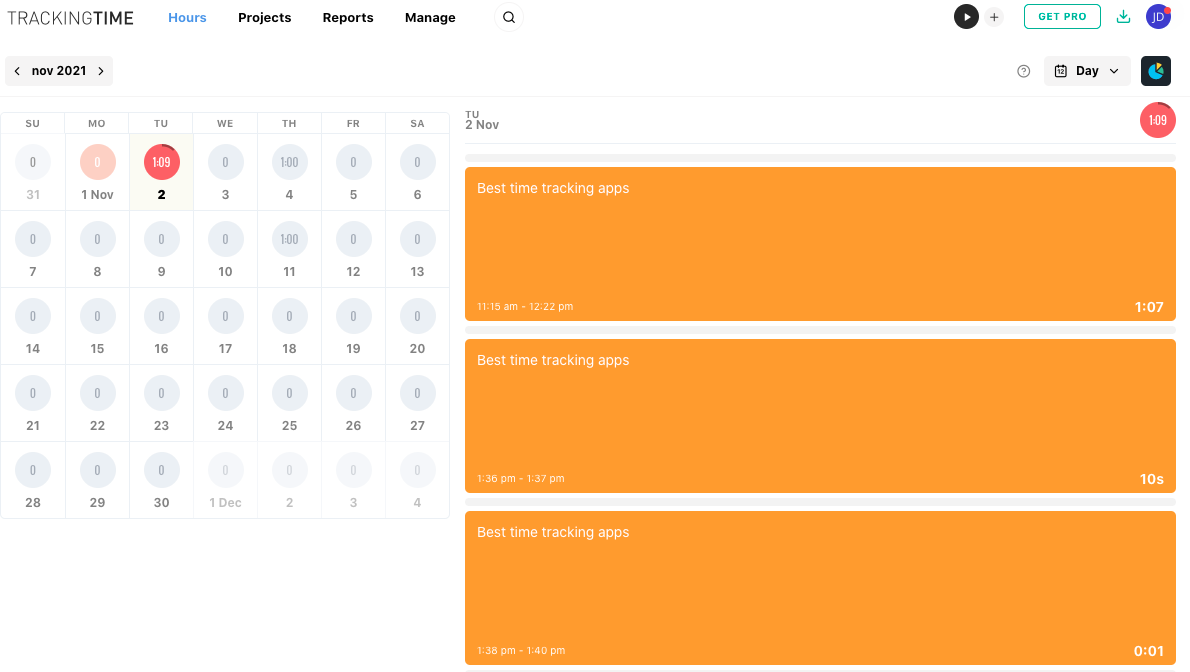
The undergraduate certificate is in facility management. It is intended to expose students to a multidisciplinary approach when it comes to facility operations. It comprises six hours engineering and six hour non-engineering coursework. Students must complete nine hours beyond the requirements for their degree. Students must have completed at least two non-engineering classes outside of the College of Engineering. One course must be from within the College of Engineering. AEEN3350 is required to earn the Certificate in Facility Management. Program advising is provided by the Department of Civil and Architectural Engineering.
Salary ranges for both entry-level managers and experienced facilities managers
A facilities manager is responsible for the overall management of a building or complex, ensuring that it is healthy, safe, sustainable and fit for purpose. The salary for this role varies depending on the level of experience, but can be as high as $150,000 per year. An entry-level facility manager can expect to make between $40K-50K annually. Some companies offer performance-related bonuses or profit share programs.
Facilities managers are mostly responsible for coordinating janitorial and emergency services. These jobs require strong leadership skills and management skills. People with these skills are often promoted into senior positions. There are many opportunities to rise in this field, even though the salary of facilities managers will vary depending upon experience.
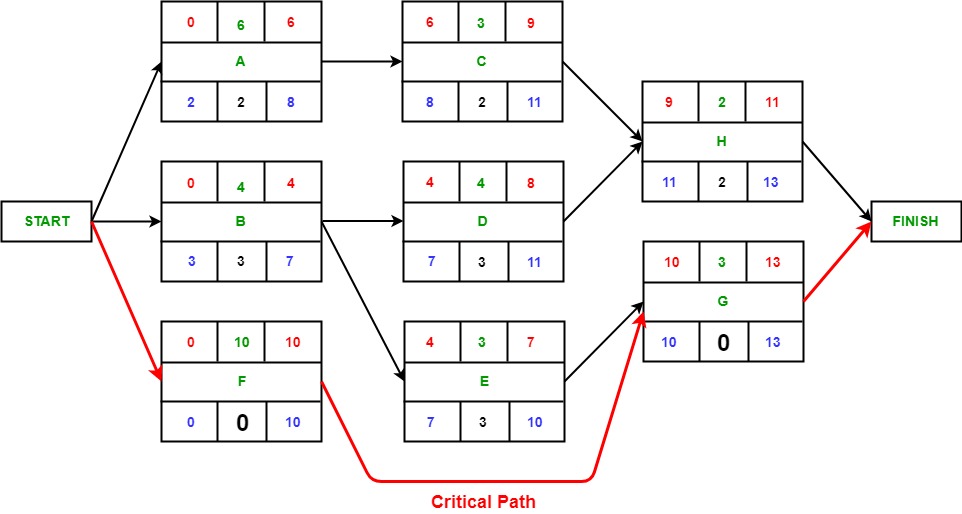
Requirements to apply for the uoft facility management certification
The U of T facility management certificate is a special program that helps professionals coordinate the physical work environment and human needs. The program brings together principles from architecture and business administration with behavioral sciences. The program covers a variety of topics related to facility management including design, construction, leadership, and project management.
The program is suitable for both experienced and novice facilities professionals. It includes core management principles and provides practical tools and training that will help you improve the efficiency and performance of your work environment. This course is available throughout the year without any prerequisites. The cost depends on the student’s professional background, IFMA member status, and copy status. The certificate program also includes a specialization in sustainability, which focuses on environmental and economic aspects of building management.
Guidelines and policies for program evaluation
The U of T facility management certificate program evaluation standards are based on a range of criteria that indicate the quality and effectiveness of the program. The standards focus on quality, integrity, and effectiveness in academic offerings and in the student experience. They were developed based on student feedback and other relevant constituencies.
Students who enroll in this certificate course learn how to critically assess and analyze program evaluations. They will also learn about cost-benefit and process evaluations.
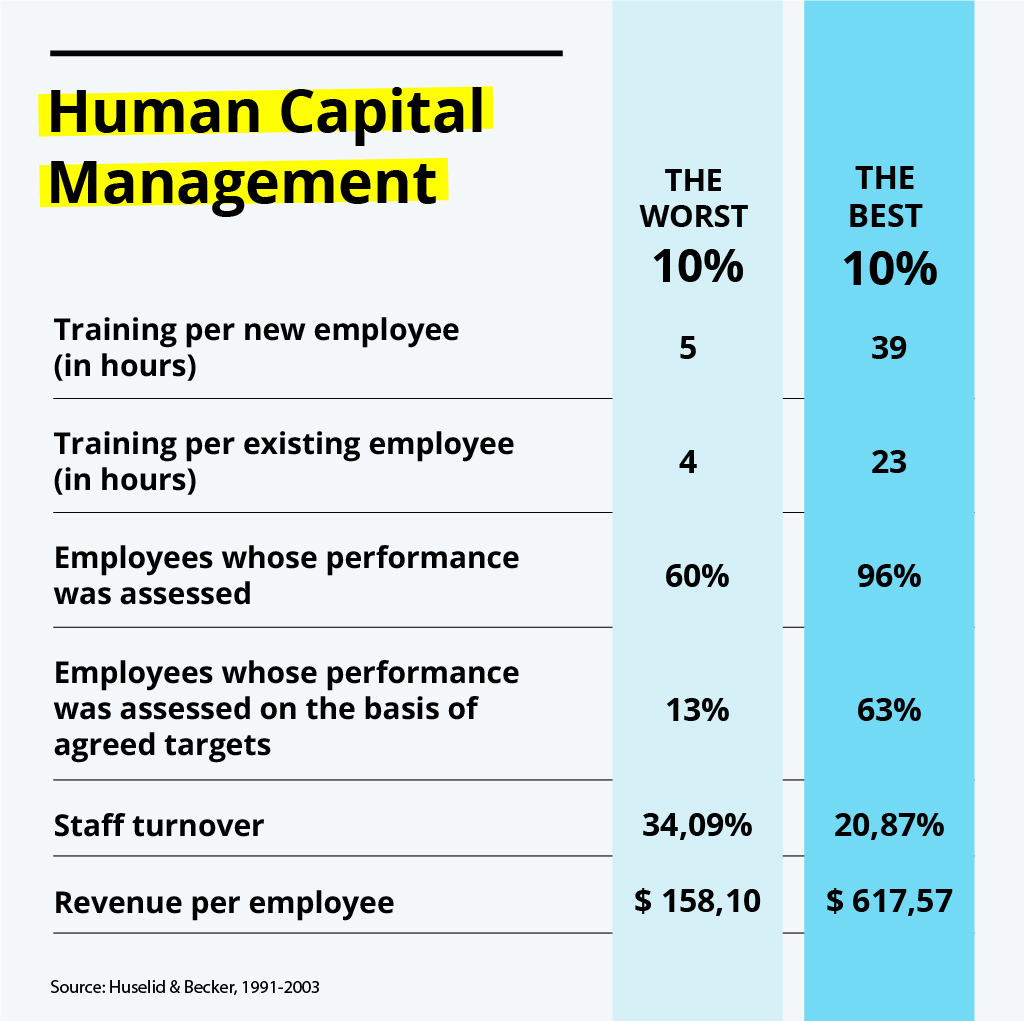
Cost of certificate
The U of T facility management certificate program is a comprehensive program that will give you a broad overview of facility management. You'll learn how to plan and manage buildings, their systems, and how to improve their efficiency and cost effectiveness. Furthermore, you'll learn leadership, construction management and design. You will also learn how you can create and sustain a sustainable environment.
The U of T's facility management certificate program will prepare you to take a bachelor in construction management. No matter what type of building you manage, a facility management certificate will help you make them smarter and more sustainable. This includes knowing how to prepare for emergencies, and ensuring that the building is safe and energy efficient.
FAQ
What are the most common errors made by managers?
Managers can make their jobs more difficult than necessary.
They might not give enough support and delegate the right responsibilities to their staff.
A majority of managers lack the communication skills needed to motivate their team and lead them.
Managers can set unrealistic expectations for their employees.
Managers might try to solve every problem by themselves rather than delegating the responsibility.
What are the four main functions of management?
Management is responsible in planning, organizing and directing people and resources. It also includes developing policies and procedures and setting goals.
Organizations can achieve their goals through management. This includes leadership, coordination, control and motivation.
These are the four major functions of management:
Planning - Planning refers to deciding what is needed.
Organizing: Organizing refers to deciding how things should work.
Directing - Directing means getting people to follow instructions.
Controlling - This is the ability to control people and ensure that they do their jobs according to plan.
What are the 5 management processes?
Each business has five stages: planning, execution and monitoring.
Setting goals for the future is part of planning. It involves setting goals and making plans.
Execution is the actual execution of the plans. They must be followed by all parties.
Monitoring allows you to monitor your progress towards achieving your goals. Regular reviews should be done of your performance against targets or budgets.
At the end of every year, reviews take place. These reviews allow you to evaluate whether the year was successful. If not, then it may be possible to make adjustments in order to improve performance next time.
Evaluation takes place after the annual review. It helps to determine what worked and what didn’t. It also provides feedback on the performance of people.
What are the steps involved in making a decision in management?
Managers are faced with complex and multifaceted decisions. It involves many factors, including but not limited to analysis, strategy, planning, implementation, measurement, evaluation, feedback, etc.
When managing people, the most important thing to remember is that they are just human beings like you and make mistakes. As such, there is always room for improvement, especially if you're willing to put forth the effort to improve yourself first.
We explain in this video how the Management decision-making process works. We discuss the different types of decisions and why they are important, every manager should know how to navigate them. Here are some topics you'll be learning about:
What is Six Sigma?
Six Sigma employs statistical analysis to identify problems, measure them and analyze root causes. Six Sigma also uses experience to correct problems.
First, identify the problem.
Next, data is collected and analyzed to identify trends and patterns.
Then, corrective actions can be taken to resolve the problem.
Finally, data is reanalyzed to determine whether the problem has been eliminated.
This cycle will continue until the problem is solved.
How to effectively manage employees
The key to effective management of employees is ensuring their happiness and productivity.
It means setting clear expectations for them and keeping an eye on their performance.
To do this successfully, managers need to set clear goals for themselves and for their teams.
They should communicate clearly to staff members. They should also ensure that they both reward high performers and discipline those who are not performing to their standards.
They also need to keep records of their team's activities. These include:
-
What was accomplished?
-
How much work were you able to accomplish?
-
Who did it all?
-
When it was done?
-
Why it was done?
This data can be used to evaluate and monitor performance.
What is the role of a manager in a company?
Different industries have different roles for managers.
A manager is generally responsible for overseeing the day to day operations of a company.
He/she is responsible for ensuring that the company meets all its financial obligations and produces the goods or services customers want.
He/she will ensure that employees follow all rules and regulations, and adhere to quality standards.
He/she oversees marketing campaigns and plans new products.
Statistics
- UpCounsel accepts only the top 5 percent of lawyers on its site. (upcounsel.com)
- Hire the top business lawyers and save up to 60% on legal fees (upcounsel.com)
- This field is expected to grow about 7% by 2028, a bit faster than the national average for job growth. (wgu.edu)
- The profession is expected to grow 7% by 2028, a bit faster than the national average. (wgu.edu)
- The average salary for financial advisors in 2021 is around $60,000 per year, with the top 10% of the profession making more than $111,000 per year. (wgu.edu)
External Links
How To
What is Lean Manufacturing?
Lean Manufacturing is a method to reduce waste and increase efficiency using structured methods. They were created by Toyota Motor Corporation in Japan in the 1980s. The goal was to produce quality products at lower cost. Lean manufacturing focuses on eliminating unnecessary steps and activities from the production process. It is composed of five fundamental elements: continuous improvement; pull systems, continuous improvements, just-in–time, kaizen, continuous change, and 5S. The production of only what the customer needs without extra work is called pull systems. Continuous improvement refers to continuously improving existing processes. Just-intime refers the time components and materials arrive at the exact place where they are needed. Kaizen means continuous improvement. Kaizen involves making small changes and improving continuously. Last but not least, 5S is for sort. To achieve the best results, these five elements must be used together.
The Lean Production System
Six key concepts make up the lean manufacturing system.
-
Flow - The focus is on moving information and material as close as possible to customers.
-
Value stream mapping: This is a way to break down each stage into separate tasks and create a flowchart for the entire process.
-
Five S's – Sort, Put In Order Shine, Standardize and Sustain
-
Kanban is a visual system that uses visual cues like stickers, colored tape or stickers to keep track and monitor inventory.
-
Theory of constraints - identify bottlenecks in the process and eliminate them using lean tools like kanban boards;
-
Just-in-time delivery - Deliver components and materials right to your point of use.
-
Continuous improvement - incremental improvements are made to the process, not a complete overhaul.