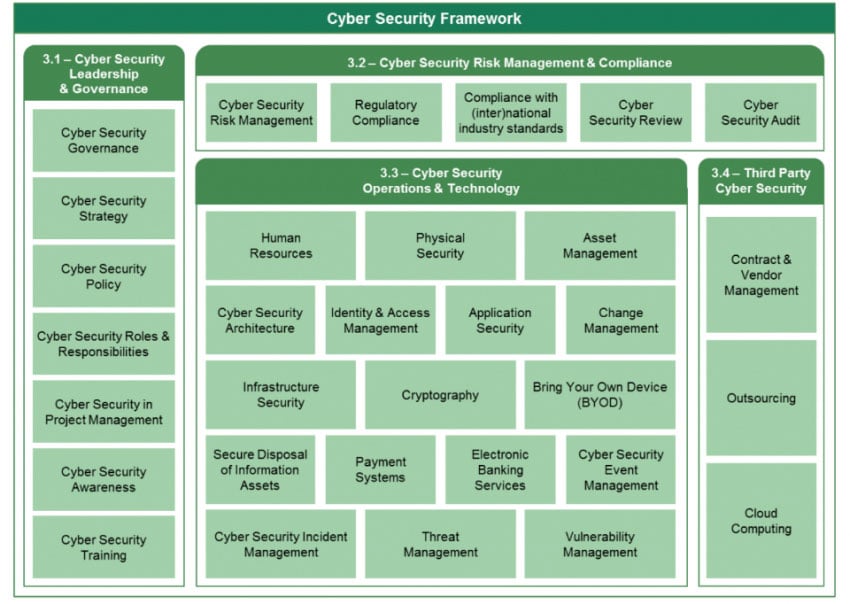
Activity logs are essential components of any IT system. They serve many purposes. They are useful for monitoring your time and energy. They also provide clues to a potential hacker, so it is important to store them for at least a week. Activity logs can be used to manage your time and track your energy use. How do you use them best? Here are some suggestions.
Keep them in your home for at most one week
Activity logs are useful for many reasons. They can be used to keep track of your daily activities and are useful in identifying patterns that you may otherwise miss. It is recommended that you keep your activity logs for no less than one week. However, you can extend this period as often as you wish. You might find it more beneficial to keep activity logs if you have a free hosting account than to keep them for one month.
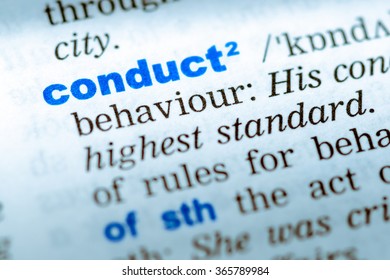
They can also provide clues for hackers
Activity logs can give a lot information about attackers, from personal characteristics to routines. Hackers, for example, often use certain patterns to attack. They might use particular types of malware to attack or only communicate with a single command and control facility. By collecting and analyzing this data, investigators can build a dossier on an attacker and recognize signs of compromise. For instance, an attacker might use the exact same method to download malicious file on a given day.
They can be used as a time-management tool
An activity log is an excellent time management tool. It helps you monitor your time usage and shows you if there are any activities that offer a low return on investment. You can track how much time you spend watching TV or surfing the Internet, for example. This log can be used to track your feelings during various activities. You can adapt your time management to suit your needs by keeping an activity log.
They can be used as energy trackers
Keep a log of your activities to track your energy levels over time. You'll also be able see which times you feel more energetic or drained. You can increase your productivity by tracking your energy level. An activity log will help you to make more of your time and find the best ways to spend it.
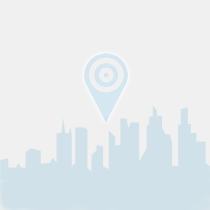
They can be used to monitor employee effectiveness
An employee's performance log can be a valuable tool to assess their effectiveness. This document can be used to track employee performance on a daily basis and to map it to other metrics such as screenshots or audit trails. This document can also be used to record employee suggestions or activities that need further attention. Employees can complete a log on their own, or it can be kept in a file for easy access later.
FAQ
What is Six Sigma?
This is a method of quality improvement that emphasizes customer service, continuous learning, and customer service. The goal is to eliminate defects by using statistical techniques.
Motorola developed Six Sigma in 1986 to help improve its manufacturing processes.
It was quickly adopted by the industry and many companies are now using six-sigma to improve product design, production, delivery, customer service, and product design.
What are the five management process?
Planning, execution, monitoring and review are the five stages of any business.
Setting goals for the future is part of planning. Planning involves defining your goals and how to get there.
Execution is the actual execution of the plans. They must be followed by all parties.
Monitoring is checking on progress towards achieving your objectives. This should involve regular reviews of performance against targets and budgets.
Each year, reviews are held at the end. They allow for an assessment of whether all went well throughout the year. If not, it is possible to make improvements for next year.
After the annual review, evaluation takes place. It helps identify which aspects worked well and which didn't. It also gives feedback on how well people did.
What are the steps of the management decision-making process?
Managers face complex and multifaceted decision-making challenges. This involves many factors including analysis, strategy and planning, implementation, measurement and evaluation, feedback, feedback, and others.
Remember that people are humans just like you, and will make mistakes. This is the key to managing them. You can always improve your performance, provided you are willing to make the effort.
In this video, we explain what the decision-making process looks like in Management. We'll discuss the different types and reasons they are important. Managers should also know how to navigate them. The following topics will be covered:
What are the main four functions of management
Management is responsible of planning, organizing, leading, and controlling people as well as resources. This includes setting goals, developing policies and procedures, and creating procedures.
Management aids an organization in reaching its goals by providing direction and coordination, control, leadership motivation, supervision, training, evaluation, and leadership.
Management's four main functions are:
Planning - Planning is about determining what must be done.
Organizing - Organization involves deciding what should be done.
Directing - Directing is when you get people to do what you ask.
Controlling – Controlling is the process of ensuring that tasks are completed according to plan.
What are some common mistakes managers make?
Managers sometimes make their own job harder than necessary.
They may not delegate enough responsibilities to staff and fail to give them adequate support.
Many managers lack the communication skills to motivate and lead their employees.
Managers can set unrealistic expectations for their employees.
Managers may choose to solve every problem all by themselves, instead of delegating to others.
It seems so difficult sometimes to make sound business decisions.
Complex systems and many moving parts make up businesses. Their leaders must manage multiple priorities, as well as dealing with uncertainty.
It is important to understand the effects of these factors on the system in order to make informed decisions.
To do this, you must think carefully about what each part of the system does and why. Next, consider how each piece interacts with the others.
It is also worth asking yourself if you have any unspoken assumptions about how you have been doing things. If so, it might be worth reexamining them.
Try asking for help from another person if you're still stuck. They might see things differently than you and may have some insights that could help find a solution.
Statistics
- Our program is 100% engineered for your success. (online.uc.edu)
- Hire the top business lawyers and save up to 60% on legal fees (upcounsel.com)
- The BLS says that financial services jobs like banking are expected to grow 4% by 2030, about as fast as the national average. (wgu.edu)
- The average salary for financial advisors in 2021 is around $60,000 per year, with the top 10% of the profession making more than $111,000 per year. (wgu.edu)
- This field is expected to grow about 7% by 2028, a bit faster than the national average for job growth. (wgu.edu)
External Links
How To
How do you do the Kaizen method?
Kaizen means continuous improvement. This Japanese term refers to the Japanese philosophy of continuous improvement that emphasizes incremental improvements and constant improvement. This is a collaborative process in which people work together to improve their processes continually.
Kaizen, a Lean Manufacturing method, is one of its most powerful. This concept requires employees to identify and solve problems during manufacturing before they become major issues. This improves the quality of products, while reducing the cost.
The main idea behind kaizen is to make every worker aware of what happens around him/her. So that there is no problem, you should immediately correct it if something goes wrong. Report any problem you see at work to your manager.
Kaizen follows a set of principles. When working with kaizen, we always start with the end result and move towards the beginning. In order to improve our factory's production, we must first fix the machines producing the final product. Then, we fix the machines that produce components and then the ones that produce raw materials. Finally, we repair the workers who are directly involved with these machines.
This method, called 'kaizen', focuses on improving each and every step of the process. Once we have finished fixing the factory, we return to the beginning and work until perfection.
To implement kaizen in your business, you need to find out how to measure its effectiveness. There are many methods to assess if kaizen works well. One way is to examine the amount of defects on the final products. Another way is determining how much productivity increased after implementing kaizen.
To determine if kaizen is effective, you should ask yourself why you chose to implement kaizen. Is it because the law required it or because you want to save money. It was a way to save money or help you succeed.
Congratulations if you answered "yes" to any of the questions. You're ready to start kaizen.