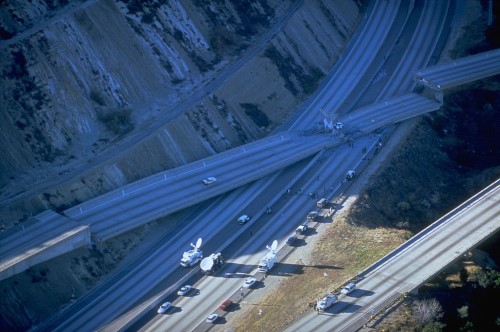
Identifying and implementing methods of managing risk is a critical aspect of surviving the inevitable changes that are inevitable in the modern world. Organizations that adopt a system-based approach to managing risks will be more resilient. But how do you know which methods are best?
You should have the resources to implement risk management strategies. There are many resources available, both internal and external. Those resources must be available at the time needed, and they must be adequately allocated. Risk is minimized when resources are readily available. If resources are not available, risk increases.
The methods of managing risk may include sharing resources, avoiding risk, or transferring risk. These methods can be either structural or non-structural. Using the right strategy, you can spread risk and minimize loss. It may not always be possible to choose the right strategy. However, in modern times, everyone is at risk.
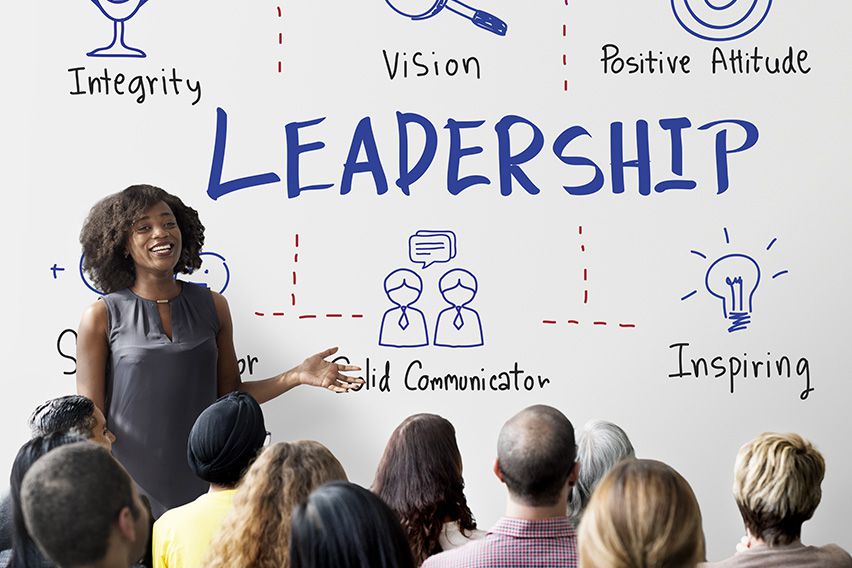
A risk chart helps you visualize potential risks and their consequences. It lists all resources at risk, as well the threats to these resources, and the steps that can be taken in order to mitigate or eliminate those risks.
Another way to visualize danger is by using a bow tie diagram. It is frequently used in the banking and finance industries. It can help you assess the severity of a risk and what it could mean for your company. It can also help identify the differences in risk between two different risks. It's especially useful in quantifying the chance of unexpected equipment failures.
The law based on large numbers can help determine the likelihood of an eventuality. However, fat-tailed distributions could render it obsolete. Moreover, the law of large numbers may not be appropriate for some risks. For example, all department records may be destroyed if a fire breaks out in one room. A fire in a single area may not pose as much risk than one in multiple buildings.
The severity of a loss is another way of measuring the risk. This involves calculating the likelihood of a loss, then measuring the risk remaining after mitigation measures have been implemented. If a loss is likely to occur regularly, you should avoid performing activities that have a high severity of loss. This is also known to be risk reduction.
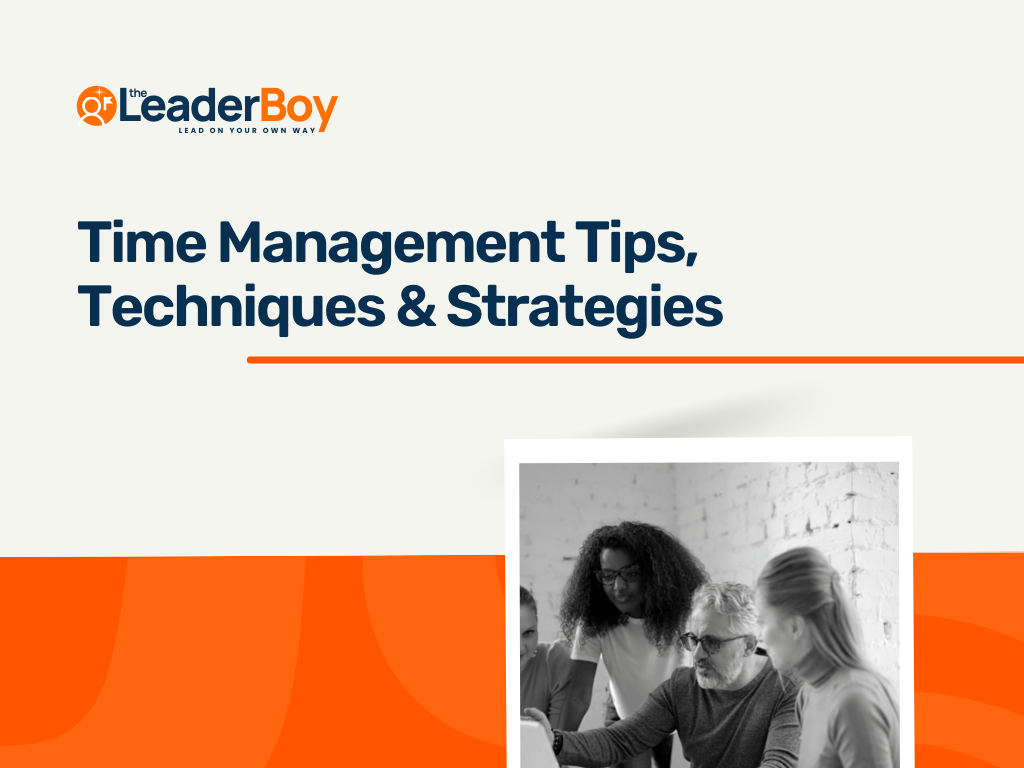
Your company will make the best decision possible by choosing the right risk management methods. The best risk management strategy should be individualized for the organization and should be implemented in the context of its operation. Finding the right methods to manage risk is the first step towards reducing risk, keeping your company healthy, and growing.
Methods of managing risk can be more difficult than they seem. The best strategies for managing risk include implementing systems, aligning these systems, and changing your organization's capability to respond to change. Your people must be able identify opportunities and threats. Your organization should also empower your people to identify threats and opportunities when they arise.
FAQ
What is Six Sigma?
It's a strategy for quality improvement that emphasizes customer care and continuous learning. The goal is to eliminate defects by using statistical techniques.
Motorola's 1986 efforts to improve manufacturing process efficiency led to the creation of Six Sigma.
It was quickly adopted by the industry and many companies are now using six-sigma to improve product design, production, delivery, customer service, and product design.
What are the five management process?
Planning, execution, monitoring and review are the five stages of any business.
Setting goals for the future requires planning. Planning includes setting goals for the future.
Execution happens when you actually do the plan. These plans must be adhered to by everyone.
Monitoring is checking on progress towards achieving your objectives. This should involve regular reviews of performance against targets and budgets.
Review events take place at each year's end. These reviews allow you to evaluate whether the year was successful. If not, it is possible to make improvements for next year.
After the annual review, evaluation takes place. It helps to identify what went well and what didn’t. It also provides feedback regarding how people performed.
What is the difference between TQM and Six Sigma?
The major difference between the two tools for quality management is that six Sigma focuses on eliminating defect while total quality control (TQM), on improving processes and decreasing costs.
Six Sigma can be described as a strategy for continuous improvement. It emphasizes the elimination or minimization of defects through statistical methods such control charts and p charts.
This method aims to reduce variation in product production. This is achieved by identifying and addressing the root causes of problems.
Total quality management is the measurement and monitoring of all aspects within an organization. Training employees is also part of total quality management.
It is often used to increase productivity.
What are the main styles of management?
There are three main management styles: participative, laissez-faire and authoritarian. Each style has its strengths and weaknesses. Which style do you prefer? Why?
Autoritarian – The leader sets the direction for everyone and expects them to follow. This style is best when the organization has a large and stable workforce.
Laissez-faire: The leader lets each person decide for themselves. This approach works best in small, dynamic organizations.
Participative – Leaders are open to suggestions and ideas from everyone. This is a great style for smaller organizations that value everyone.
Statistics
- Hire the top business lawyers and save up to 60% on legal fees (upcounsel.com)
- Our program is 100% engineered for your success. (online.uc.edu)
- The BLS says that financial services jobs like banking are expected to grow 4% by 2030, about as fast as the national average. (wgu.edu)
- UpCounsel accepts only the top 5 percent of lawyers on its site. (upcounsel.com)
- Your choice in Step 5 may very likely be the same or similar to the alternative you placed at the top of your list at the end of Step 4. (umassd.edu)
External Links
How To
How do you do the Kaizen method?
Kaizen means continuous improvement. Kaizen is a Japanese concept that encourages constant improvement by small incremental changes. This is a collaborative process in which people work together to improve their processes continually.
Kaizen is one of Lean Manufacturing's most efficient methods. The concept involves employees responsible for manufacturing identifying problems and trying to fix them before they become serious issues. This improves the quality of products, while reducing the cost.
The main idea behind kaizen is to make every worker aware of what happens around him/her. Correct any errors immediately to avoid future problems. Report any problem you see at work to your manager.
Kaizen follows a set of principles. When working with kaizen, we always start with the end result and move towards the beginning. In order to improve our factory's production, we must first fix the machines producing the final product. Next, we fix the machines which produce components. Then, we fix those who work directly with the machines.
This method, called 'kaizen', focuses on improving each and every step of the process. When we are done fixing the whole factory, we go back to the beginning and continue until we reach perfection.
How to measure kaizen's effectiveness in your business is essential to implement it. There are several ways to determine whether kaizen is working well. One way is to examine the amount of defects on the final products. Another way is to see how much productivity has increased since implementing kaizen.
If you want to find out if your kaizen is actually working, ask yourself why. Is it because the law required it or because you want to save money. Did you really believe that it would be a success factor?
Congratulations! You're ready to start kaizen.