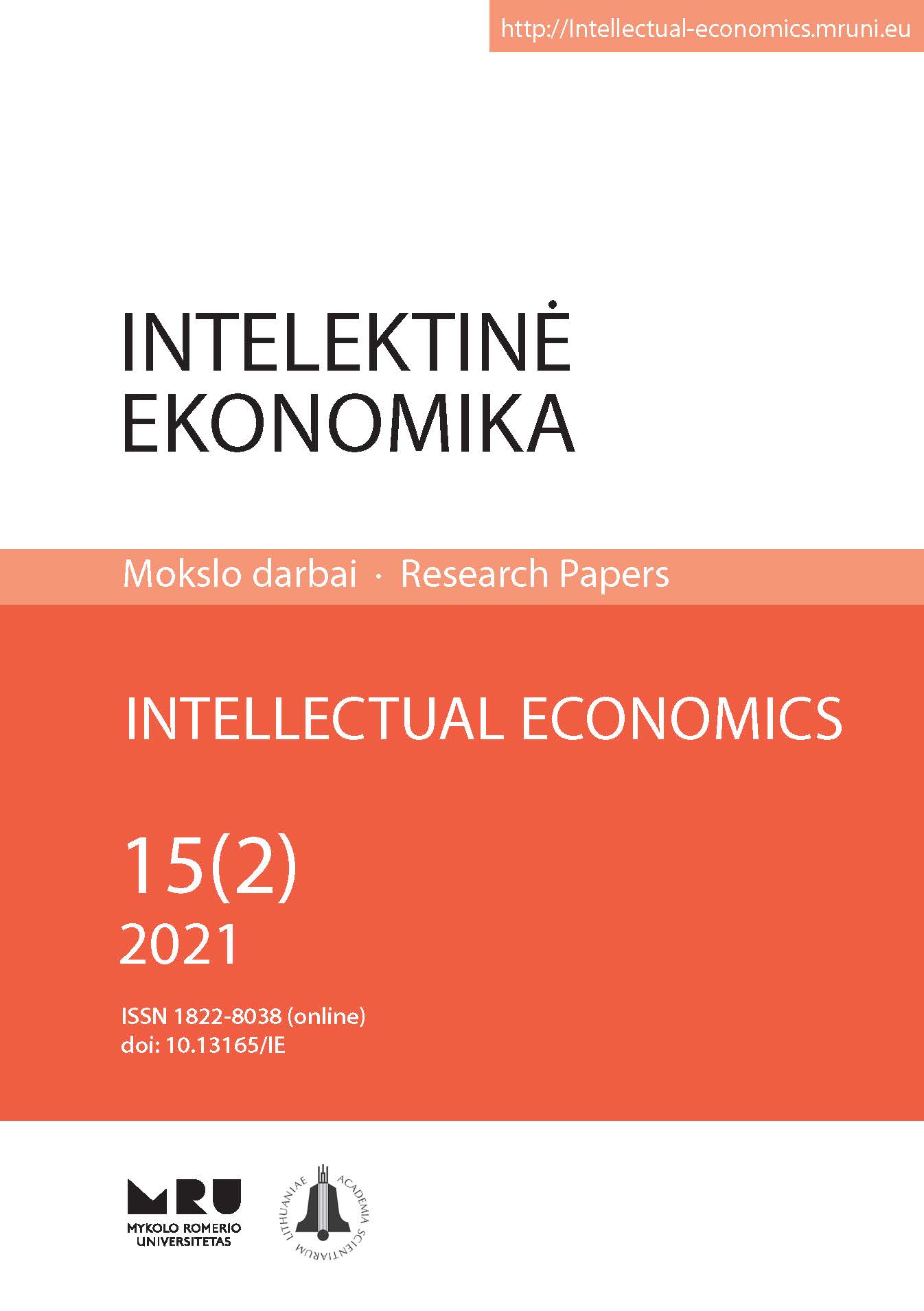
Process safety management refers to a disciplined approach to managing the integrity of operating systems and processes within a facility. This system must be up-to-date at least five years after it is established. Process safety management is designed to prevent accidents. These are the steps you need to follow to implement process safety management. These steps will make your facility as safe as possible, and prevent accidents.
Process safety management can be described as a disciplined framework that manages the integrity of operating system and process processes.
The goal of process safety management (PSM) is to minimize the likelihood of incidents and improve productivity. It focuses on controlling risks within the plant and inherently safer equipment. It requires strict adherence and assessment of hazards. It includes training and maintenance, along with process control. It is an integral part of any safety-conscious organization.
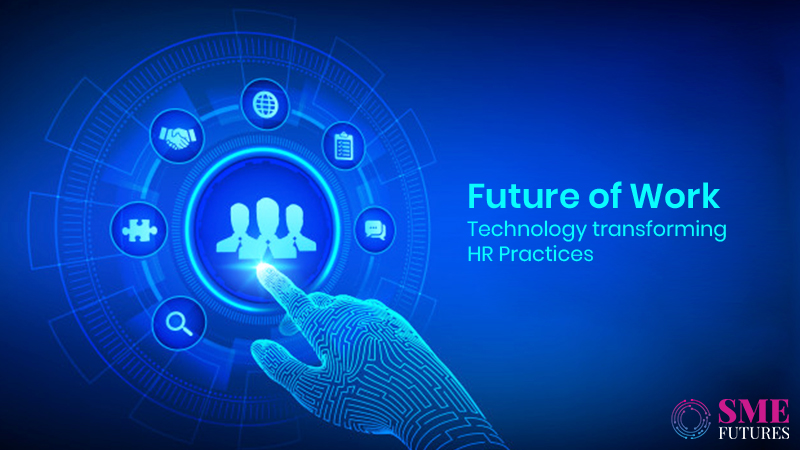
It should be updated at least every 5 years
OSHA (Occupational Safety and Health Administration) requires that process safety information be regularly reviewed and updated. This includes the creation and maintenance of process safety information and written procedures. This information must be available to all employees involved in the process. For five years, written procedures and reports must be retained. Employees must have access to current process safety information that they can review and follow. An employer may seek out safety risk management consulting to help them meet their requirements.
It is a legal requirement to have major hazard equipment.
All major hazard facilities are required to have a process safety system. Employers are required to implement a process for safe and prompt evacuation of employees. In most cases, the plan includes a safety alert that will notify employees to evacuate. It should also contain emergency procedures to aid employees who are not physically able to evacuate the hazardous zone.
It helps prevent incidents
A well-designed process safety system can help improve profitability, safety performance, as well as quality. It can also help improve the company’s environmental responsibility. It also reduces the chance of accidents. These are all vital areas to ensure the company's long-term success. Below is a short overview of the numerous benefits of a safety management system. It is a system that helps companies prevent and reduce accidents, as well as improve the safety and health of employees and customers.
It is a time-consuming process
The process safety management of hazardous chemical facilities can be complex and time-consuming. Even if OSHA doesn't regulate process safety management programs, it does require facilities to have a written plan for implementation and to meet 14 minimum requirements. Some companies rely heavily on spreadsheets, forms and forms to collect information and compile risk analyses and other information. This is time-consuming, and there is a risk of human error.
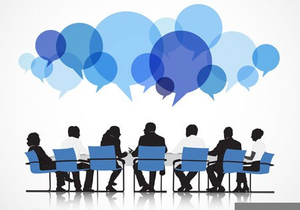
It involves employee participation
The Pennsylvania State University adopted a PSM program that includes an Employee Participation element. This element takes advantage of employees' experience, knowledge, and unique perspectives in order to improve safety. The program lists the requirements and describes the mechanisms available for employee participation. It is vital to include all employees into the process safety process management process. For serious incidents to be avoided, it is vital that employees participate in PSM. But, how do you ensure that all employees are engaged in the program?
FAQ
What are management theories?
Management concepts are the practices and principles managers use to manage people or resources. They cover topics like job descriptions (job descriptions), performance evaluations, training programmes, employee motivation and compensation systems.
Why is it important that companies use project management methods?
Project management techniques ensure that projects run smoothly while meeting deadlines.
This is because most businesses rely on project work for their products and services.
These projects are essential for companies.
Companies may lose their reputation, time and money if they do not have effective project management.
How can a manager motivate employees?
Motivation can be defined as the desire to achieve success.
Enjoyable activities can motivate you.
You can also be motivated by the idea of making a difference to the success and growth of your organization.
For example: If you want to be a doctor, you might find it more motivating seeing patients than reading medical books all day.
Motivation comes from within.
One example is a strong sense that you are responsible for helping others.
Perhaps you enjoy working hard.
If you don't feel motivated, ask yourself why.
Then, consider ways you could improve your motivation.
Statistics
- Your choice in Step 5 may very likely be the same or similar to the alternative you placed at the top of your list at the end of Step 4. (umassd.edu)
- Our program is 100% engineered for your success. (online.uc.edu)
- This field is expected to grow about 7% by 2028, a bit faster than the national average for job growth. (wgu.edu)
- 100% of the courses are offered online, and no campus visits are required — a big time-saver for you. (online.uc.edu)
- UpCounsel accepts only the top 5 percent of lawyers on its site. (upcounsel.com)
External Links
How To
How is Lean Manufacturing done?
Lean Manufacturing techniques are used to reduce waste while increasing efficiency by using structured methods. They were developed by Toyota Motor Corporation in Japan during the 1980s. It was designed to produce high-quality products at lower prices while maintaining their quality. Lean manufacturing emphasizes removing unnecessary steps from the production process. It has five components: continuous improvement and pull systems; just-in time; continuous change; and kaizen (continuous innovation). Pull systems involve producing only what the customer wants without any extra work. Continuous improvement involves constantly improving upon existing processes. Just-in-time refers to when components and materials are delivered directly to the point where they are needed. Kaizen means continuous improvement, which is achieved by implementing small changes continuously. Last but not least, 5S is for sort. These five elements work together to produce the best results.
The Lean Production System
Six key concepts underlie the lean production system.
-
Flow - focus on moving material and information as close to customers as possible;
-
Value stream mapping- This allows you to break down each step of a process and create a flowchart detailing the entire process.
-
Five S's – Sort, Put In Order Shine, Standardize and Sustain
-
Kanban is a visual system that uses visual cues like stickers, colored tape or stickers to keep track and monitor inventory.
-
Theory of Constraints - Identify bottlenecks in the process, and eliminate them using lean tools such kanban boards.
-
Just-in-time - deliver components and materials directly to the point of use;
-
Continuous improvement is making incremental improvements to your process, rather than trying to overhaul it all at once.