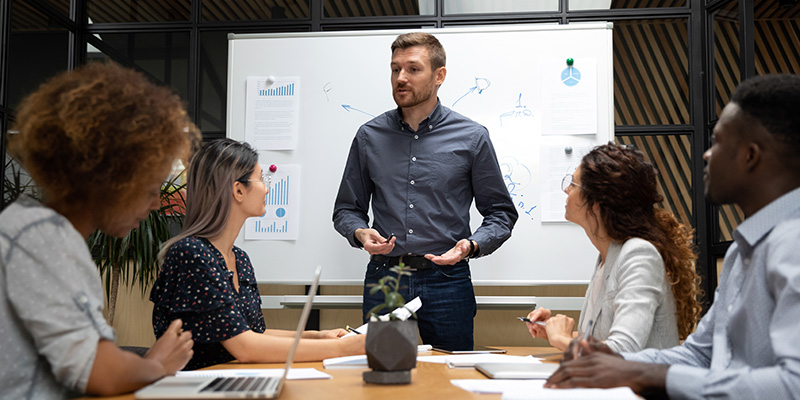
Integrated supply chain management is an integrated approach to managing a company. It involves the "cradle to grave" management of a business. This management approach involves asymmetrical relationships between buyers or sellers. It aims to improve quality and decrease costs. It includes visibility at all stages of the supply chain. This is an important part of fully integrated supply chains. Not all companies are keen to adopt this approach.
Integrated supply chain management can be described as a "cradle–to-grave" approach.
Integrated supply chain management encompasses all aspects of the product's life cycle. It includes raw materials, consumer products, and information flows. It involves forward and reverse logistics, information flows, and cash flows, typically from producers to distributors to retailers. The ultimate goal here is to minimize waste while maximising benefits for the consumer. To do this, supply chain managers must understand how to utilize outside resources and recycle materials at the end of their life cycles.
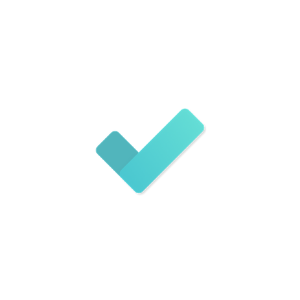
It is marked by adversarial relationships between buyers, sellers, and other participants
The process of integrating supply chain management involves reducing the number of transactions and maximizing the performance of the supply chain. It requires disciplined management skills, technologies and processes. Additionally, it requires a focus on key capabilities. The ultimate goal is higher profitability and reduced risk to all participants. This is often difficult to achieve in the current global economic climate. However, integrating supply-chain management can be cost-effective and profitable if you follow some basic principles.
It lowers your costs
Integrated supply chain management can reduce costs for your business in many ways. First of all, you will need to make sure your suppliers meet your specifications and that their prices match your expectations. You should also choose vendors who have a good reputation and can deliver the goods on time. This is particularly important if you deal with perishable goods. Implementing efficient supply chain management techniques can improve the efficiency of your company.
It improves quality
Integrated supply chain management allows for a single view of the entire supply chain. This central view can be updated easily without having to purchase software or hardware. It makes the supply chain flexible and scalable. Organizations can make better business decisions, work with vendors, and leverage real-time data to improve their planning. All involved win. Below are just a few benefits to integrating your supply-chain.
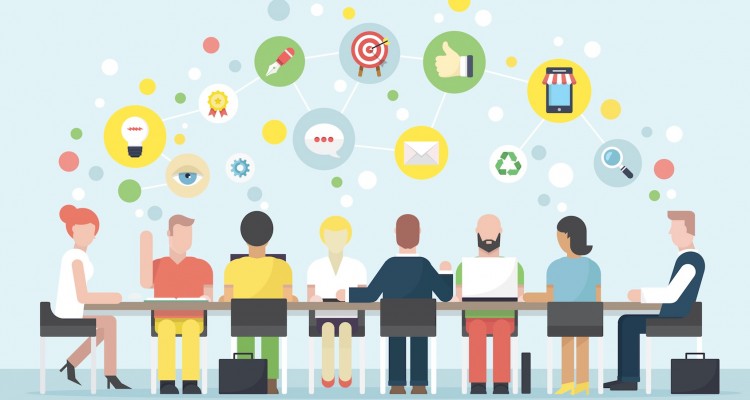
It allows for rapid product design, fabrication, and assembly
With integrated supply chains management, manufacturers are now able design and manufacture full products in much less time than they used to. This trend can reduce material wastage and warehouse costs. Also, on-demand production offers better customer services. The only downside is the steep learning curve. But, it is possible to create products in as little as one day using new materials and hardware. It can also enhance the product's quality.
FAQ
What are the steps to take in order to make a management decision?
Managers face complex and multifaceted decision-making challenges. It involves many factors, such as analysis and strategy, planning, execution, measurement, evaluation, feedback etc.
It is important to remember that people are human beings, just like you. They make mistakes. You can always improve your performance, provided you are willing to make the effort.
In this video, we explain what the decision-making process looks like in Management. We will explain the importance of different types decisions and how every manager can make them. The following topics will be covered.
Why is it important that companies use project management methods?
Project management techniques are used in order to ensure projects run smoothly, and that deadlines are met.
This is because many businesses depend heavily upon project work to produce products and services.
Companies must manage these projects effectively and efficiently.
Companies could lose their time, reputation, and money without effective project management.
What are management concepts, you ask?
Management Concepts are the principles and practices managers use to manage people and resources. These include topics such as human resource policies and job descriptions, performance assessments, training programs and employee motivation.
How do you effectively manage employees?
Achieving employee happiness and productivity is key to managing them effectively.
It is important to set clear expectations about their behavior and keep track of their performance.
To do this successfully, managers need to set clear goals for themselves and for their teams.
They must communicate clearly with their staff. They should also ensure that they both reward high performers and discipline those who are not performing to their standards.
They also need to keep records of their team's activities. These include:
-
What did we accomplish?
-
How much work did you put in?
-
Who did it and why?
-
Was it done?
-
Why was it done?
This data can be used to evaluate and monitor performance.
It seems so difficult sometimes to make sound business decisions.
Complex systems with many moving parts are the hallmark of businesses. They require people to manage multiple priorities and deal with uncertainty and complexity.
To make good decisions, you must understand how these factors affect the entire system.
To do this, you must think carefully about what each part of the system does and why. It is important to then consider how the individual pieces relate to each other.
Ask yourself if there are hidden assumptions that have influenced your behavior. You might consider revisiting them if they are not.
You can always ask someone for help if you still have questions after all of this. They might have different perspectives than you, and could offer insight that could help you solve your problem.
What is a basic management tool that can be used for decision-making?
A decision matrix is an easy but powerful tool to aid managers in making informed decisions. It allows them to consider all possible solutions.
A decision matrix allows you to represent alternatives as columns and rows. This makes it easy for you to see how each option affects other options.
We have four options in this example. They are represented by the boxes to the left of the matrix. Each box represents one option. The top row shows the status quo (the current situation), and the bottom row shows what would happen if nothing was done at all.
The middle column displays the impact of selecting Option 1. In this example, it would lead to an increase in sales of between $2 million and $3 million.
These are the results of selecting Options 2 or 3. These are good changes, they increase sales by $1million or $500,000. But, they also have some negative consequences. For instance, Option 2 increases cost by $100 thousand while Option 3 reduces profits by $200 thousand.
Finally, the last column shows the results of choosing Option 4. This results in a decrease of sales by $1,000,000
The best part about using a decision matrix to guide you is that you don’t need to keep track of which numbers go where. The best thing about a decision matrix is that you can simply look at the cells, and immediately know whether one option is better or not.
This is because the matrix has already taken care of the hard work for you. It is as simple a matter of comparing all the numbers in each cell.
Here's an example of how you might use a decision matrix in your business.
You need to decide whether to invest in advertising. This will allow you to increase your revenue by $5000 per month. However, additional expenses of $10 000 per month will be incurred.
By looking at the cell just below "Advertising", the net result can be calculated as $15 thousand. Advertising is a worthwhile investment because it has a higher return than the costs.
What is Six Sigma?
This is a method of quality improvement that emphasizes customer service, continuous learning, and customer service. This is an approach to quality improvement that uses statistical techniques to eliminate defects.
Motorola developed Six Sigma in 1986 to help improve its manufacturing processes.
It was quickly adopted by the industry and many companies are now using six-sigma to improve product design, production, delivery, customer service, and product design.
Statistics
- The profession is expected to grow 7% by 2028, a bit faster than the national average. (wgu.edu)
- The BLS says that financial services jobs like banking are expected to grow 4% by 2030, about as fast as the national average. (wgu.edu)
- Hire the top business lawyers and save up to 60% on legal fees (upcounsel.com)
- As of 2020, personal bankers or tellers make an average of $32,620 per year, according to the BLS. (wgu.edu)
- Your choice in Step 5 may very likely be the same or similar to the alternative you placed at the top of your list at the end of Step 4. (umassd.edu)
External Links
How To
How does Lean Manufacturing work?
Lean Manufacturing is a method to reduce waste and increase efficiency using structured methods. These processes were created by Toyota Motor Corporation, Japan in the 1980s. The main goal was to produce products at lower costs while maintaining quality. Lean manufacturing eliminates unnecessary steps and activities from a production process. It consists of five basic elements: pull systems, continuous improvement, just-in-time, kaizen (continuous change), and 5S. Pull systems are able to produce exactly what the customer requires without extra work. Continuous improvement refers to continuously improving existing processes. Just-in-time refers to when components and materials are delivered directly to the point where they are needed. Kaizen is continuous improvement. This can be achieved by making small, incremental changes every day. The 5S acronym stands for sort in order, shine standardize and maintain. To achieve the best results, these five elements must be used together.
Lean Production System
The lean production system is based on six key concepts:
-
Flow - focus on moving material and information as close to customers as possible;
-
Value stream mapping - break down each stage of a process into discrete tasks and create a flowchart of the entire process;
-
Five S's – Sort, Put In Order Shine, Standardize and Sustain
-
Kanban - visual cues such as stickers or colored tape can be used to track inventory.
-
Theory of constraints - identify bottlenecks during the process and eliminate them with lean tools like Kanban boards.
-
Just-in time - Get components and materials delivered right at the point of usage;
-
Continuous improvement: Make incremental improvements to the process instead of overhauling it completely.