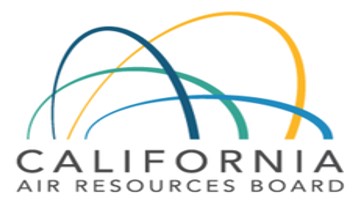
This article discusses organizational change management tools and the processes involved. The next section focuses on the results from change management initiatives. These results will decide whether or not the initiative was successful. Organizations should have a communication strategy in place to encourage employees' feedback and concerns to be shared with management. It will be difficult to implement any change without communication. This article will focus on three important elements that make change management successful.
Organizational change
Human Resource professionals involved in organizational initiatives must manage change. This seminar will provide participants with a practical guide to management of change. Participants also experience simulations of various major phases of change. Participants receive a Learning Reinforcement Kit after the seminar. This toolkit provides additional resources that will help them continue their education beyond the classroom.
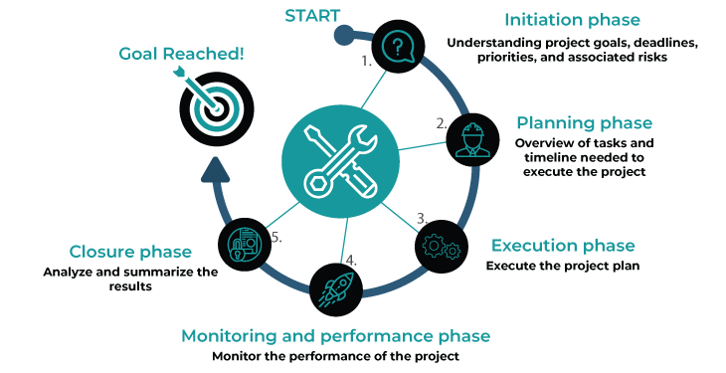
Process
The process of SHRM change management is a multi-staged approach that includes the assessment of an organization's employees' capabilities to deal with the change. The changes that are a part of the change process are often difficult to implement, but HR professionals can lead these efforts with their basic organizational design principles. The process includes creating new, more efficient teams, running assessment centres, and setting up fair and effective selection processes.
Tools
HR professionals can use tools to manage changes more effectively and efficiently. Tools such as Scribe make it easy to document changes and ensure that processes are uniform across teams. They can automatically generate step screenshots and written instructions, and let users modify them in the future. They can also easily be shared using links and shared workspaces. This makes it possible to track the impact of every change and make necessary changes.
Results
SHRM's SHRM Change Management Study revealed that more organizations still use informal approaches to managing change despite having evidence-based methods. The study also found that implementing formal change management processes was associated with increased overall effectiveness of initiated change efforts. The results of this study highlight the need for both formal and informal change management processes to be more effective in addressing the challenges of change. Organizations should use both formal and informal approaches to manage change effectively and attain desired results.
The role of HR
HR can play multiple roles in an organizational change. HR is responsible for implementing changes when external forces require them. It also facilitates change when necessary to improve processes and technology. Depending on the business's needs and current conditions, the HR department often makes these changes possible. Here are some of the ways HR professionals can facilitate change.
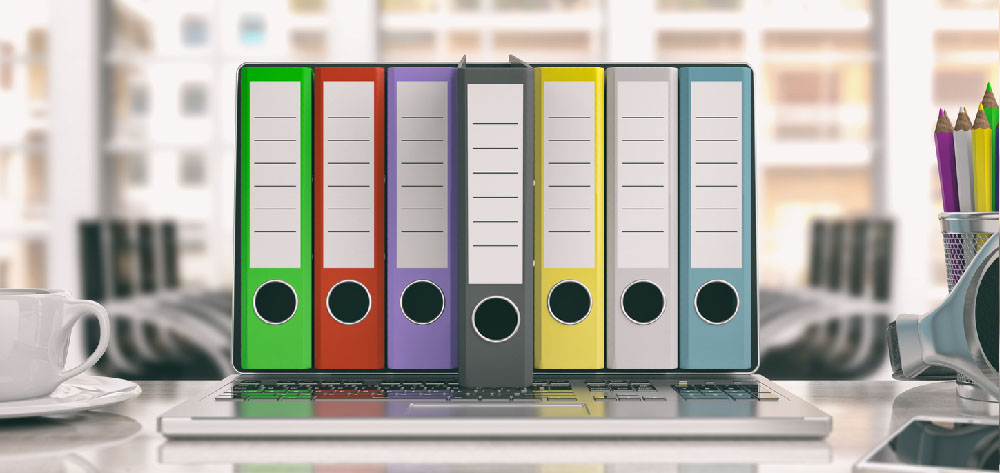
Future research
The Society for Human Resource Management (SHRM) provides information on change management, major transformations, and employee support. HR professionals know the skills and abilities needed to make change work and are active participants in the process. HR has two roles in workplace change management. As the initiator and catalyst of change, HR also plays an important role. Many initiatives include both change management and human resources.
FAQ
What are management concepts, you ask?
Management concepts are the fundamental principles and practices that managers use when managing people and their resources. They cover topics such as job descriptions and performance evaluations, human resource policies, training programs, employee motivation, compens systems, organizational structure, among others.
What is Six Sigma?
It's an approach to quality improvement that emphasizes customer service and continuous learning. The goal is to eliminate defects by using statistical techniques.
Motorola developed Six Sigma in 1986 to help improve its manufacturing processes.
This idea quickly spread throughout the industry. Today, many organizations use six sigma methods for product design, production and delivery.
What's the difference between leadership & management?
Leadership is about inspiring others. Management is about controlling others.
A leader inspires his followers while a manager directs the workers.
A leader motivates people to achieve success; a manager keeps workers on task.
A leader develops people; a manager manages people.
What is the difference between TQM and Six Sigma?
The key difference between the two quality management tools is that while six-sigma focuses its efforts on eliminating defects, total quality management (TQM), focuses more on improving processes and reducing cost.
Six Sigma stands for continuous improvement. It emphasizes the elimination and improvement of defects using statistical methods, such as control charts, P-charts and Pareto analysis.
This method aims to reduce variation in product production. This is done by identifying and correcting the root causes of problems.
Total Quality Management involves monitoring and measuring every aspect of the organization. Training employees is also part of total quality management.
It is used to increase productivity.
What is Kaizen, exactly?
Kaizen is a Japanese term for "continuous improvement." It encourages employees constantly to look for ways that they can improve their work environment.
Kaizen is based on the belief that every person should be able to do his or her job well.
How do you define Six Sigma?
Six sigma is a common concept for people who have worked in statistics or operations research. Anyone involved in business can benefit.
Because it requires a high level of commitment, only those with strong leadership skills will make an effort necessary to implement it successfully.
Statistics
- The BLS says that financial services jobs like banking are expected to grow 4% by 2030, about as fast as the national average. (wgu.edu)
- This field is expected to grow about 7% by 2028, a bit faster than the national average for job growth. (wgu.edu)
- UpCounsel accepts only the top 5 percent of lawyers on its site. (upcounsel.com)
- Your choice in Step 5 may very likely be the same or similar to the alternative you placed at the top of your list at the end of Step 4. (umassd.edu)
- Our program is 100% engineered for your success. (online.uc.edu)
External Links
How To
How does Lean Manufacturing work?
Lean Manufacturing methods are used to reduce waste through structured processes. They were created in Japan by Toyota Motor Corporation during the 1980s. The aim was to produce better quality products at lower costs. Lean manufacturing eliminates unnecessary steps and activities from a production process. It includes five main elements: pull systems (continuous improvement), continuous improvement (just-in-time), kaizen (5S), and continuous change (continuous changes). The production of only what the customer needs without extra work is called pull systems. Continuous improvement is the continuous improvement of existing processes. Just-in time refers to components and materials being delivered right at the place they are needed. Kaizen means continuous improvement. Kaizen involves making small changes and improving continuously. The 5S acronym stands for sort in order, shine standardize and maintain. These five elements are used together to ensure the best possible results.
Lean Production System
Six key concepts make up the lean manufacturing system.
-
Flow - focuses on moving information and materials as close to customers as possible.
-
Value stream mapping is the ability to divide a process into smaller tasks, and then create a flowchart that shows the entire process.
-
Five S's – Sort, Put In Order Shine, Standardize and Sustain
-
Kanban is a visual system that uses visual cues like stickers, colored tape or stickers to keep track and monitor inventory.
-
Theory of Constraints - Identify bottlenecks in the process, and eliminate them using lean tools such kanban boards.
-
Just-in time - Get components and materials delivered right at the point of usage;
-
Continuous improvement - make incremental improvements to the process rather than overhauling it all at once.